Farmer builds ingenious twin-chamber double square baler
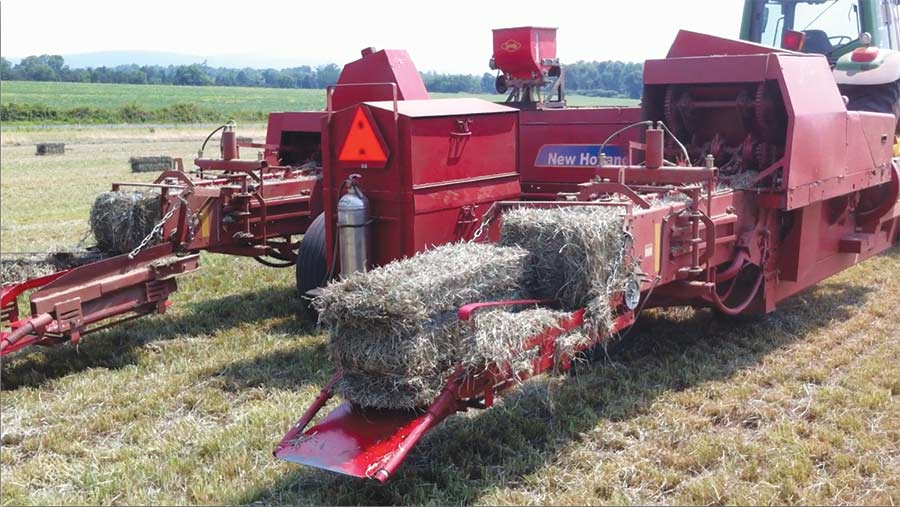
Keen to increase the pedestrian pace of small-bale hay production, Virginia farmer Rusty Inskeep designed and built a baling system that almost tripled the farm’s output.
The slick setup allows the team at Mount Pony Farms to make, collect and stack about 5,500 bales safely in the dry each day, without having to do a jot of manual handling.
But this output isn’t the work of a team of balers.
Central to the operation is a one-off, custom-built, double-barrelled baler that, once wound-up, will fire out up to 20 60lb (27kg) bales a minute.
The inspired machine – dubbed the Mount Pony Special – was built by Mr Inskeep in the farm workshop, and consists of two New Holland BC5070 conventional balers conjoined at the pick-up.
Travelling at speeds of up to 13kph, its twin chambers fire out a double row of bales, and with fewer headland turns to perform, it will do the work of three single machines.
Farm facts
Mount Pony Farms, Culpeper County, Virginia, US
- Size: 810ha
- Cropping: corn (maize), wheat, beans, and grass for horse hay
- Staff: Rusty and John Inskeep (pictured), plus Neal Coffey, Ricky Dugan and Billy Walker
Once ejected, the bales are flipped 90deg on to a weighing platform before dropping to the ground.
The next part of the process involves a team of three New Holland Stack Cruisers.
These self-propelled machines trundle along the rows, picking up bales with a conveyor and stacking them on board.
Once they’re up to their 162-bale capacity, these head back to the yard and offload directly into a shed.
Rusty Inskeep, his bother John and three other members of staff – Neal Coffey, Ricky Dugan and Billy Walker – share the workload between them and hop between the different machines.
The final part of the system is a conveyor-belt trailer that helps speed up deliveries to customers without a loader.
The conveyor runs the length of the trailer and allows one person to empty the entire 607-bale load in 90min.
See also: Inventions Competition 2019: Strap winders, gate lifters and other clever farm gadgets
Quality hay
The speedy baling process is essential for maintaining the quality of the farm’s hay, which is predominantly sold to equine customers.
The harvest regime at Mount Pony Farms, which is located in Culpeper County in the north of Virginia, begins with a Krone Big M2 self-propelled mower.
To help speed the wilting process, this is fitted with a set of B&D crusher rollers, which, according to operator Neal Coffey, cuts about a day off the drying time.
Summer temperatures in the region peak at about 30C and on average it takes about two days for the hay to make. However, on some occasions it is possible to cut one day and bale the next, with only one run through with the tedder.
Raking is carried out with a Vermeer V-rake that produces a 6ft-wide windrow for the double baler.
For some of the crop, Mr Inskeep will also run through with his homemade hay processor.
This is essentially an old round baler with the chamber removed and a knife unit bolted in its place.
It trundles up the rows ahead of the baler, chopping the hay before laying it back down in the swath.
Apparently, horses will eat every scrap of the crop when it’s processed in this way and as a result there’s a list of customers waiting to take it each year.
With this grade of hay, water content is crucial, so Mr Inskeep has installed moisture meters on both of the baler’s chambers with readouts in the tractor cab.
He also applies Siloking granules via a Gandy box applicator fitted above the pick-up.
To ensure bales are uniform, a set of scales has been installed at the rear of each chamber.
These register and record the weight of each bale as it leaves the machine and allow the operator to make quick adjustments to ensure the bales are being produced to spec.
Including straw, the baler clocks up an annual bale count of 70,000 and generally gives very little trouble.
However, Mr Inskeep has a spare BC5070 baler on standby for the odd occasion it’s out of action.
Building the beast
The process of bolting two balers together is far more complicated than it sounds, and despite Mr Inskeep’s engineering experience, the double-baler project took about a year to complete.
The first of his jobs was to work out a suitable way of getting the two identical New Holland BC5070 balers to work with one another.
In the end, he opted to mount them side-by-side, with the pick-up positioned in the centre so that the operator could drive directly over the windrow.
However, with both machines being built in the same orientation (with the pick-up sticking out on the right-hand side), this approach meant one would have to be completely rebuilt to work in reverse.
Sensibly, it was the left-hand unit that was left intact so that its pick-up could be used to feed both balers.
Apart from extending it from 6ft to 7ft, no significant modifications needed to be made.
Then, once the right-hand baler had been stripped back to the bare bones, Mr Inskeep could begin rebuilding it in reverse.
This process also involved flipping some of the internals upside down so that the raker arm would move in the opposite direction.
It needed to do this so that it would grab material from the now shared pick-up on the left, rather than its original unit on the right.
In a bid to help balance the machine, he also timed the rams so that one is pulling back as the other goes forwards.
Framework
Properly supporting and pulling the new rig was another challenge, so Mr Inskeep enlisted the help of his nephew Paul, a design engineer, to come up with a custom frame and drawbar.
He was able to thrash out multiple iterations of the design and carry out virtual stress testing before any expensive and time-consuming work was carried out in the workshop.
Kit list
- Tractors: John Deere 7520, 7430, 2950 and 2155
- Forage equipment: Krone Big M2 self-propelled mower with B&D crusher rollers, Vermeer V-rake, custom hay processor, custom double baler, New Holland BC5070 conventional baler, New Holland Stack Cruiser x 3, John Deere 466 round baler, custom conveyor-belt hay delivery trailer
- Drills: Custom 30ft John Deere 1590 no-till disc drill, eight-row maize drill, John Deere split-row planter for beans
- Combine harvester: John Deere 9770 with 30ft header and eight-row maize header
- Sprayer: GVM Prowler
- Muck spreaders: Three twin-disc spreaders fitted to Mack and International rigid-frame trucks
- Other: Mack articulated trucks x 2, GT grain dryer running on three-phase electric motors x 2, John Deere Land Plane, set of discs, trailed granular fertiliser spreader.
The resulting structure is built out of heavy box-section steel and starts with the drawbar, which sweeps up high to clear the windrow.
This has a split framework to allow the pto to pass through the centre and is connected to a square frame that runs under the whole machine, locking both balers together securely.
The balers’ original running gear was also removed, with the outfit now running on a set of super-single wheels attached to the new frame.
Providing the power
Getting power to each baler also required a bit of thought. In the end, Mr Inskeep opted to run the tractor on the 1,000rpm pto.
He used a straight shaft from the tractor up to the centre of the machine, where a gearbox splits the drive to either side.
There is then a 90deg gearbox at the front of each baler unit that gears the drive speed down to 540rpm and directs the power straight to the flywheel.
Final touches included fitting a large, 16-spool twine store at the rear in the void between the two balers.
All up, the baler weighs just under 5t and a 160hp John Deere 7430 pulls it.
This is fitted with dual wheels to help improve stability.
The completed rig measures about 13ft (almost 4m) wide, which isn’t a problem in the US.
However, this would prevent it from travelling legally on the UK’s road network without an escort.
So far, the Mount Pony Special has totted up a total bale count of 500,000 and hasn’t had to have any modifications to the original design.
Other projects
Hay processor
Mr Inskeep’s hay processor started life as a fire-damaged John Deere 457 round baler.
He stripped it down, keeping just the pick-up and running gear, and built his own knife unit that sat on the top.
In operation, hay is swept up from the windrow, chopped and returned without having to row-up again.
Conveyor-belt hay trailer
To reduce the amount of manual handling when delivering small-bale hay to customers without a loader, Mr Inskeep built a trailer with a conveyor belt running through the floor.
When it’s full, panels cover the belt, but as the bales start to get unloaded, the panels can be removed, allowing the operator to place the bales on to it.
They are then be transported to the rear and dropped off the back.
The trailer can accommodate 607 bales and one person can unload it in 90min.
30ft John Deere drill
To increase drilling output, Mr Inskeep continued his theme of doubling up by mashing two 15ft John Deere 1590 disc drills together.
He did this by splitting one of the drills in half and mounting the separated sections on hydraulic-folding wings on either side of the other drill.