Video: Getting the best from a Horsch Pronto
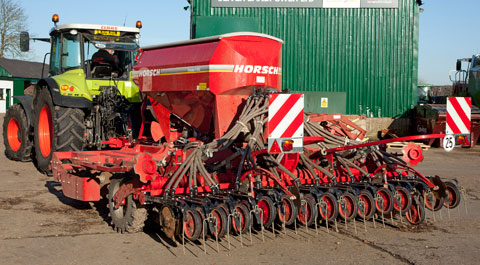
Our series which sets out to advise users on how to get the best from their machinery continues with a look at the Horsch Pronto drill – a Pronto 4 DC which uses discs as it primary cultivation unit. Watch the videos and read the report.
The drill, loaned to us by a local farmer, has clocked up about 3,500 acres over a couple of seasons and, as we shall, see is showing some signs of wear.
So with the help of Horsch service engineer, Will Lawton and use of the workshop facilities provided by Luton-based Horsch dealer, AT Olivers, let’s discover the points to look for – and the errors to avoid.
- The drawbar on the Pronto drill can be extended if required. Check to ensure the retaining bolts have not become loose.
- As with all hydraulic systems check pipes for wear/chafing and hunt down any oil leaks.
- Rubber blocks clamped between the beam and the disc support arms provide a degree of suspension and absorb shock loadings. Check that clamp bolts are tight and that the rubber blocks are present and in good condition.
- Sideboards to prevent soil throw need to be operational if even drilling is to be achieved. Check for wear and replace if it is excessive.
- Press wheels need to be at the correct pressure to do their job and to prevent excessive tyre wear. A hard tyre wall and a soft tread helps to keep the wheels clean.
- Preparing to adjust the coulter bar pressure. Note the use of coloured shims on the coulter raise and lower ram to provide the required working depth and pressure.
- To prevent coulter bars shaking about when raised this gap needs to be closed by lowering the bar so that it is in contact with the coulter support arms.
- Coulters each have two discs. Check the sealed bearing condition by removing the six retaining bolts (left hand thread).
- Cultivation discs run on oil filled sealed bearings. Check for any leaks and replace bearings as required.
- These discs are about a third worn and, depending on soil type, should be good for 7-10,000 acres before being changed.
- On assembly, the two angled discs should just meet at the bottom.
- Seed distribution takes place in the seeder head – as does the tramline seed cut off.
- Remove the central plate to check that the electronically activated tramline units are operative and are not blocked with seed residues.
- When the plate is fitted with the deflectors in the distributer it blanks off half of the coulters for right or left hand only drilling.
- Each seed outlet should also be clean.
- Loosening the clasp holding the seed pipe to the coulters requires a pair of grips – not a screw driver which will cause them to split.
- The seed metering unit – note the brushes which can be places in the unit when the small seed roller is fitted.
- Also look out for leaking hydraulic pipes on the wing lift rams.
- Check that working pressures are correct. The left gauge is for the fan air pressure and the right is for the hydraulic ram pressure on the wing sections.
- Seed metering rollers to cater for different crop types – ensure there is a full set on board.
- Forward speed is essential information for the seed metering unit. It is recorded using a radar system.
- Check that its sensors are clean and working correctly.
- It’s a bit of a plumber’s nightmare but take time to check each pipe and electrical connection.