Green bedding v sand recovery – which is best?
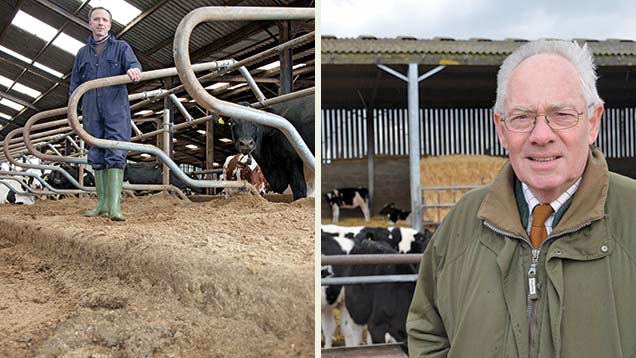
Bedding dairy cows on recycled muck or sand might seem counterintuitive, but plenty of farms are adopting the approach.
Following a certain amount of controversy over recent years, a study funded by DairyCo has concluded that the use of recycled solids from slurry as a bedding material is a legitimate practice and as such has approval from Defra.
Green bedding has been used for decades in North America and northern Europe but it is only in the past 10 years or so that the practice has really got the attention of British dairy farmers.
As such it is still a relatively new concept and users of the system are still tweaking the kit and the way it is used to suit UK conditions.
Separating liquids and solids has the potential to knock massive holes in bedding bills, but it requires a significant shift in mindset.
See also: Manure-into-bedding gains popularity
In the same vein, recycling bedding sand from cubicles sounds fraught with issues, especially when it comes wear and tear on the machinery involved.
However both approaches have their merits and offer the opportunity for huge savings.
Sand recovery: Robert Horton, Wiltshire
With Holsteins yielding more than 40 litres/day, the Horton family place a lot of importance on cow comfort and cleanliness.
Having had concrete cubicles bedded with straw for decades, 15 years ago they made the switch to deep sand beds, primarily for comfort reasons but also to reduce the cases of mastitis and to improve lameness caused by hock issues.
“Every element of cow health is critical in the success of our business,” explains Robert Horton.
“If they’re happy and comfortable they’ll produce more milk, get back in calf easily, stay healthier and last longer. We’ve got cows here that have done 12 lactations.”
Having made the switch to sand, things dramatically improved in all these areas. But there was one thing that wasn’t so easy – dealing with the slurry.
With a large open lagoon, the sandy liquid would settle and it took a lot of work then to get it shifted, taking a heavy toll on the machinery involved.
“We had a huge mass of sandy slurry to get out and spread. It was a nightmare to get it moving and meant it needed stirring and pumping before shovelling out the sand muck into spreaders.
Sand-manure separation
“We struggled on for seven years like that but having spent a lot of time at dairy units in the US I knew there were better ways of dealing with the problem and that we could be recovering the sand for reuse.”
Wanting to find a system that would deal with the slurry and separate out the solids and sand, Mr Horton approached Midland Slurry Systems, which markets the McLanahan Sand-Manure Separator.
Modified and adapted from heavy-duty mining equipment, the Pennsylvanian-produced machine uses a pair of slow-turning augers to propel slurry up an inclined trough through a series of weirs.
With the flight-to-trough clearance set at 25mm, liquid and organic matter tends to flow back down the channel while heavier mineral particles travel up the trough and eventually drop out the top as clean, recycled sand.
Midland Slurry paired the McLanahan machine with one of NC Engineering’s roller and brush separators which takes the sand-free slurry and pulls out the organic, fibrous solids.
The dirty water fraction then makes its way down through a series of buffer ditches where weirs hold back any remaining sand particles before the liquid finally ends up in one of two large lagoons.
Back to the lagoon
“The set-up solved all our slurry issues in one go. We can now get a contractor in to inject the liquid with an umbilical system – and you can see to the inch how effective that is in boosting grass growth.
“The sand-free solids are now easily handled and spread and the sand we get out for bedding is as good as new.”
Due to losses of small mineral particles captured in the weir system, the farm still buys in some sand – about 5% of what it was previously having delivered.
Generally it comes in when temperatures are too low to use the recycled sand, which is difficult to spread with the farm’s trailed AgDispenser when frozen. Despite this, the savings are still pretty impressive.
“The set-up cost us £134,000 and we’ve worked on a six-year payback period. That’s pretty conservative given we’re saving about £20,000 on sand and a similar amount on contractor spreading charges.
“Of course there is electricity and maintenance to take into account.
“After seven years we’ve had to change one of the augers to have it reflighted and there is inevitably the occasional bearing that fails but generally it’s a reliable set-up.
“Most importantly we’ve got an easy-to-mange slurry system and we’ve got comfy, clean cows bedded on recycled sand.”
Green bedding: Anthony Goadby, Warwickshire
With 300 cows in milk plus another 400 followers, the Goadby family spend a good deal of their time ensuring their animals are kept clean and comfortable.
Up until two years ago the business was spending almost £20,000 on bedding materials alone, not including the labour and machinery required to do it.
Serious issues with mastitis in the farm’s traditional straw-yard set-up had prompted a move to cubicles kitted out with mattresses, spread with lime and sawdust.
“Our somatic cell counts [SCC] were up between 300 and 400 with loose housing and we were having 80-90 clinical cases of mastitis per 100 cows each year,” explains Anthony Goadby.
Healthier outcome
“Moving to cubicles was a huge investment but we dropped to 150-200SCC and one-third of the number of cases we had been getting. It came at a cost, though – the sawdust and lime bill was huge.”
When the family decided to increase cow numbers two years ago, cubicles were obviously the way to go and having heard about the potential cost-savings of green bedding Mr Goadby decided to investigate further.
He visited a number of farms using different systems and was convinced that the concept would work at Manor Farm.
“Having looked closely into the options we decided that the EYS screw-press was the one to go for. With its massive, solid-looking gearbox it seemed well-built which gave us a lot of faith.
Keeping costs down
“Buying it through Storth, it was one of the best-priced. But when you started adding all the ancillary stuff the bills started to mount up. So we decided to sort the gantry and bedding bunker out ourselves.”
Instead of mounting the separator on a galvanised steel frame over a concrete panelled storage bay, the Goadbys commissioned a local builder to put up walls with blocks laid on their sides to make up the bunker.
Precast concrete panels were then laid across the top to carry the separator, with a hole cut to allow the solids to drop through.
A fibreglass calf-kennel over the top of the screw-press finished the job off.
“The quote for the gantry frame was £6,000-£7,000 and we would then have had to put a building up over the top of it to keep the bedding dry,” explains Mr Goadby.
“Our enclosed bunker cost about £2,500 and we have no need for an additional building – it was a massive saving.”
How has it performed?
Cows on the first 200 cubicles with mattresses are bedded on 25-50mm of pressed slurry solids while another 80 are in a new shed with plain concrete cubicles. With a half-round fence rail bolted along the heelstone, bedding can be flung on at depths of 50-150mm.
“The cows absolutely love the deep bedding and are clearly more comfortable on that than the mattresses.
Costing about £80 apiece, we saved £6,400 on mats alone and we’ll do the same again with the 60-cow shed we hope to put up this year to trial robot milking.”
Herd health has seen massive improvements with cell counts dropping and the number of clinical cases of mastitis being slashed by three-quarters.
Much of this is put down to the fact that any milk, urine or muck is absorbed better by the thicker bedding so the next cow to come into the cubicle isn’t lying directly on any contamination.
Wet patches are hooked off the beds by hand during milkings.
Health benefits |
||
Mastitis (per 100 cows a year) |
Somatic cell counts (SCC) |
|
Loose-housing in straw yards |
80-100 cases |
300-400 |
Cubicles with sawdust and lime |
25-30 cases |
150-200 |
Cubicles with green bedding |
17-22 cases |
150-175 |
Dealing with the slurry is easier too as the fibrous content is more easily broken down so a crust doesn’t form on the surface of the lagoon and hardly any stirring is required before pumping.
That all helps to keep costs down but the true savings are far greater than that.
“The separator cost us about £50,000 and, running it three days a week it costs £36/week in electricity.
Our sawdust bill was over £380 a week previously and the lime took the total to well over £400. By going to green bedding there is the potential for massive savings.
“But there is one downside – we have to get up five minutes earlier each morning to kick the cows out of bed before milking. In my book comfy cows means happy cows which means more milk.”