Keep your grain dryer in tip-top condition
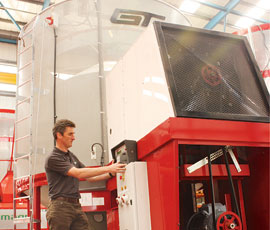
When it comes to harvest weather, we all tend to be optimists. However, with five catchy harvests in a row, only the most bullish farmer is betting on an endless procession of dry, sunny days through August.
The prospect of lots of damp corn coming off the combine is not a pleasant one, whether you rely on a big continuous-flow dryer or a smaller mobile unit to take the moisture out. For increasing numbers of farmers, it’s the latter that will be shouldering the task.
Mobile dryers are sturdy and long-suffering, but they do need some pre-harvest maintenance, says product manager Angus Steven from Opico. The company sells both US-made gas-powered GT mobile dryers and diesel-powered Italian Magna units.
The company reckons it has 3,500-4,000 mobile dryers working around the UK. Around a quarter of those will be dealer-serviced in the winter, while many are serviced by farmers. However, a significant minority have no routine servicing, says Mr Steven.
Here are nine tips for keeping a gas-powered (typically 12t) dryer in top nick.
Burner
1. The GT dryer uses liquified petroleum gas (LPG), which heats up in the dryer and then exits through a series of small holes in a burner ring. These holes can get blocked, so they need cleaning with a gas nozzle cleaner, a pipe cleaner or even a 5/64in drill-bit. Also check the oil trap hasn’t got blocked up.
You need to ensure that the long-terminal spark plug gap is 3/32in and that the terminals aren’t encrusted with lots of carbon. Also check that the silicon-core HT lead isn’t damaged – it can deteriorate after a few years and sometimes gets gnawed by rodents. A new lead needs to come from an Opico dealer – you can’t just replace it with a standard HT lead.
Flame detector
2. The flame detector cuts off the fuel supply if the flame goes out. However, the capillary tube involved can sometimes break off, so it’s worth checking if it looks OK. Similarly, there’s an air pressure switch (pictured) that shuts off the burner if the fan stops working. Make sure the air pipe to this switch is not blocked. The two pilot holes should face forward.
Fan driveline
3. Check for belt wear and correct tension (it should deflect by 1-2in) as well as any play in the bearings.
Agitator
4. The agitator gearbox oil level should be checked once a year and, if necessary, topped up with EP90 gear oil. At the same time, make sure the four guide rollers are seated neatly within the race. They can come loose, causing the agitator arm to move down (potentially tearing the bottom screen) or up (potentially catching the plenum skirt).
Turning an eccentric nut moves the guide rollers in and out.
One easy way to see if things are amiss is to take the chain drive off and try to move the arm up or down. It shouldn’t move.
Bearings
5. The bearing at the bottom of the vertical auger has a hard life. If the dryer is left outside, water will run down into the bottom bin-well, germinating any grain left there and causing the metal to rot. The answer? Keep the dryer undercover, clean out the bin-well and leave the door open once the drying season is over.
Still in the same area, the large washer at the bottom should be loose enough to turn. Also, there should be an 8-10mm (3/8in) gap between the end of the auger and the bottom of the bin-well. If the gap is much smaller than that – or nonexistent – it could be that there’s too much pressure on the bearing.
The answer is to release the grubscrew on the bottom bearing, put a jack under the bottom stub-shaft and then loosen the clamp that holds the vertical auger tube inside the plenum chamber. Jack up the auger until you get the right gap and re-tighten the clamp and grubscrew.
If you have to replace the bearing, then change the two rubber seals at the same time. It might seem a pointless extra job, but it is a false economy not to do so, according to Mr Steven, as it can mean the difference between the bearing lasting six to seven years rather than just one or two years. Grease the bearing every 100 hours, but take care not to overdo it. One to two pumps is plenty.
Discharge head
6. If you need to take the discharge head on and off, make sure you grease the stub shaft well and that the flights make up a continuous, undamaged spiral. There should be just a 6mm (0.25in) gap between the ends of the two auger flights.
Loading hopper
7. Check the grain volume regulator is set right – if there’s grain in the agitator chain drive it’s coming in too fast. It should take about 15 minutes to load 12t.
Auger drive
8. The vertical auger drive belt needs to have the right tension, otherwise it can flip over or jump off the pulleys. The problem can sometimes be due to non-genuine belts, says Mr Steven.
Grain guard sensor
9. Check that the gap on the motion/speed sensors is right, otherwise the electronics will stop the dryer. Beware bridging the contacts as a quick fix.
Competition
Opico is looking for the oldest working Opico machine in the country still in action this harvest. Send a picture of yours in action, along with its serial number, and you could win a free winter service, including ÂŁ500-worth of parts (anything extra will be an additional cost).
Entries to ask@opico.co.uk or Taryn Williams, Opico, Cherry Holt Road, Bourne, Lincolnshire PE10 9LA. Or you can fill in a short online form on the Opico website
Every entry will receive a gift so please include your full name and address.