Farmer gets 12m drill and Case IH Quadtrac for just £85,000
Keen to get into low-disturbance drilling without spending a fortune, Warwickshire farmer William Forsyth decided to build his own machine and buy a cheap used tractor to pull it.
But with more than 2,000ha of drilling to cover each year from his base near Kineton, he had to think big. In the end he went the whole hog and converted a massive 12m Horsch CO12, but not before doing a bit of homework first.
Mr Forsyth’s desire to give low-disturbance drilling a go started back in 2010. At the time he was concerned about the uncertainty of future cereal prices and wanted to find a cheaper system than the farm’s current min-till regime.
See also: Customised Horsch CO4 offers min-till drilling on a budget
To find out more, he went on a fact-finding mission to the USA and took a look at their systems for no-till crop establishment.
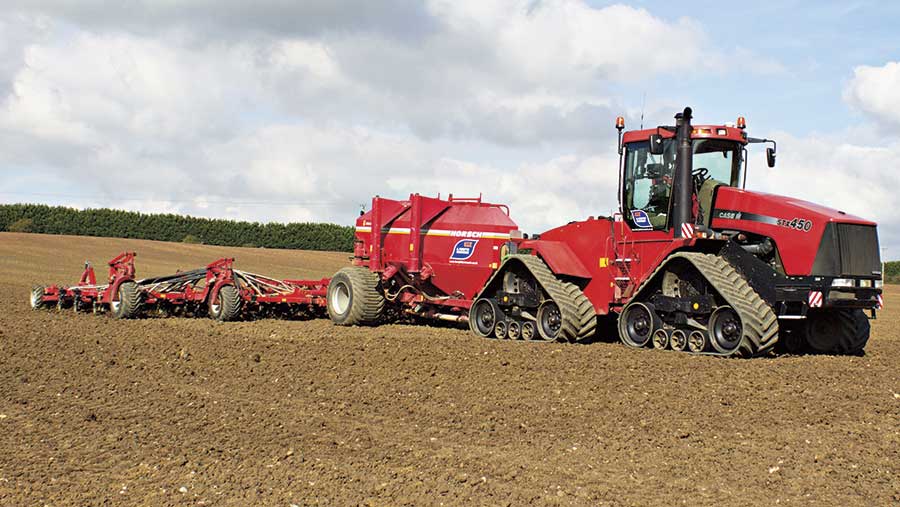
© James Andrews
Inspired by the fact that they were managing to direct sow into heavy clay ground like his with simple disc drills, he came home, bought an old, well-used John Deere 750A and decided to give it a go.
Sadly the drill just didn’t have the coulter pressure to penetrate into his heavy ground, so it was parked up and drilling duties were resumed by the farm’s brace of trusty 8m Vaderstad Rapids.
Discs to tines
Undeterred, he switched his attentions from disc to tine drills. As an experiment, he got hold of a couple of demonstrator tine drills, which he put to work in spring 2013. Both drills did a decent job, but when it came to autumn they both kept clogging up with the volume of straw from the preceding crop.
That’s when Mr Forsyth decided to have a stab at making his own machine with greater trash clearance. The first job was to track down a donor drill, and with its reputation for coping well in trashy conditions, the Horsch CO was top of the hit list.
To fund the project, Mr Forsyth sold a few items of redundant kit and then hunted down a tidy 6m Horsch CO6. The plan was to experiment with a 6m machine with the hope that the design could be stepped up to 12m in the future.
With the drill acquired, he and Tom Winters, who was working for him at the time, set about stripping it down for the conversion.
The first job was to remove the Horsch’s original set of Duett coulters and find a suitable set of low-disturbance legs to replace them. After some shopping around Mr Forsyth settled on Weaving’s Sabre tines as the most fitting replacement and worked out that he would need 42 in order to give him the 15cm spacing he wanted.
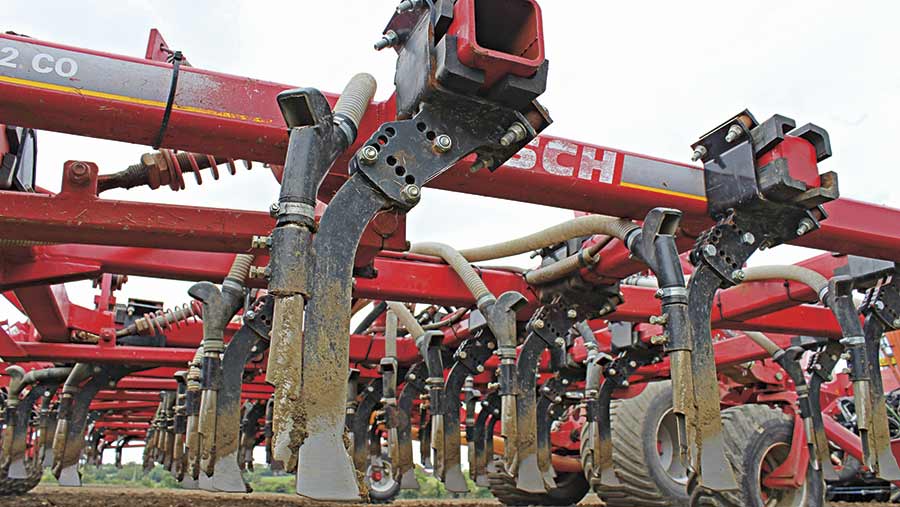
Weaving Sabre tine coulters © James Andrews
The next challenge was to fit Weaving’s diagonally mounted tine brackets on to the Horsch’s square frame. One option was to fabricate another sub frame, but he decided this would require too much work and add too much weight, particularly as they were going to step the design up to 12m.
Instead, Mr Forsyth came up with the idea of getting new 90 deg rubber suspension mounts made to replace the original round corner mounts used by Weaving.
He tracked down a specialist manufacturer in Southampton that fabricated a hardened rubber mount capable of withstanding the pressures exerted on it by the coulter, but also offering some shock deadening.
These meant the Weaving tines could be bolted on to the Horsch’s square frame without any modifications, other than adding a couple of extra bits of framework to accommodate the larger number of tines.
After playing around with the orientation of the tines across the four rows, he settled on staggering them diagonally to improve trash flow.
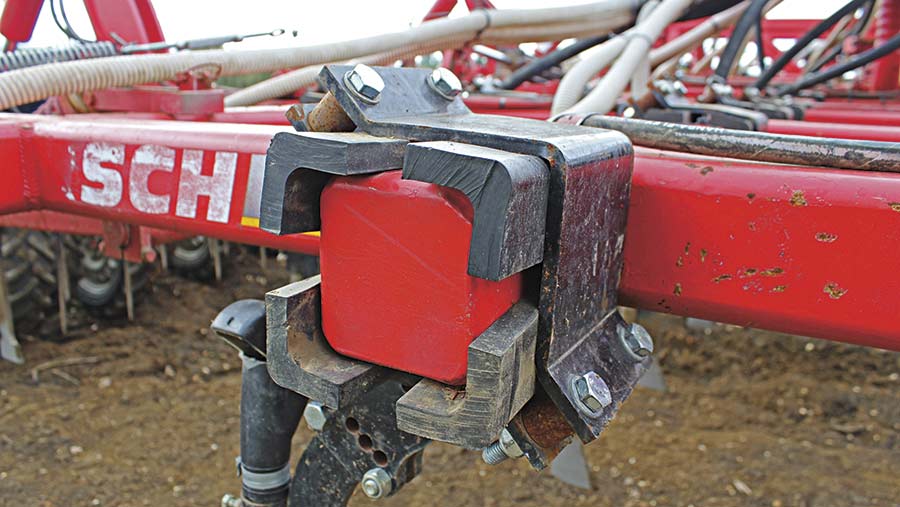
Custom rubber mounts © James Andrews
With the tines successfully arranged, Mr Forsyth asked Weaving to build him a custom distribution head that could feed the additional coulters. Final touches included fitting a tramlining kit and radar metering system.
The drill was completed by spring 2014 and planted 30% of that year’s cropping area, with the Vaderstad still hanging on to the lion’s share of the work.
Throughout that period the 6m Horsch/ Weaving mashup was being pulled by a 200hp New Holland T7050, which was never wanting for power. The 8m Vaderstad, meanwhile, was still being hauled along by the farm’s old-school 360hp Versatile 946.
As 2014’s crops started to emerge the difference in quality of crop establishment between the two drills was minimal. Added to that, the low-disturbance drill was considerably easier to pull and encouraged less blackgrass to germinate.
Buoyed by the results, Mr Forsyth decided to forge ahead with the 12m drill.
Going to 12m
The first job on the full-size drill project agenda was tracking down a decent 12m Horsch CO12 for a reasonable price.
Initial searches bought up several newer machines, but their circa £150,000 price tags meant they were out of the question.
Eventually, Mr Forsyth stumbled across an earlier 2005 drill for sale in Denmark, which had a far more reasonable £25,000 asking price.
It had spent its life on the huge Bregentved Estate and had all the features he was looking for, including the biggest 7,500-litre seed cart available with twin loading augers.
It cost £2,500 to haul the drill back to Warwickshire and it arrived in spring 2014 ready for the conversion work to start. Not wanting to spend any extra money on the project, he funded it by selling two ploughs and a Vaderstad Topdown.
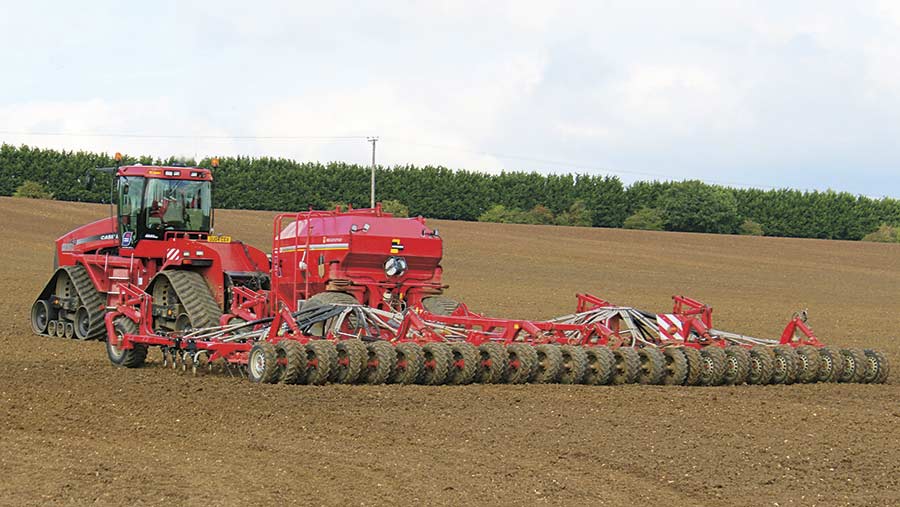
© James Andrews
Adding the 82 coulters using the same system as the 6m drill was fairly straightforward and while they were at it they added an extra coulter on each side so that the drill would sow to a full 12m and fit in with their partial CTF system.
But the tricky part came when they tried to get the new, larger twin distribution heads to fold within the frame.
“We spent hours and hours trying to work it out,” says Mr Forsyth. “But eventually we came up with a linkage that tucked them out of the way as the wings folded up.”
He also had problems with the CO’s original seed pipes kinking as the drill folded. However, he noticed that there were a few replacement pipes fitted by the Danes that never had a problem. Through Weaving he managed to sort a full set of these ‘memory rubber’ pipes and the problem was solved.
Putting it to work
Due to the complexity of the project it was eight months before the drill was ready to start work in spring 2015 and the total build cost ran to about £40,000. That included the £25,000 paid for the drill, roughly £10,000 worth of tines and metal, plus paying for some specialist fabrication.
With nothing really suitable on the farm to pull it, Mr Forsyth hooked it to the Versatile 946 and had a go. It just about managed to drag it along on flat, easy-going ground, but was far from up to the task. It also had nowhere near enough oil flow to power the massive hydraulic fan.
“I knew I would need to get a bigger tractor, but I wanted to get the drill finished and prove it could work before I went shopping,” says Mr Forsyth.
First on the list of potential tractors was a Case-IH Quadtrac 535. However, at approximately £115,000, these were considerably outside his £50,000 budget.
For that money he could only get one of the older 450 models. However, having seen a University of Nebraska study, which showed the 450 delivered just 55hp less than the 535 at the drawbar, he decided to give it a try.
After flicking though the classifieds, he spotted a mechanically sound 2004 Case 450 for sale though Pecks and managed to buy it for £45,000.
The tractor only had 5,500 hours on the clock and had 60% tracks with decent looking idlers, but the paintwork was a tad shabby in places. When the tractor arrived it was treated it to a full service, a partial respray and was fitted with RTK Trimble GPS and an EZ Pilot automatic steering system.
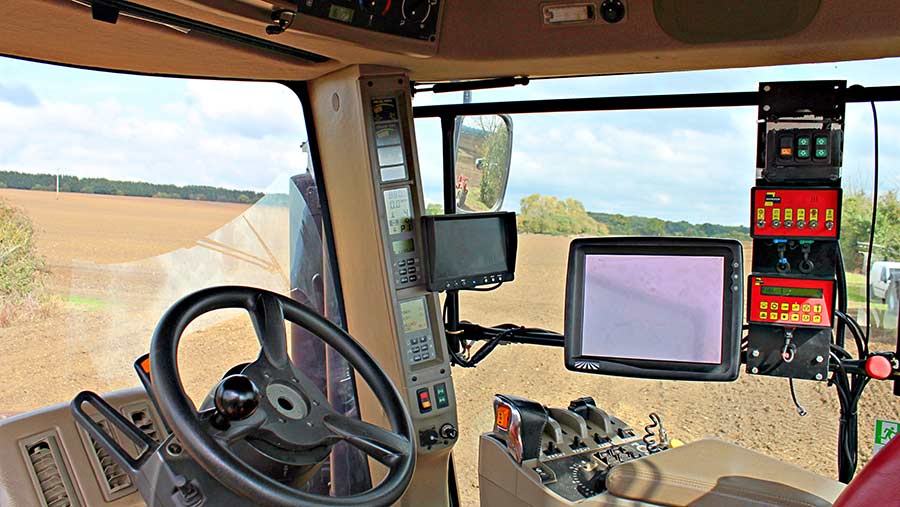
Quadtrac interior © James Andrews
Thankfully the Quadtrac 450 pulled the drill with ease and after doing a few fields as a test in spring 2015 the new rig drilled the farm’s entire 400ha of oilseed rape and a large chunk of the autumn wheat crop.
The results were just as good as the 6m test machine and the only teething problem was a broken drill fan, which landed them with a £2,500 repair bill.
“The fact that there are 82 outlets and no blockage sensors also means the driver has to check each coulter by eye every time he fills up,” says Mr Forsyth.
The only situation where the drill gave a less-than-ideal performance was planting wheat after oilseed rape. Here the open slot cut by the tine allowed slugs to move too freely.
For these conditions, Mr Forsyth decided to have anther stab with a direct disc drill and bought a 6m Weaving GD. He now uses this for sowing all wheat after oilseed rape and it tackles some of the spring drilling, too.
“To do the job properly I think we need both tine and disc drill,” says Mr Forsyth. “The GD’s angled discs move less soil and they tuck the seed in, making it harder for the slugs to find it.”
What’s next?
Despite the C0s decent trash clearing abilities it still occasionally clogs up in particularly heavy crops of chopped straw.
So for his next experiment Mr Forsyth is planning to convert a 6m Horsch Sprinter to Sabre tines. The hope is that the drill’s front packer will crush and consolidate the straw so it doesn’t clog up under the chassis.
Rather than fiddle around with new distribution heads, he says he will look for a seed and fert drill that already has the correct number of outlets for when he doubles the number of tines.
To help fund this next project he plans to sell the original modified Horsch CO6.
Farm facts: A Forsyth Farmwork
Farming: 2,200ha of arable split between owned and contract-farmed ground
Cropping: 50:50 split between winter and spring cropping
Crops: Winter wheat, winter oilseed rape, spring barley and spring oats
Staff: Five full-time, including William, and two part-time
Frontline equipment
Tractors: Case-IH Quadtrac 450 x 2; Versatile 946; JCB Fastrac 8250 x 1, 7230 x 2 7270 x 2, and 3185 x 2
Combines: New Holland CR9090 with tracks and 12m headers x 3
Sprayers: Berthoud Tenor 24m trailed and Boxer 24m self-propelled; Housham 24m self-propelled
Drills: 12m Horsch C012 converted to Weaving Sabre tines and 6m Weaving GD direct disc drill. Vaderstad Rapid and Challenger hired in
Cultivators: 12m Horsch FG, home-made 12m straw rake using sumo strake tines on Will-Rich frame, 12 Vaderstad Carrier, Weaving sub-lift x2, Cambridge rolls and mole ploughs