Ultimate guide to buying a big square baler 2024
Considering a new big square baler? Then check out our Ultimate Guide to all the makes, models and variations, complete with list prices for these highly productive machines.
Baler specs
Download the complete 2024 buyer’s guide to round and big square balers
Prices apart, changes from last year’s guide are limited – but only because a number of machines received significant updates beforehand.
These included intake improvements for the Claas Quadrant 5200 and 5300 and, for Fendt and Massey Ferguson balers, upgrades to the running gear, pick-up reel, pre-compression chamber adjustment and baler settings display, along with the introduction of isobus speed management; see last year’s Ultimate Guide review for details.
There are, nonetheless, changes reflected in this year’s guide to a handful of mid-range machines that bring added bale density in the never-ending quest for increased productivity and transport efficiency.
In addition, the hitherto flagship models from Fendt (Squadra 1290 UD) and Massey Ferguson (MF 2370 Ultra HD) are listed as unavailable.
Case IH
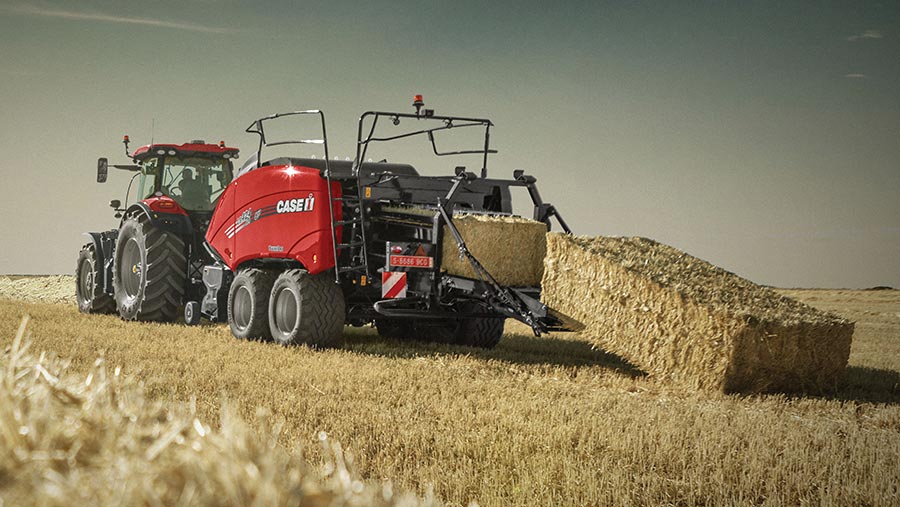
Upgrades bringing a 10% density increase create the new Case IH LB 424 XLD © Case IH
With up to 10% more material packed into every bale, the XLD version of the LB 424 XL offers a performance upgrade over the standard model.
As a result, says Case IH, the newcomer will appeal to customers who need extra-dense, well-shaped, consistent and durable large square bales for maximum output, perfect handling, lower transport costs and optimum use of storage space.
The denser bales come mainly thanks to a reinforced plunger, which provides 400kN of compression force, a 27% increase over the XL.
Its design incorporates strong, perpendicular V-shaped support beams made from 33% thicker 8mm steel, together with four sectional reinforcement plates instead of two.
Reinforced baler chamber side doors are said to be twice as stiff as those on the standard model, while the top door and top door density beams are also stronger and stiffer.
The front and floor sections, meanwhile, are protected by Hardox steel wear plates that are durable and highly resistant to abrasion.
Larger hydraulic cylinders exert greater force on the chamber side and top panels, and there are two more density levers to ensure that increased force is evenly distributed.
Kuhn
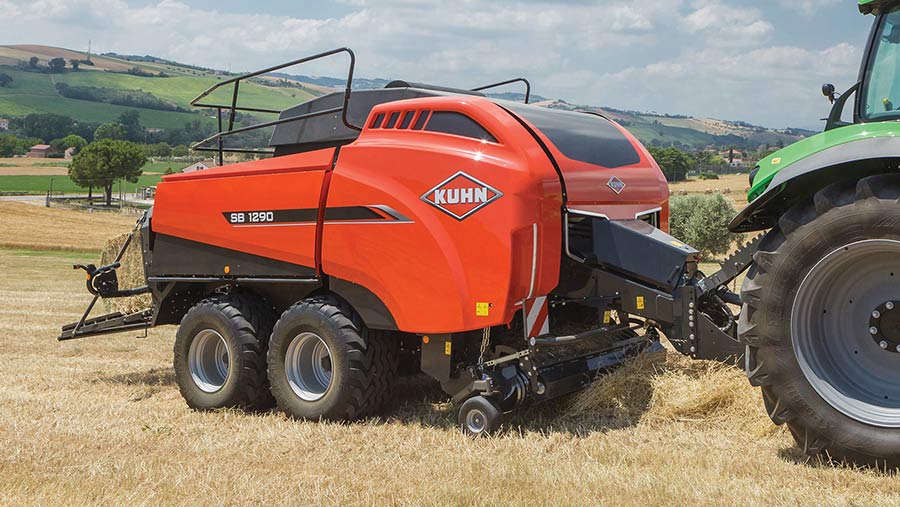
All Kuhn square balers now sport a 75cm longer bale chamber at 3.75m © Kuhn
The 3.75m-long bale chamber first introduced on the “double punch” SB 1290 iD baler from Kuhn now features across the range.
Being 75cm longer, the new chamber exerts pressure on the bale for an extended period as it is constructed, with nine hydraulic cylinders acting upon the chamber side and top panels to help produce consistently high-density bales, especially when packaging very dry material.
It is incorporated on the three 80x90cm, 120x70cm and 120x90cm versions, which all have a conventional one-piece plunger in contrast to the iD’s two-part design that delivers two “hits” with each stroke to produce the highest density of all Kuhn balers.
New Holland
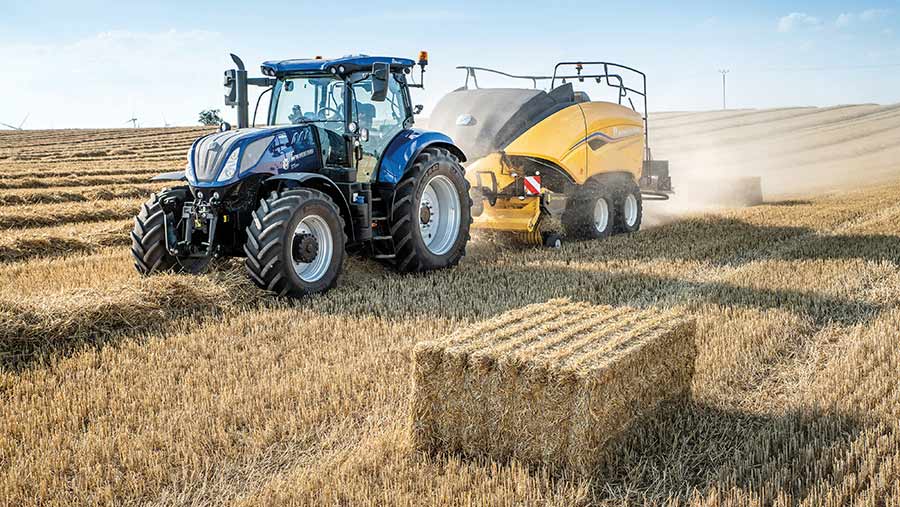
Stiffer side and top chamber panels, plus bigger rams, feature on New Holland’s BigBaler 1270 Plus Density © New Holland
With double the force applied to the chamber side panels and 25% more on the top panel, the new “Plus Density” version of the New Holland BigBaler 1270 is reckoned to have up to 10% greater bale density potential.
The newcomer slots into the line-up alongside the existing BigBaler 1270 Plus, both producing a 120x70cm bale, with models on either side making bigger (120x90cm) and smaller (80x90cm and 80x70cm) packages.
Like its siblings, the new baler is available with a tine-feed intake mechanism or with a 650mm diameter helix rotor and 15- or 29-knife crop slicing system.
In addition to a reinforced plunger, stiffer top and side chamber panels, and otherwise optional Hardox floor wear plates as standard, the secret to the 1270 Plus Density’s ability to stuff more material into each bale is the big increases in hydraulic ram force.
This is up by 113% on the side doors compared with the regular model, with an additional two density levers helping spread the force evenly, and by 25% on the top panel.
Despite the increased pressure in each bale, the same LoopMaster knotters as on the other models continue to be used.
The notable characteristic of this design is that the second knot is made in a loop style, which New Holland says results in 26% greater tensile strength compared with conventionally-tied twine.
Moreover, the lack of trimming potentially saves dropping 6km of twine in fragments across fields during a 10,000-bale harvest campaign.