Wing Jet workshop modification forms 30m Avadex applicator
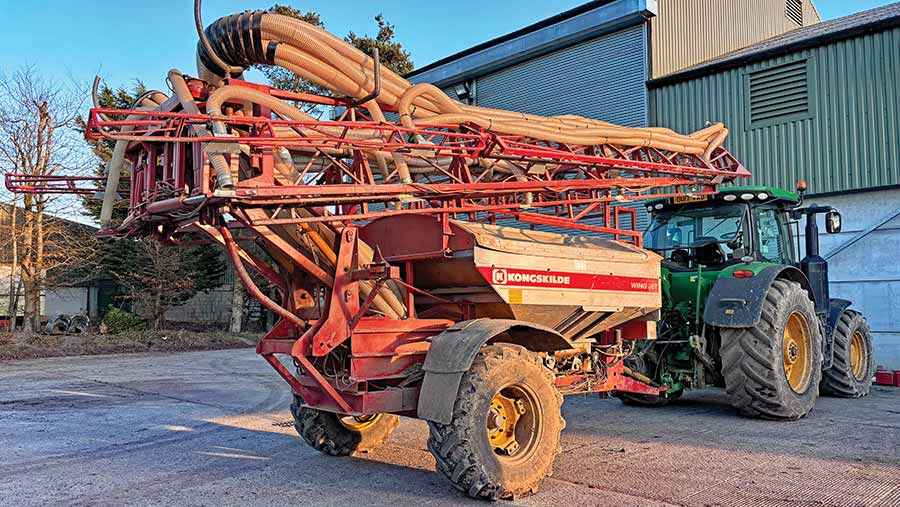
Upsizing from 24m to 30m tramlines meant Buckinghamshire arable farmer Charlie Edgley had a raft of machinery to either upgrade or replace, one of which was his Avadex applicator.
In the old regime, the grassweed suppressing granules were applied using a Kongskilde Wing Jet pneumatic spreader, which also handled the farm’s granular fertilisers.
However, when this was swapped for an Amazone ZGTS trailed spinning-disc machine, he had to come up with an alternative.
See also: Contractors build blackgrass-beating 24m weed wiper
For the first season, Charlie and his team at Kensham Farms, near Stokenchurch, kept using the 24m Wing Jet and put up with the additional wheel marks.
It worked, but the crop struggled to recover where it had been padded down, so something needed to be done.
Several options were put forward, including a sprayer-mounted Techneat Outcast V2 and various applicators that could be fitted to his 10m Dale Eco XL drill or the Cambridge rolls.
All were relatively expensive and lacked the flexibility of a standalone spreader, so the decision was made to widen the Wing Jet.
Kensham Farms’ 30m Avadex applicator
- Base machine Kongskilde Wing Jet
- Boom 30m Knight twin fold
- Outlets 20 Lite-Trac spreader plates
- Metering LH Agro hydraulic metering with four 7.5m sections
- Project price £9,000 to 10,000 (excluding cost of original machine)
Charlie was a bit dubious to start with, but two his staff members, Paul Rogers and Nick Perry, were convinced it could be done.
“They’re both very handy in the workshop so I let them get on with it,” says Charlie.
“Plus, I’d recently spent a lot of money having the spreader converted from land-wheel to hydraulic metering, so I was keen to get some more work out of it.”
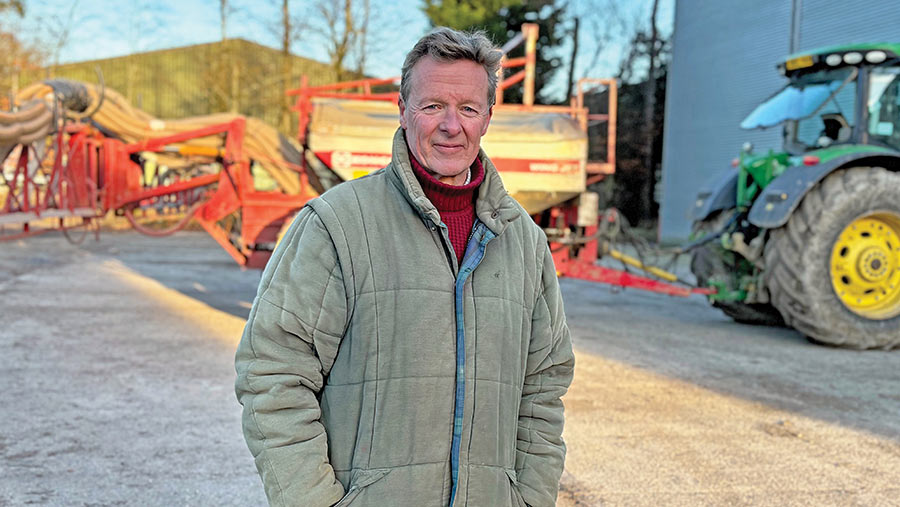
Charlie Edgley © James Andrews
Knight sprayer boom
The first part of the process was to remove the original vertical-folding boom and replace it with a 30m twin-fold unit sourced from Avison Sprayers for about £5,000.
This had been removed from a written-off Knight self-propelled machine, but was in good order and came with all the mounting hardware.
Grafting it onto the Wing Jet involved building a new section of chassis at the rear and fashioning a subframe to support the original boom storage brackets.
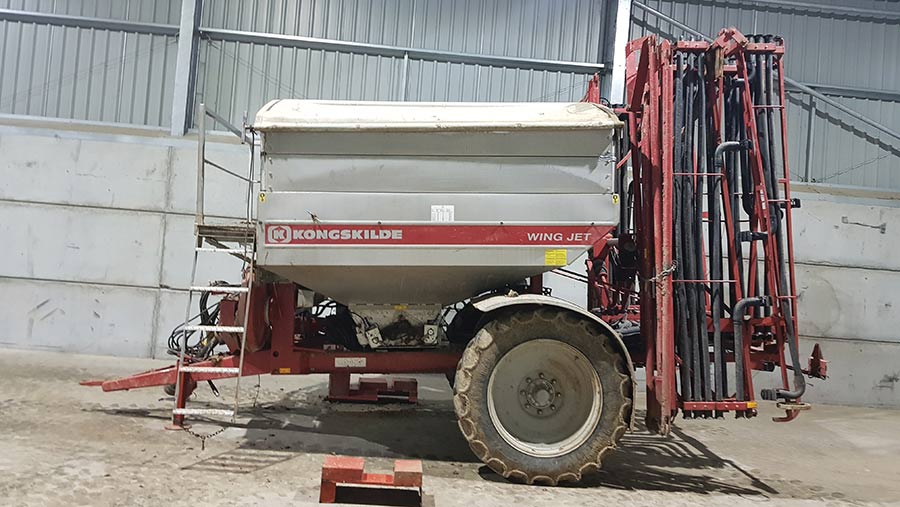
© James Andrews
All this went according to plan, but a surprising amount of extra work went into balancing the machine and making sure the booms didn’t hit the back of the tractor cab when turning.
This involved lengthening the drawbar and shunting the axle back by about 500mm.
A couple of new rams also had to be fitted, as the originals were past their best, and they installed a new set of hydraulic pipes.
Prior to the conversion, they had added a full-width loading platform at the front, accessed by a foldaway ladder, and a rollover sheet.
Mastering the pneumatics
The boom was expected to be the trickiest part of the job, but the pneumatics and associated pipework turned out to be far more challenging.
Initial setup involved fitting 20 lengths of drill seed tube to transport granules from the hopper to the boom.
On the original machine, the pipes fed 20 spreader plates, but in a bid to improve accuracy over the wider spreading width, Y-shaped dividers were fitted on the ends of the pipes, doubling the number of outlets to 40.
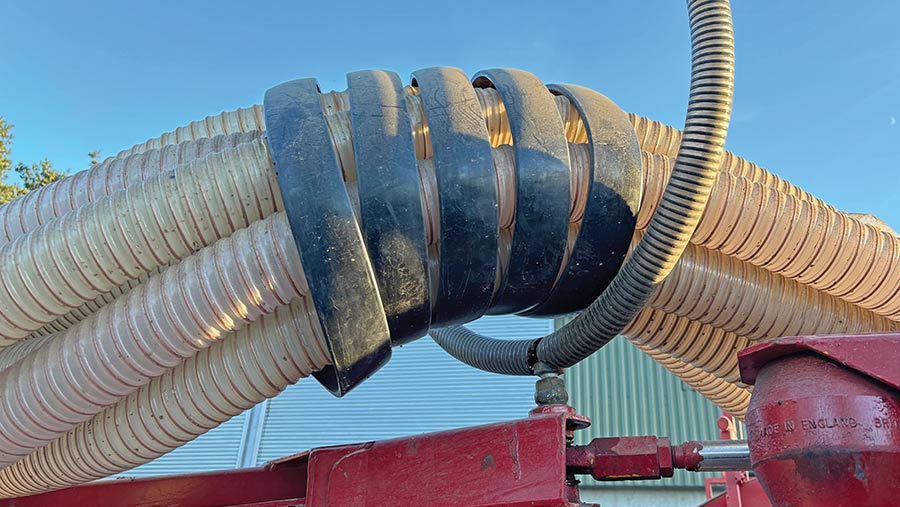
© James Andrews
Each of these had a Stocks spreader plate mounted on the end.
It looked the part, but the long lengths of pipe created too much resistance and the granules failed to reach the ends, instead blowing out of the metering cups onto the floor.
Wooden blanking plates were then fashioned to prevent this from happening, but this caused the granules to force their way back into the hopper, even at modest application rates of 15kg/ha.
“As there’s such a small amount of product going to each outlet and plenty of airflow from the fan, we couldn’t understand why it wasn’t working,” says Charlie.
“We wasted a lot of time trying to sort it and ended up missing an entire season of Avadex application.”
The project was starting to look like a huge waste of money, but as a last-ditch attempt, Charlie got in touch with Paul McAvoy of Lite-Trac, who managed to pull it all together.
His solution was to remove the small-bore seed pipe and replace it with much larger 70mm-diameter tubes, each of which was terminated with one of his own wide spreader plates.
The huge reduction in drag immediately solved the problem, allowing ample airflow for delivering granules at the desired rate.
With 10 of these pipes running down each side of the boom, the next challenge was to find a way to secure them neatly while making sure they didn’t kink or snag during folding.
This involved fitting a series of swivelling brackets and using large coil bindings to lash the pipes together at strategic points.
GPS section control
It was then time to look at the control system. When the spreader was first upgraded to hydraulic metering, it was teamed with a TopCon X30 screen that enabled it to run four-section auto-section control.
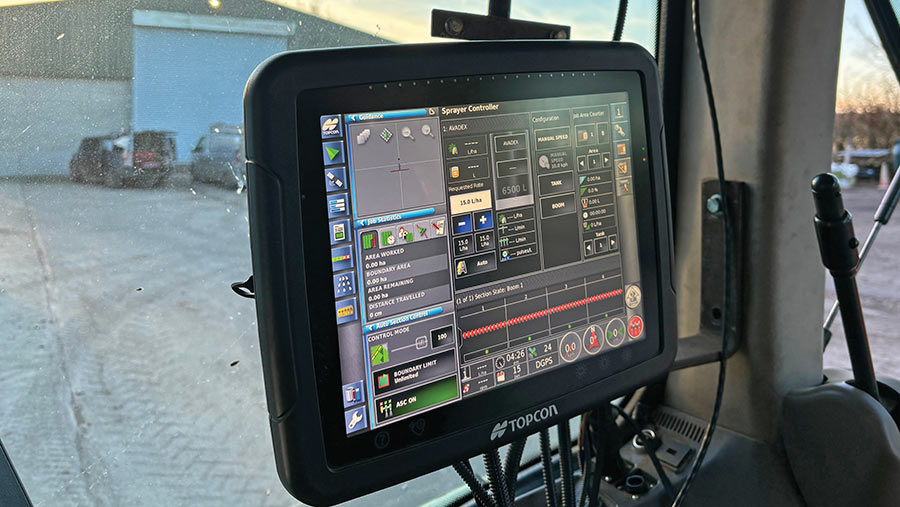
© James Andrews
On the 24m boom, it was configured with 6m sections, so the move to 30m simply involved increasing these in the computer to 7.5m, which Charlie achieved with some help from LH Agro.
Another upgrade carried out at the time of the hydraulic conversion was to replace the original Nordsten electromagnetic clutches, which could give trouble and were expensive to replace.
After a considerable amount of research, Charlie came across some Warner Wrap Spring alternatives – typically found on machines in the food trade – which have proved reliable so far.
However, to help promptly spot problems if they do go wrong, each is fitted with a speed sensor connected to an LED read-out in the cab.
During work, the lights should repeatedly flash on and off, so if they turn off completely or emit a solid light, the driver knows something has gone awry.
Using it
As the farm is situated in the rolling Chiltern Hills and all ground is worked across steep slopes to avoid excessive erosion, wheel tracks on all machines are pushed out to 2.2m centres to maximise stability.
The Wing Jet was given the same treatment, and with a huge set of Trelleborg floatation tyres, it was suitably planted.
A less desirable side effect was the fact the wide rubber padded down too much of the field in damp conditions and the crop struggled where they had been.
They were therefore swapped for a more modest set of 420/85 R24s that strike a better balance.
Work on the applicator was finished ready for autumn 2022, it passed its NSTS test and completed the season without a hitch.
It’s now got through its second without incident, so the pain of its inception is starting to wane.
“It’s great as you can fill the hopper and head out for a full day of spreading without having to nip back to the yard,” says Charlie.
“We stick to a modest speed of 8-10kph, but we can still cover a lot of ground quickly and we have the flexibility to go when we want.”
All in, the project cost between £9,000 and £10,000, not including the original spreader.