Krone unveils first non-stop round baler
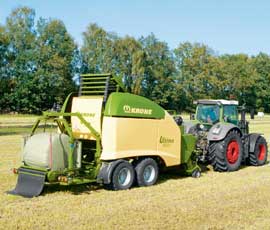
It’s here at last – the world’s first commercial non-stop round baler/wrapper. Designed and built by Krone, the Ultima promises to almost double the output of round baling.
The challenge of producing a non-stop round baler has occupied the minds of designers for more than few years but, until now at least, there has not been a successful version that has made it commercially.
Krone, which admits to trying out a system in the 1980s, points out that there are fundamentally two problems to overcome – one is what to do with the incoming crop while the completed bale is being net wrapped and ejected. The other is how to ensure the density of the bale is maintained when the accumulated crop is released into the empty chamber.
Density is the problem
According to Krone’s Ingo Schoppe, who has been closely involved with the Ultima’s development, it is the density that has posed the biggest problem.
“We had to find a way of accumulating the crop outside the chamber and ensuring that when it was fed into it, it wasn’t just a loose pile that would be difficult for the chamber to produce a bale with suitable density,” he says.
The solution has been to create a pre-compression chamber which is fed and filled by the front rotor and comprises a top and bottom belt – the tapering gap between them creating the chamber.
How does it work?
• It starts with the pick-up and centralising auger, which guides the crop to the intake rotor. It is possible to chop the crop at this stage using a conventional bank of knives though which the rotor forces the crop.
• The crop now enters the pre-compression chamber. If the bale chamber is not net wrapping a bale, the crop flows on into the chamber using the top and lower belts to move it along.
• If a completed bale is being net wrapped and the path to the chamber is not available, the belts don’t move and the crop is allowed to build up between them. Compressed comes from the incoming crop.
• Mr Schoppe points out that there needs to be sufficient capacity to store 45 seconds’ worth of crop, which is the amount of time it takes to net wrap, eject the bale on to the film-wrapping table and set up the bale chamber for the start of the next bale.
“It is a possibility that when baling large swaths of straw, for example, the chamber can become overloaded,” he says. “But the Ultima uses the new Tractor Implement Management monitoring system (TIM), which, by using Isobus, enables the baler to communicate with the tractor and automatically adjust tractor speed in respect of the loading on the baler. Such speed control also ensures the baler makes a sufficient number of rotations to achieve maximum bale density.”
• As the rear door opens to eject the bale, the bottom belt moves down so that, when the rear door shuts and the starter roller moves down to the same level as the end of the rear lower belt, the crop can begin to be transferred into the chamber.
Krone uses the same chamber as the Comprima F155 baler. This has a fixed chamber design and employs a belt and slat elevator – metal slats attached to two endless belts – which initially runs in five guide rollers to keep it in position.
• When the bale reaches 1.2m in diameter, the belts move away from their guide rollers as a tensioning bar moves down against spring-loaded stop rods. The bale can then expand to a size set by the operator, who inserts a pin into one of six hole positions for bale diameters from 1.25m to 1.5m, in 5cm increments.
• With the bale made, net wrap is applied and the bale ejected on to the film-wrapping table. The high chassis of the Ultima allows the bale to drop directly on to the table without any time-delaying transfer system being required.
• To ensure there is no hold up in the film-wrapping department, bales are wrapped using a twin satellite film application system.
Cost and throughput
Suitable for silage, hay or straw baling, the new baler is claimed to have a spot working rate of up to 90 bales an hour and an average output when headland turns are taken into account of about 65 bales an hour, which is very nearly double that of most conventional round baler designs.
Krone says it plans to have 12 Ultima balers working in Europe this year and will have a limited number available for the 2014 season. Expected cost is about €120,000 (£99,150).
Step-by-step process
• Step 1
Normal baling with the cutting rotor and pre-chamber belts transferring the crop to the bale chamber.
• Step 2
Bale completed and net wrapper applies wrap. Belts in pre-chamber stop and the crop which continues to enter chamber is pre-compressed.
• Step 3
The net wrap is cut and the rear door of the chamber is opened. At this time the bottom belt moves down.
• Step 4
Rear door is closed and the starter roller moves down to the lower belt’s level. Both belts then start to transfer the accumulated crop into the bale chamber.