Grain dryer revamp helps cut farm energy costs
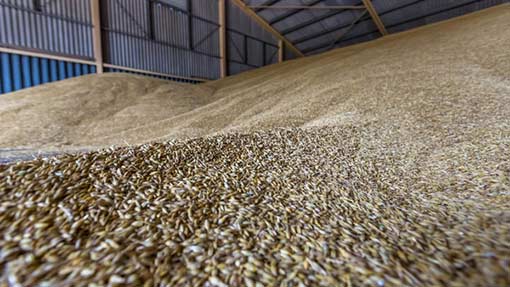
High-capacity grain handling, good ventilation and efficient energy use were priorities for a Cambridgeshire farm’s new grain drying installation.
A convenient gap between two grain stores has been filled by a new intake and drying facility that eased harvest operations on a Cambridgeshire farm last year.
In particular, it removed a big bottleneck imposed by the existing 40-year-old set-up and resulted in more timely combining of crops on the 710ha (1,750 acres) at Manor Farm at Keyston near Huntingdon.
“With 5,000t of floor and bin storage we had plenty of capacity for all crops,” says Minto Lohoar of Keyston Farm Partnership. “But putting them through a 20t/hr drier when we’re combining at 45 to 50t/hr was hopeless.”
The struggle to keep up resulted in piles of wet grain, delayed combining and a lot of double handling of grain between storage sheds and the dryer.
“It took months to get cleared in a wet year and shifting 500t of grain and oilseed rape backwards and forwards in a 10t trailer is no joke,” says Mr Lohoar. “The contrast with the way things went last year is tremendous – the new facility could easily keep up with the combine and we needed one less casual to cope, so there was a labour cost saving too.”
The square building fits neatly between two grain stores. It houses an intake bunker (left) with plenty of height for tipping trailers; a lobby housing the drier and handling system controls, and space for sample analysis and storage. There’s also an enclosed bunker beneath the aspiration system cyclone to minimise dust.
New installation
The new installation designed by dryer manufacturer and service company GrainTek, in collaboration with Ludlow’s APS Erection, consists of a square steel-framed building clad with Plastisol-coated steel sheet produced by Thomas Panels & Profiles at its Leominster factory in Herefordshire.
“Our TPP 1000-32 profile is produced from a continuous roll and cut to the required length,” explains George Thomas. “This project also called for our Ventair perforated product, which is unusual for an arable building.”
The cladding, finished in Goosewing Grey to tone in with adjoining buildings, is cut short to one side of the building to avoid creating a cosy void for rodents where it would cover the grain walling that forms one side of the intake bunker.
The Ventair perforated sheeting gives an air flow equivalent to Yorkshire boarding, says Phil Crow of GrainTek. “A lot of consideration is given to good ventilation in livestock buildings but it’s often overlooked for indoor driers,” he points out. “The perforated sheeting ensures the drier fans can run at peak efficiency.”
At harvest, milling and feed wheat, spring barley, oilseed rape and spring beans are tipped into an 8m x 12m intake bunker capable of stockpiling up to 230t of grain.
The new grain intake and drying facility transformed harvest operations for Minto Lohoar of the Keyston Farm Partnership.
Tramlines let trailers back further
There’s no pit, instead two below-ground Kongskilde KCA30 chain conveyors draw the crop from the front of the bunker to minimise the amount of pushing up needed while clearing two “tramlines” so that trailers can continue to be backed in without running into the pile.
The conveyors have a nominal capacity of 30t/hr each and feed a 60t/hr KCA60 cross conveyor with a 45deg incline section discharging into one of three Kongskilde KBE60 bucket elevators.
“Inverter control of the motors provides adjustable speed and performance,” explains Malcolm Greves of Kongskilde. “Grain can be drawn at up to 60t/hr to fill the dryer quickly when empty, then at a slower rate to match dryer throughput.”
Filling rate is automatically slowed when grain reaches the low-level sensor 1.5m from the top of the dryer, and again when detected by the mid-level sensor.
Everything is brought to a halt when the dryer is full, with a return-to-pit gravity chute from the dryer-filling conveyor providing a fail-safe mechanism. Thereafter, grain is drawn from the intake as and when needed.
“We were offered two handling systems and went for the more expensive option,” says Mr Lohoar. “The Kongskilde system was the better quality product, in my view, and with an investment such as this I wanted something that would last.”
Despite being housed indoors, the GrainTek Tornado 5.5/20 mixed flow drier is fully clad and insulated for maximum fuel efficiency.
Thomas Ventair perforated sheeting is used on three sides of the building to ensure sufficient air flow for the drier fans to work at peak efficiency. They are designed to give air flow equivalent to Yorkshire boarding.
Minimising heat loss
“It only costs a few hundred pounds more but the potential energy savings are tremendous – about 18kW/hr by insulating the roof alone,” says Phil Crow.
“It makes sense to minimise the heat loss and reduce the amount of energy consumed to dry grain – it’s potentially worth about £2,000 a year for this installation.”
Energy efficiency apart, Mr Lohoar reports that the heat insulation and ventilation provided by the perforated cladding also helps create a pleasant working environment in the drying plant.
“The dryer panels are only warmish to the touch and the shed stays cool even on the hottest days,” he says.
The operator also enjoys the comfort of an entrance lobby where the touch-screen control system is housed for the dryer and handling system, and crop samples are analysed and logged.
“I’m very pleased how the project turned out,” says Mr Lohoar.
“We can now start combining at 10 or 11am because we have the drying capacity and there’s no more stockpiling and tedious double-handling of wet grain.”