Managing welding fumes on farms – all you need to know
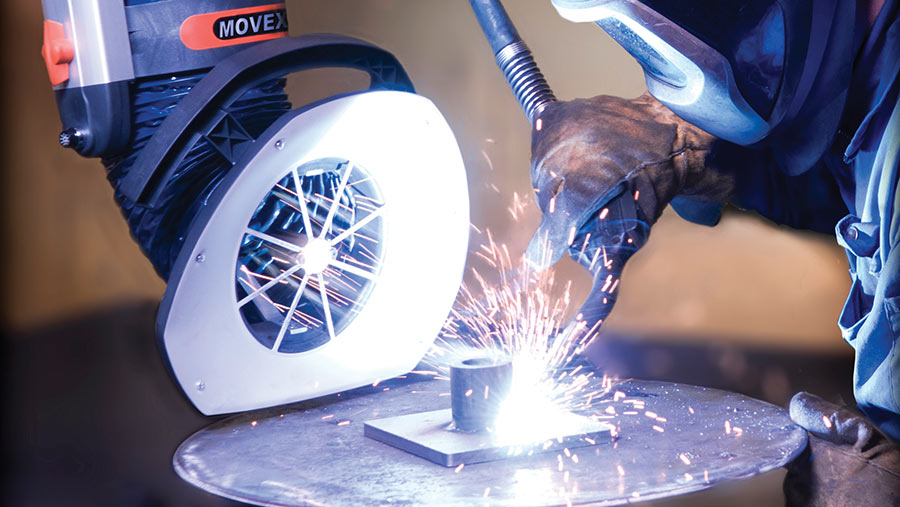
Farm businesses must now understand and mitigate the health and safety risks associated with fumes produced during welding and other metalwork tasks to protect the long-term health and wellbeing of workers.
Rightly, there has been a lot of attention around farm safety recently, as the number of fatalities making the headlines continues to shock.
While addressing the causes of these preventable deaths – mostly from accidents involving machinery, working at height and livestock – should remain a priority, a silent killer also deserves urgent consideration.
See also: Workshop tips: A guide to oxy acetylene gas cutting and welding
Carcinogen
In 2017, the International Agency for Research on Cancer (IARC) published a summary of a very large and comprehensive study in The Lancet Oncology, which classified welding fumes as “carcinogenic to humans”.
The study linked exposure to welding fumes by welders and other workers with an increased risk of lung cancer, while more limited evidence suggests it may cause kidney cancer, too.
Useful links – welding fumes
It has long been known that hot work with stainless steel produces carcinogenic fumes, largely because of its 11% minimum chromium content, and specialists working with the alloy have been mitigating risks accordingly.
However, Stephen Britton of the Health and Safety Executive (HSE) says the most significant thing about the new research and guidance is that it incorporates fumes created by all metals, including mild steel.
This is a game changer for farmers, because it is the most common type of steel used in the production or modification of agricultural machinery, equipment and even buildings.
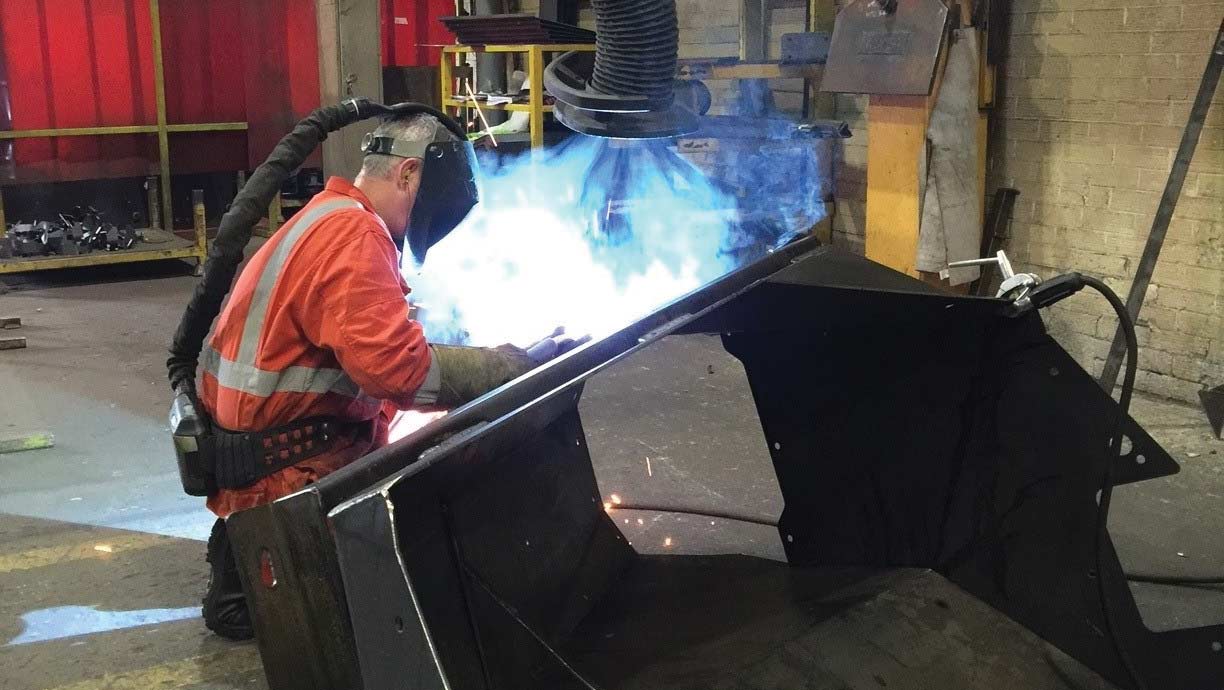
© Auto Extract Systems
No safe limit
In addition, no safe exposure limit has been established, so all welding fumes need to be controlled in some way and in any situation.
“Welding mild steel is much more hazardous than first thought, and even where welding is an ad-hoc operation, some thought on how risk can be reduced is required,” he explains.
When HSE brought in new workplace guidelines last year, there was a big drive within the engineering sector to get companies up to speed with welding safety regulations.
Dr Britton says this has been a relatively successful campaign, largely because many were already familiar with rules around stainless steel, so it was a simple case of widening existing fume controls to any mild steel fabrication.
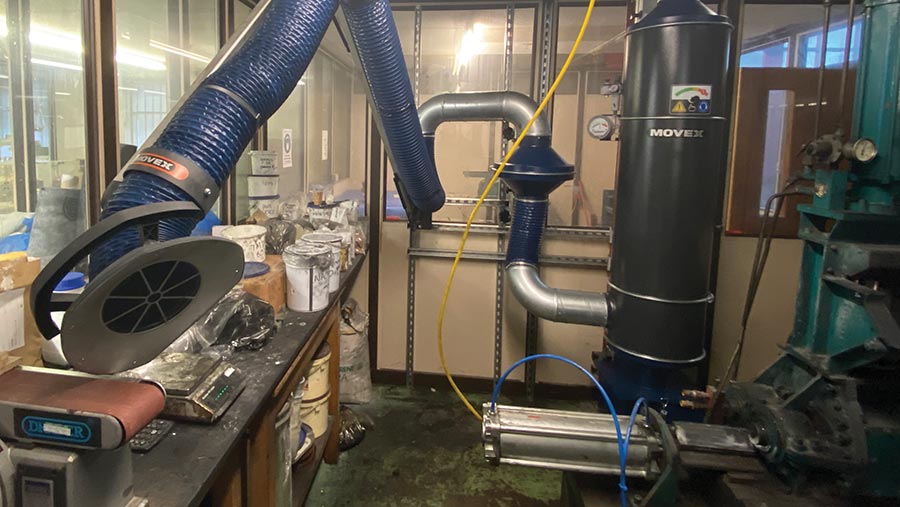
© Auto Extract Systems
A similar drive in agriculture was set for this year as part of wider campaigns, but unfortunately the Covid-19 pandemic has made it more difficult for HSE to get out on farm to help businesses understand and control welding fume risks.
However, it will be a key priority once the pandemic is over, so farmers should take action now to protect themselves and avoid a fee for intervention (FFI) or, worse, penalties for actually harming people.
Here, Farmers Weekly takes a look at what needs to be done.
1. Carry out and record a risk assessment for welding
The very mention of a risk assessment can cause a sense of dread, or sometimes apathy, but it needn’t be complicated or arduous.
This is particularly so in the case of welding on farms, as the vast majority of businesses will only be doing occasional repairs, where the exposure risk is relatively low.
However, for larger businesses, those that enjoy winter manufacturing projects or run a fabrication sideline, longer periods of welding and associated tasks such as cutting and grinding increase risk dramatically.
As with all health and safety risk assessments, it should look to reduce risk in five ways – elimination, substitution, engineering controls, administrative controls and personal protective equipment (PPE) – and record actions the business will take.
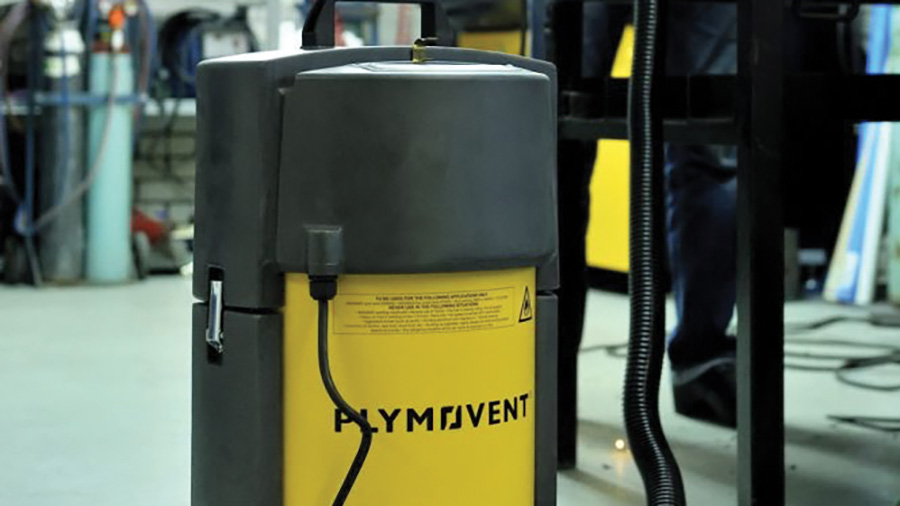
© A.Mac
Some of these will be covered later, but for elimination and substitution there are a few questions to ask.
Firstly, if a big, one-off welding repair or fabrication job comes up and the farm only has dated equipment, would it be better to get a local engineering firm with the relevant safety gear to complete the task instead?
Secondly, can you reduce exposure risk by using alternative methods of joining, cutting or surface preparation that produce less fumes or dust? For example, a MIG welder will produce fewer harmful fumes than a stick welder, so is it time to update your kit?
The figure below clearly shows the relative risks associated with various joining and cutting methods with regards to fume.
2. Use engineering controls
For many ad-hoc welding jobs on farm – such as repairing a cultivator – it can be difficult to use the most effective engineering controls, such as local exhaust ventilation (LEV), unless you have a large and very well-equipped workshop.
In these cases, HSE says where practically possible, every effort should be made to do the job either outside or in a large and well-ventilated building, with the breeze taking fumes away from the welder.
On-torch extraction
When carrying out these types of repairs, or where tacking mild steel box or sheet together during a simple fabrication job, an on-torch extractor for MIG welders could be an option, according to Darren Bell, director at fumes extraction experts Auto Extract Systems.
There are many variations in design but, essentially, a vacuum pulls fumes from the weld pool to a filtration system via the shroud and a pipe that runs around the torch cable.
Mr Bell says they are sometimes unsuitable for longer stints of welding due to the small extraction area, which is limited to the diameter of the shroud on the MIG gun.
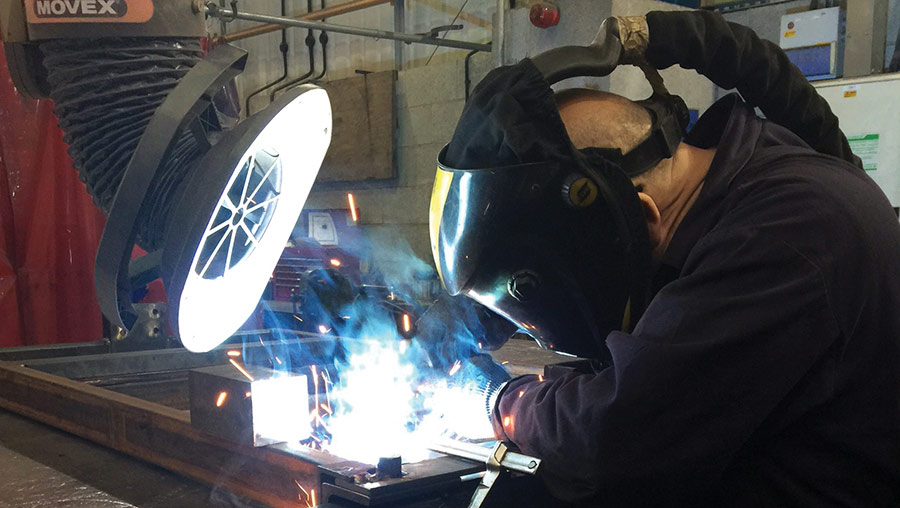
© Auto Extract Systems
For example, if you are doing an intermittent fillet weld, you would weld the first inch and, because it’s still hot and emitting fumes, as soon as you start the second weld, you would be exposed, as the small extraction area has moved on.
In some cases, the vacuum can also interfere with the MIG’s gas shield, leading to porosity in the weld, so while on-torch systems can be useful, they do have their flaws.
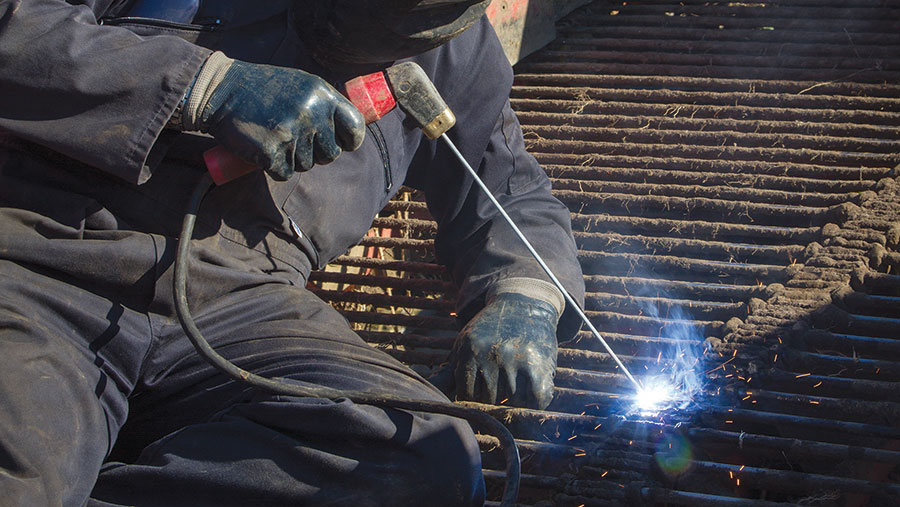
Where it isn’t practically possible to use engineering controls, welding should be done outside or in a large and well-ventilated building © Gary Naylor
Portable LEV
Another option for ad-hoc welds or for those in awkward spots is a portable LEV system, which vary considerably in cost, depending on size and sophistication.
These are typically on wheels and have an adjustable suction arm, so can be moved to the welding site and positioned to draw dirty air into its filtration system. The air is then released locally once filtered.
While these offer a good solution for extracting dust and fumes from grinding tasks, Mr Bell says they do not necessarily offer protection against all particles found in welding fume (see “What are welding fumes?”).
What are welding fumes?
Welding fumes are created when metals are heated above melting point, then vaporise and condense into fumes. The fume is predominantly made up of fine, solid particles, which form a complex mix from wire or electrode, base metal or any coating on the metal.
Welders are exposed to gases when welding, including nitrous oxide, carbon monoxide and ozone. There is also exposure to argon where it is being used as a shield gas (MIG, for example).
Fumes are created to a greater or lesser degree by the following welding methods or associated tasks when working with mild and stainless steel, and other metal materials:
- Manual metal arc (MMA) (also known as stick)
- Metal inert gas (MIG)
- Flux-cored arc
- Tungsten inert gas (TIG)
- Submerged arc
- Electronic resistance welding
- Flame cutting
- Gouging
- Brazing
- Carbon arc or plasma arc cutting
- Soldering
Taking MIG fume as an example, harmful particle sizes range from fine (0.01-1 micron) to coarse (1-10 microns), with the majority in the fine range. This is important when choosing which engineering control or RPE to use.
What are the health risks when working with metal?
- Ultraviolet (UV) radiation Arc welding generates UV light, which is a risk factor for the rare cancer ocular melanoma (eye cancer) and other eye disorders such as cataracts and keratoconjunctivitis (inflammation of the cornea and conjunctiva).
- Welding fume Short-term effects include respiratory irritation, reduced lung function and metal fume fever (flu-like symptoms). Long-term effects include lung cancer, possibly kidney cancer, nervous system damage and increased susceptibility to lung infections such as pneumonia.
- Cutting/grinding Dust containing metals, metal oxides and potentially respirable crystalline silica (RCS) are associated with occupational asthma and other chronic lung conditions.
This is because the filters contained in the moveable LEVs are typically rated to trap particles down to three microns in diameter, but the most harmful gases in fumes are as small as 0.1 micron.
This is something that employers should be aware of when selecting the appropriate LEV, particularly if workers will be using it in confined spaces for long periods.
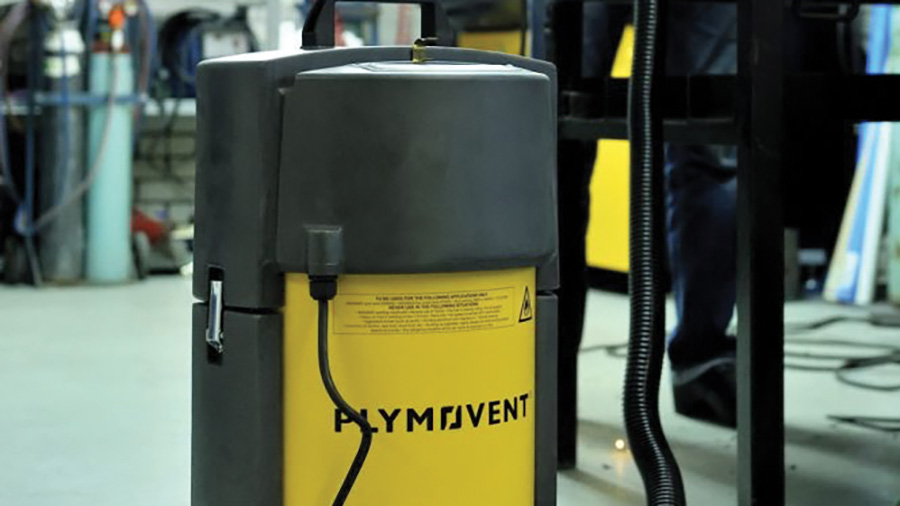
© A-Mac
Extraction arms
In these situations, the safest way of carrying out hot work is to take it to a bench with an extraction arm installed close by.
Extraction arms are secured to a wall or building steel and comprise a long, flexible PVC or stainless-steel hose, with a capture hood on the end.
The capture hood can be moved and adjusted to remove fumes and dust from the workspace by a centrifugal extraction fan. It is then taken through a replaceable filter or more sophisticated self-cleaning filtration system before exiting the building.
Mr Bell says for most farm workshops that are welding and grinding regularly, a 4m extraction arm and a standard extraction system with replaceable filter would suffice, costing about £4,000.
Where opting for a self-cleaning version, price would increase to about £6,000.
Farmers Weekly understands that some farm businesses have built their own LEV systems. While these are better than no LEV at all, in the long term it will be much safer to invest in specialist equipment that is regularly maintained and tested for efficacy.
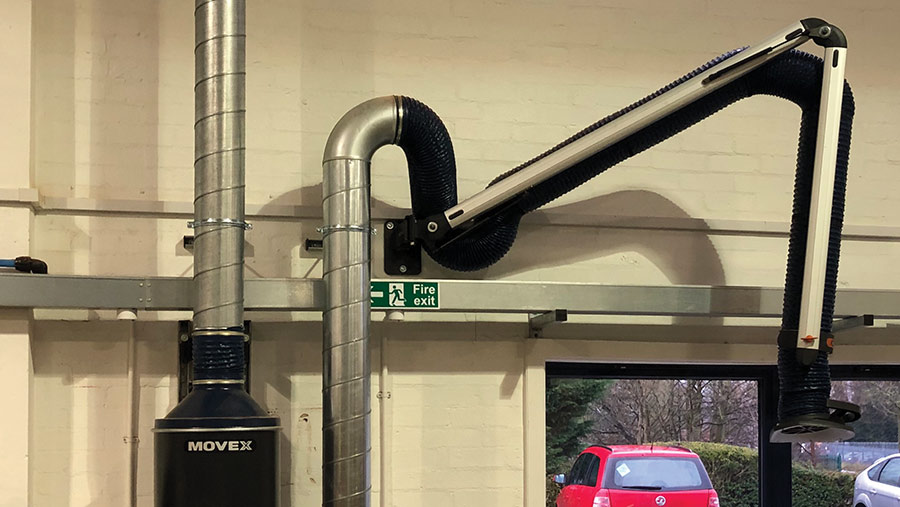
© Auto Extract Systems
Servicing and maintenance
Under the Control of Substances Hazardous to Health (Coshh) regulations, LEV suppliers have to provide three documents on installation, including a manual, logbook and commissioning report. These must be present and up to date at all times.
Once up and running, LEV equipment should be well-maintained, and inspected and tested every 14 months. Most suppliers will provide this service for about £120 an inspection.
Some service providers will maintain LEV records in a cloud-based platform, which allows users to download the relevant documents when required, avoiding the risk of loss or damage.
3. Use respiratory protective equipment (RPE)
Engineering controls such as LEV must always be the primary tool to reduce exposure to fumes, but farm businesses should also provide workers with appropriate RPE for welding and associated jobs.
HSE advises the use of an FFP3 disposable mask or half mask with P3 filter for jobs taking no more than one hour. This needs to be upgraded to a battery-powered air-fed device with a minimum assigned protection factor of 20 (APF20) for longer stints of hot work.
Like portable LEV, Mr Bell again cautions that RPE won’t necessarily take out smaller harmful particles.
In the case of an air-fed device, he advocates using an external air source to ensure contaminants aren’t sneaking through its filtration system.
Many well-equipped workshops will have a compressed air system and while air straight from a compressor isn’t breathable, fitting a coalescing filter will remove contaminants and allow it to be safely used by air-fed RPE systems.
On top of choosing the correct RPE, employers should also ensure that it fits correctly by conducting a fit test. This is best done when purchasing the kit to ensure it is effective on the staff wearing it.
As most RPE relies on a good seal against the skin, having stubble or beards should be avoided if any amount of welding forms part of the employee’s role.
However, if there is a good reason to have a beard (religion, for example), then RPE such as powered hoods might be appropriate and eliminate the need for a seal on the face (they tend to fasten around the neck).
4. Provide adequate training
Whether you do your own welding, or have employees that are required to weld, training is one of the most important tools to make the operation safe.
Paul Woodhouse of Shropshire-based Telford Group, which provides welding training nationwide, says all its available courses have been updated to include the latest Coshh regulations.
He says it is important that farmers and their employees are educated in this area and it’s not viewed as another unnecessary and costly box-ticking exercise.
“That is where the training comes in. We can talk things through, show why it’s now a requirement and ultimately, that it’s a good thing for both short- and long-term health.”
As an example, the Telford Group’s basic one-day welding course covers updated health and safety guidance, plus a refresher on practical welding. This is ideal for farmers and workers already proficient in welding but need an update on the new regs. It costs £350-£400.
For those who want to take their knowledge and skills up a notch, an ISO 9606 Welder approval course is also available (often referred to as becoming a “coded welder”).
For mild steel, the two-day ISO 9606-1 Qualification test of welders – fusion welding course would cost about £750. Additional sessions are available for those working with alloys such as aluminium.
While these give an idea of the type of training on offer, Mr Woodhouse says anyone interested in a welding course should contact their training provider, as some will offer a bespoke service based on employee/employer needs.
Common cancer-causing fumes |
||
Fume type |
Source |
Carcinogen |
Beryllium |
Hardening agent found in copper, magnesium, aluminium alloys and electrical contacts |
Known |
Cadmium oxides |
Stainless steel containing cadmium or plated materials, zinc alloy |
Suspected |
Chromium |
Most stainless steel and high-alloy materials, welding rods. Also used as a plating material |
Some forms are carcinogens |
Nickel |
Stainless steel, nickel-chromium, nickel-copper and other high-alloy materials, welding rods and plated steel |
Increased cancer risk has been noted in occupations other than welding |
Source: IARC/Cancer Council |