Contractor adapts McHale Fusion for single-pass silage bales
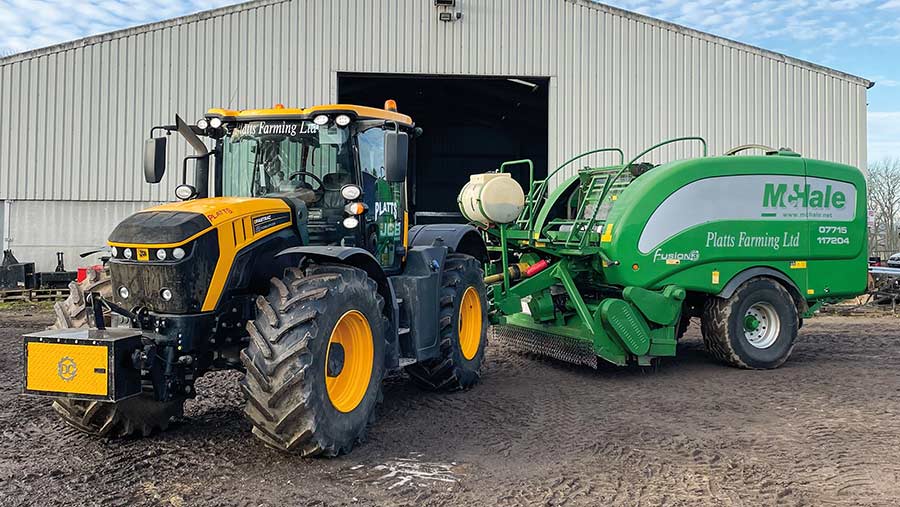
Mulling over his council mowing contract in the local pub, Nottinghamshire contractor Mitch Platts devised a novel way of turning the clippings into saleable livestock feed.
His ingenious plan involved taking a second-hand McHale Fusion baler wrapper, removing the pick-up and grafting a flail mower in its place; the theory being that he could cut, bale and wrap round bales on rough ground in a single pass.
As well as creating silage that could be sold or given to his own livestock, it offered a considerable time and labour saving over his original system.
This involved cutting the sites using flail mowers fitted with collecting boxes, before returning with trailers and grab loaders to remove the crop and dump it on a muck heap.
“Most of the sites we cut are wildflower meadows or sites of special scientific interest, so the clippings have to be removed to prevent the fertility building up,” says Mr Platts.
“The old system worked, but it was labour intensive and it seemed mad that we were dumping decent grass and letting it rot down.”
See also: Driver’s view: Paul Brute’s McHale Fusion 3 Plus baler-wrapper
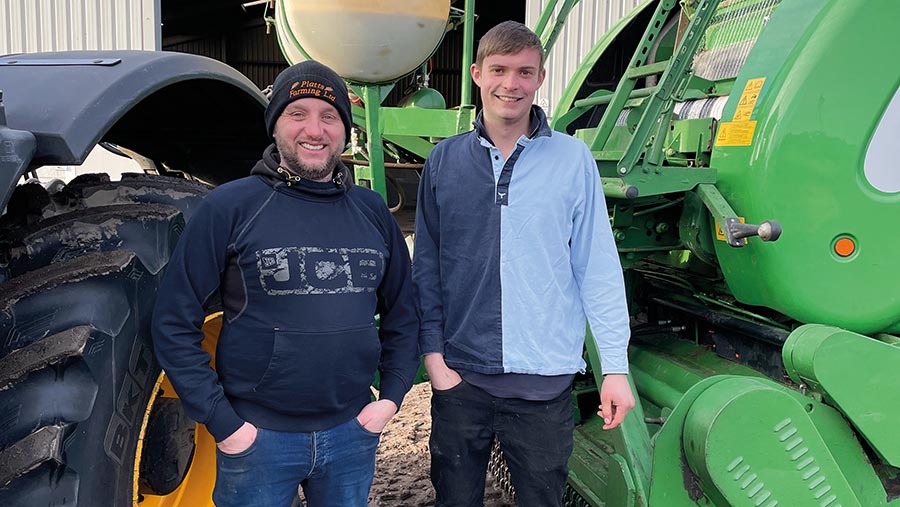
Mitch Platts and Ed Curtis © James Andrews
Building it
The build took place in 2018 with the help of a couple of lads who were working for him at the time, and his late father, Roy, who was a skilled engineer.
His expertise was put to particularly good use when it came to making pulleys up on the lathe and calculating how fast they should be spinning.
Work began by sourcing a second-hand McHale Fusion 3 baler wrapper at a sensible price. After a rifling through the classifieds, Mr Platts found one for sale with Welsh dealer Emyr Evans.
It was on a high bale count, but was in good condition, apart from a heavily worn pick-up. As this wasn’t required for the project, the machine seemed a good fit and was purchased for about £25,000.
The mower selected for the front of the rig was a 2.7m Spaldings Concept flail that was already on the farm. It was about the right width and had a tough enough construction to withstand encountering the odd foreign object.
“Most of the sites we go to are clean, but you get the odd one where people have dumped stuff,” says Mr Platts. “We’ve come across lumps of concrete, bicycles and the occasional barbeque, so you need a robust machine.”
Before attaching the mower, they needed to decide how close it should sit to the baler.
After watching how far the mower threw grass during work, they reckoned it needed to be about a foot away from the rotor – a distance that proved to be just right.
It was then welded in place using braces running up to the drawbar and chassis.
With the mower and baler set in a fixed position, they needed a way of adjusting cutting height. This was achieved by splitting the drawbar and fitting a pair of hydraulic rams from an old Bettinson drill.
Other modifications included widening the baler’s intake to match the width of the flail and extending the side feeding augers to get the crop to flow cleanly.
The most difficult job was sorting out the driveline, a process that was made more complex by the fact that the baler ran off the 540rpm pto and the flail input needed to spin at 1,000rpm.
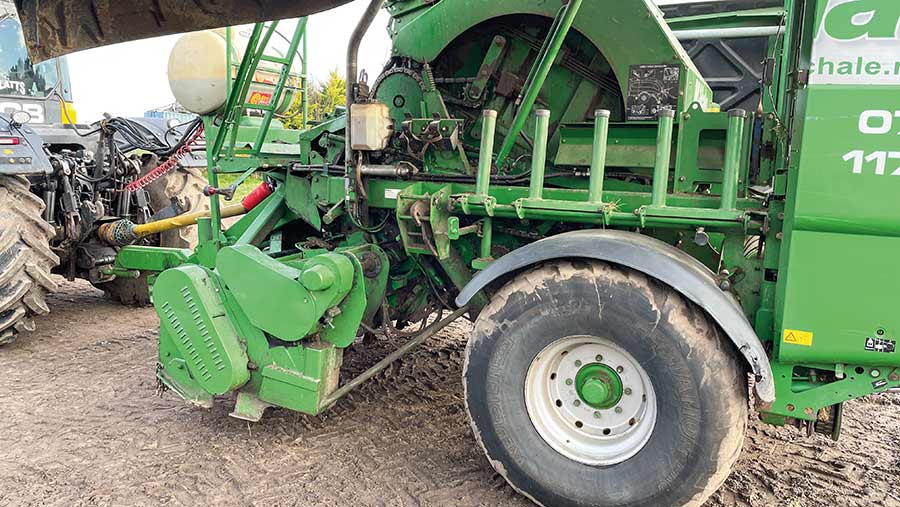
Altering the driveline allows the baler and flail to run at different speeds © James Andrews
This is where Mitch’s dad came in. He split the baler’s driveline and added a belt-and-pulley arrangement to drop power down to the left side of the flail via a 90deg gearbox.
A few sums and a bit of trial and error were required to get the ratios right, but he successfully managed to up the speed enough for the mower to cut cleanly.
An added complication was getting drive to the right-hand feed auger, which was originally powered from the pick-up.
The solution was to alter the sprocket arrangement for the left auger and add an additional driveshaft that runs across the front of the rotor.
Most of the parts for the driveline were sourced from Acorn Industrial Services near Rotherham.
The final part of the build was adding a molasses tank to make some of the poorer grass more palatable. An Eco Bale pressurised tank was bought off eBay and mounted on a frame that sits above the baler’s drawbar.
This is supplied with air from the tractor and sends a fine mist of molasses into the rotor via four jets. The application rate is altered by adjusting the air pressure.
They considered adding an electric valve to control the flow, but for simplicity and reliability, they switch it on and off using the tap on the tank.
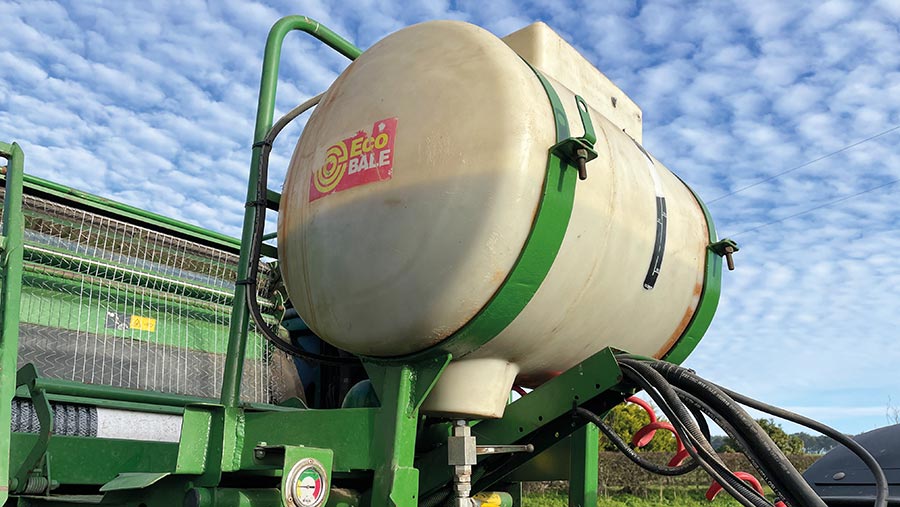
A pressurised tank feeds four jets that fire molasses into the rotor © James Andrews
Using it
The baler was up and running for the 2018 season and, bar a few minor teething problems, it worked well.
Grass flowed from the mower to the baler cleanly and the baler didn’t miss a beat. However, the fact that there is no way of seeing the grass going into the bale chamber means the driver must stay alert.
“It’s a bit of a seat-of-the-pants job and you have to judge your speed based on the sound it’s making,” says current operator Ed Curtis.
“I often drive with the radio off and the back window on the latch so I can hear exactly what’s going on.”
Working speeds range from 5kph to 16kph and cutting height is adjusted according to the conditions.
As the flail is only 2.7m wide, it can’t cut enough grass to block the baler intake, but if it travels too fast, some will spill out. “If that happens, I just go back over that patch and drop the speed,” says Mr Curtis.
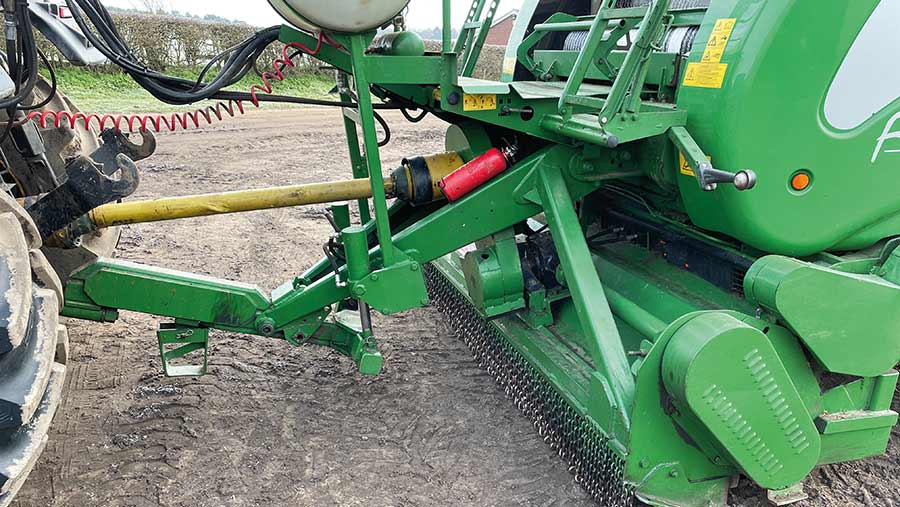
The split drawbar allows mower cutting height to be adjusted © James Andrews
When the ground is rough and there’s some contamination, they leave a slightly longer stubble. And if they do encounter any heavy debris, the flail tends to drop this under the baler, so only clean grass goes into the chamber.
The original chopper unit is still in the baler, but it doesn’t tend to get used. This is because the Y-shaped flails on the mower chop the silage into roughly 5cm lengths and the average bale weight is about 1t.
When they have used the knives, they tend to put too much in the bale.
Due to the distances they travel between sites and the roughness of the ground, a JCB Fastrac 4220 is the tractor of choice.
“Sometimes, we’ll go miles to cut a rough patch of ground that’s no bigger than a domestic garden, so we need a tractor that can get there quickly and soak up the lumps and bumps.”
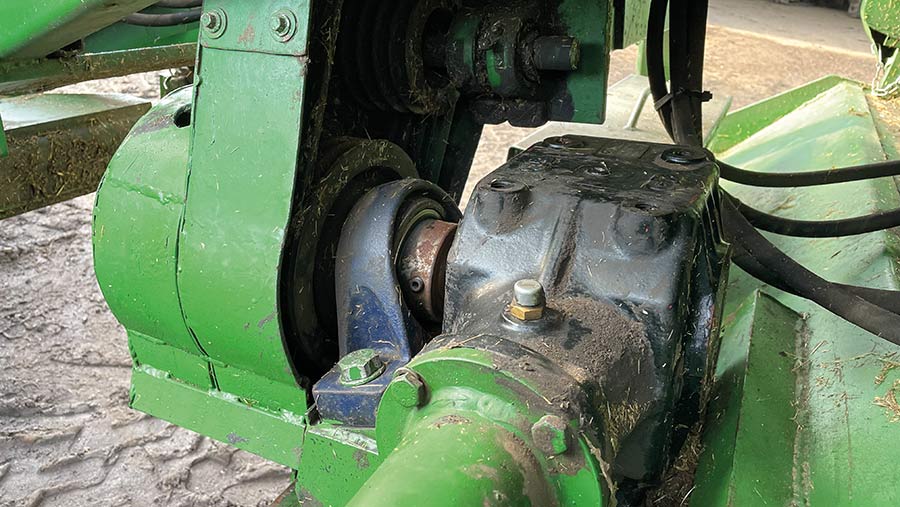
Mower driveline © James Andrews
Bale collection
To speed up the process of collecting the bales, Mr Platts invested in a Wilson Engineering bale trailer that can carry 12 bales at a time.
This needs to be used immediately after the bales have been made, as they slump slightly over time and won’t slide into the trailer properly. If they can’t collect immediately, they use a loader tractor and conventional trailer.
Mr Platts didn’t have high hopes for the quality of forage, but it’s been surprisingly good, and they’ve rarely felt the need to add molasses. It’s been fed to sheep, cattle and horses, all of which have eaten it and done well on it.
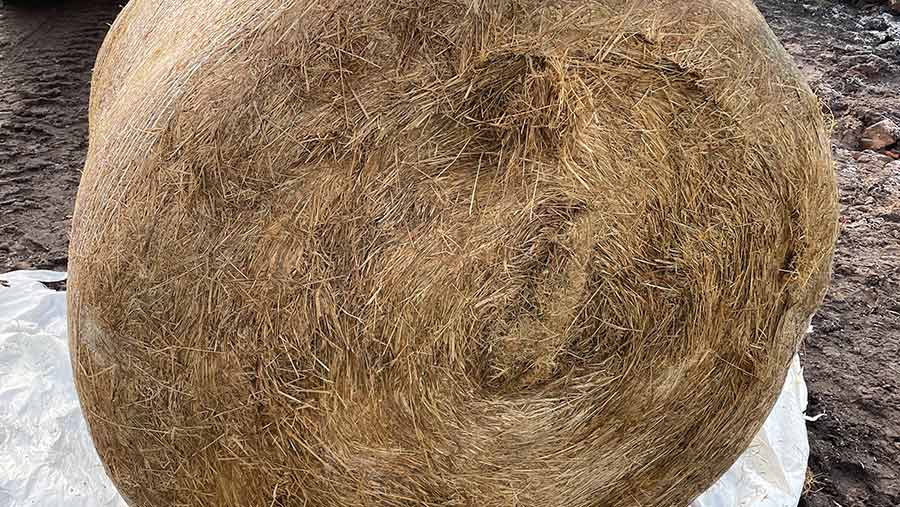
Silage bale © James Andrews
One year, they carried out a trial on one of their better patches of ground – one half was cut with a disc mower conditioner, left to wilt, rowed up and baled, and the other half was direct cut with the one-pass McHale.
They were sent to a customer for comparison and the one-pass bales were the most palatable.
The decent quality means Mr Platts hasn’t struggled to sell the bales. Prices vary according to the season, but last year he sold some for £25/bale.
He’s also considering upping his own stock numbers based on the quality of the feed.
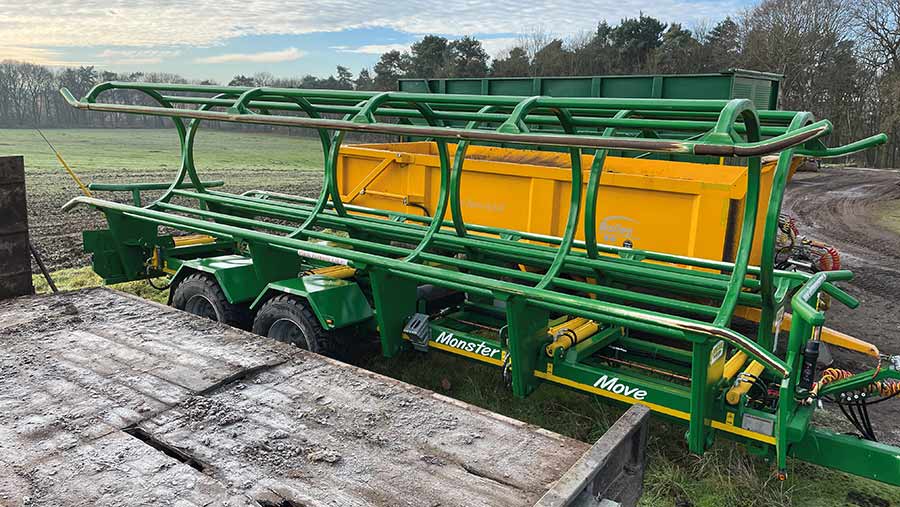
Wilson bale trailer © James Andrews