Inventions Competition 2024: Neat ideas for livestock farms
From crafty modifications to high-tech implements and self-propelled machines, this year’s Farmers Weekly Farm Inventions Competition had it all.
We round up the best of the entries for livestock farmers.
See also: Tips to get the perfect solar-powered electric fence setup
Drew Kennedy’s grass broadcaster
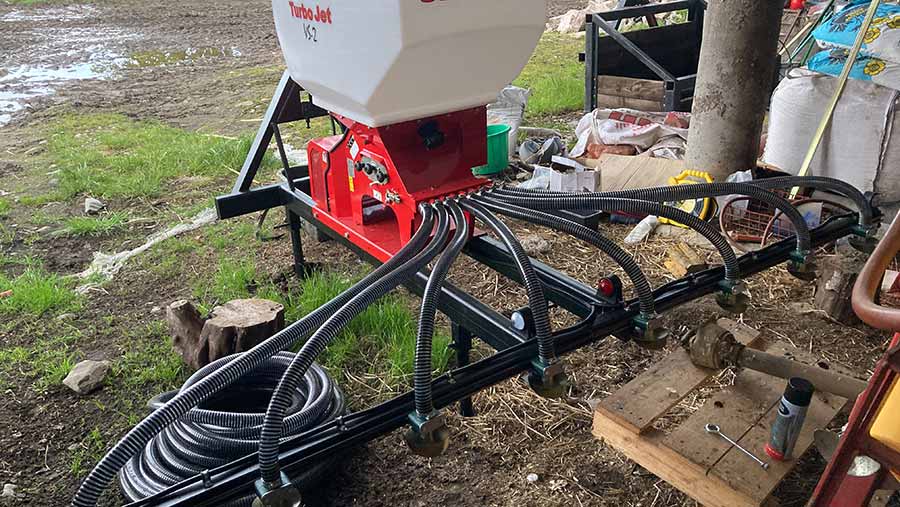
© Drew Kennedy
After failing to find a grass seeder that suited his requirements, Drew Kennedy bit the bullet and made his own.
It was designed to mount on the front of his 150hp Valtra, primarily because he could then tow a heavy flat roller behind to complete the job in a single pass.
The other advantage of this setup, he says, is that the grass and clover is applied on level ground without any wheel markings.
The more consistent sowing depth has allowed him to cut his seed rate back by 5kg/ha.
The most expensive part of the build was a new Stocks Turbo Jet VS-2 applicator.
This came with a speed sensor that ensures the application rate is accurate, irrespective of any wheel slip on the steep hills around his base in Aberfeldy, Highland Perthshire.
The eight pipes plumbed in below the Turbo Jet run to spreader plates on the 3m boom, delivering a quadruple overlap of seed for a denser sward that gives weeds less space to establish.
He has been pleased with the results, not only for grass, but also other small-seeded species such as fodder rape.
On occasions, he also blocks half of the outlets and removes the spreader plates from those that remain open, so he can drop chickery and canary grass game cover in 450mm rows.
Neil Ryall’s mobile hammer mill
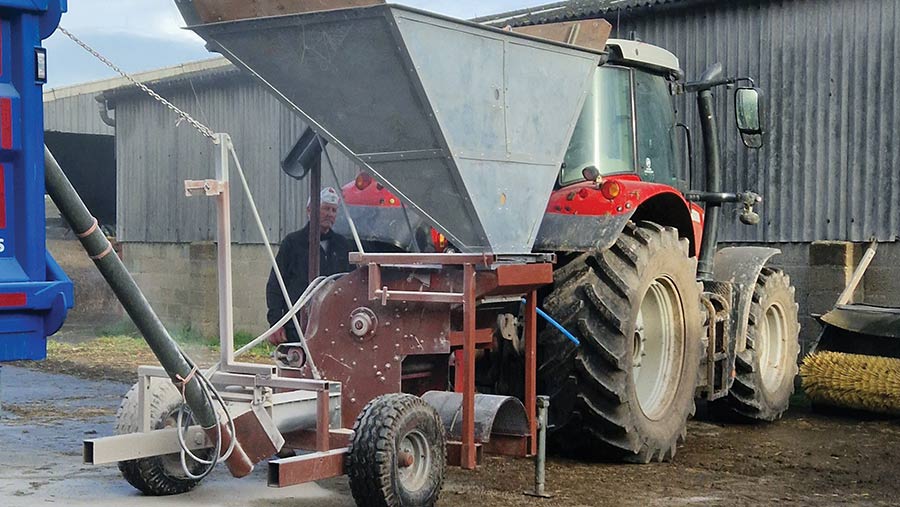
© Neil Ryall
To make better use of the 80ha of cereals and beans he grows on his Oxfordshire farm, Neil Ryall assembled his own low-cost mobile hammer mill.
This allows him to process the crops at his leisure, rather than relying on a mill and mix contractor. And, once he’s accumulated a full 28t artic load, it is hauled to his brother’s 180-cow dairy farm 50 miles away in Wiltshire.
About half-a-bucket of grain can be loaded into the pyramidal hopper at one time. From this, it runs into a pto-powered Gehl hammer mill, which Neil picked up for £1,000 complete with new hammers and bearings.
When not in use, the second of the two augers can be swung over to be stored neatly in its own mounting slot along the nearside of the hopper.
All of the components are carried on a home-made chassis complete with new stub axles and wheels.
Output is roughly 5t/hour – double that of the small Christy 4000 roller mill he uses daily to make feed for his own 180 head of cattle.
John Roberts’ weed wiper
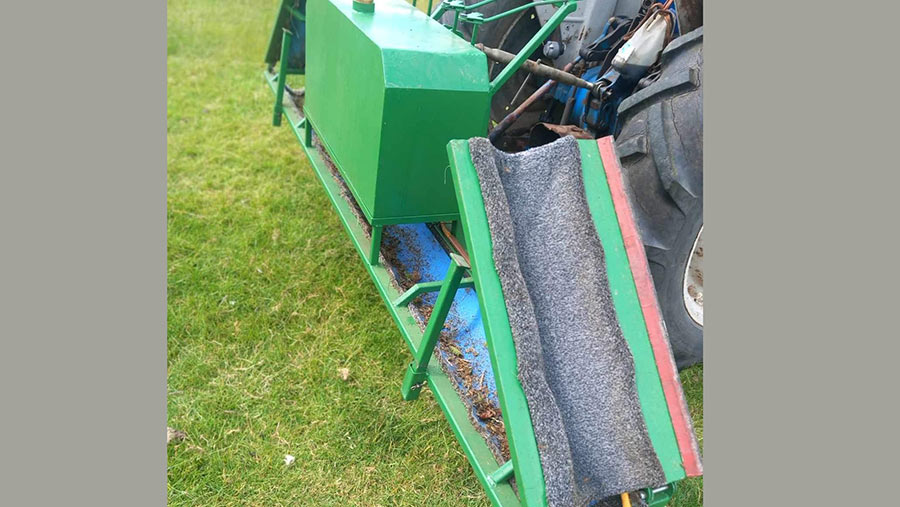
© John Roberts
Powys beef and sheep farmer John Roberts built a simple tractor-mounted weed wiper that goes without the complication of electrics and hydraulics.
Instead, glyphosate is gravity-fed from the home-made, 90-litre steel tank through four taps threaded into its base.
These are opened and closed via handles on long stalks, allowing him to quickly alter the flow of liquid through the four sections of weeping pipe by reaching out the back of the tractor cab.
For particularly undulating ground, he can close two taps that feed the outer wings.
This reduces the width from 4.5m to just under 3m, ensuring he hits any weeds growing in dips and hollows.
The wiping element was made from lengths of carpet, sourced as off-cuts for just £40, which are hung between lengths of box section roughly 300mm apart.
To maximise the efficacy of the herbicide, he has also fitted a blade on the front to scratch tougher weeds such as thistles, scraping the skin off to speed up the kill rate. When not in use, it sits on four legs and can be moved relatively easily by two people.
His total spend was about £350.
Andrew Carbis’ feed blower
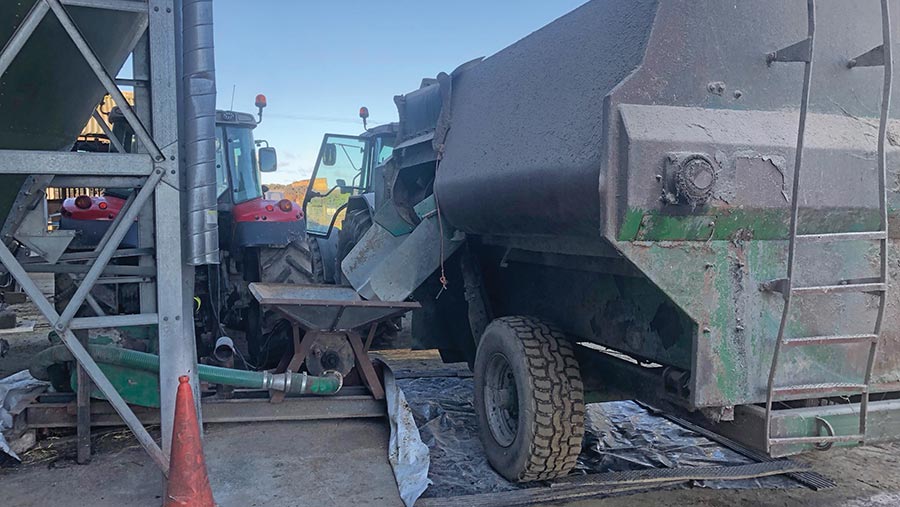
© Andrew Carbis
In search of a low-cost method of home mixing parlour feed, Cornish dairy farmer Andrew Carbis teamed his back-up Keenan 170 diet feeder with a workshop-built blower setup.
The process starts by blending a 4.5t batch of crimped barley and protein pellets in the diet feeder, along with molasses tipped in from an IBC.
Once fully mixed, the load empties into a small hopper mounted above a dosing system and blower salvaged from an old feed lorry, which fires it into the parlour feed bin.
The blower was converted from prop-shaft to pto drive so that it can be run off a second tractor sitting next to the one turning the diet feeder, and the hydraulically driven dosing system is connected to one of the tractor’s spool valves.
By adjusting the hydraulic flow on the tractor, Andrew can vary the amount of feed that’s wound into the air flow to maximise efficiency without risking blocking the blower or pipework.
Andrew says the setup has reduced feed costs to one-quarter of bought-in alternatives when using home-grown barley, which represents a cost saving of £80-£90/t.
Total build cost was £1,000, most of which went on the blower unit and dosing chamber.
Malcolm Wain’s stripper header and mower combination
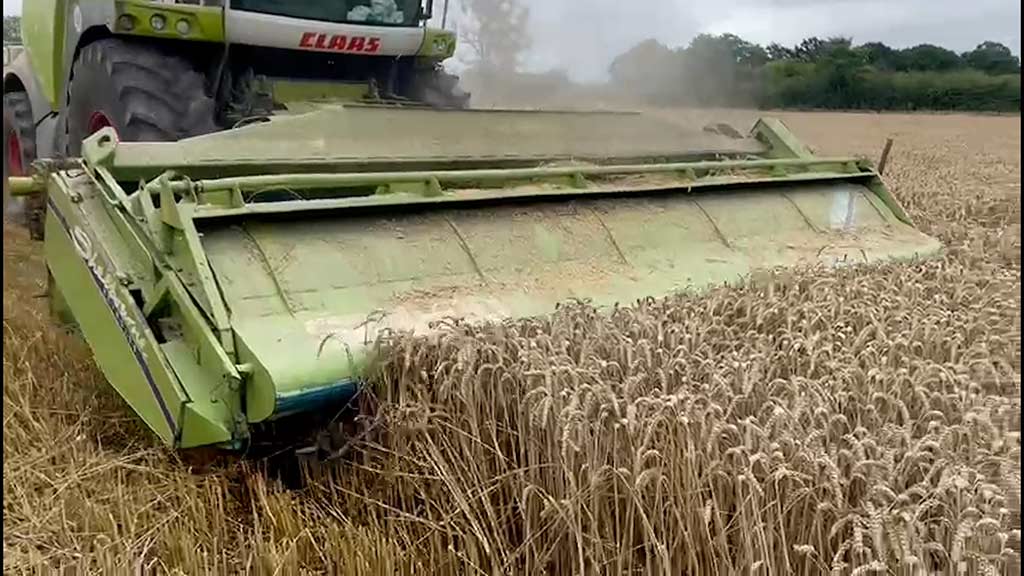
© Malcolm Wain
Staffordshire farmer Malcolm Wain has developed a natty way of harvesting cereals for his dairy herd.
Rather than wholecropping it, the Claas Jaguar forager is instead fitted with a Shelbourne Reynolds stripper header that whips off the grain, sending it through the forager’s internals and out the spout.
This means he can apply a dose of additive at the same time.
The standing straw is then chopper by a disc mower mounted below the extended feeder house, leaving it in a neat swath ready for baling.
Ken Hopkins’ fencing wire winder
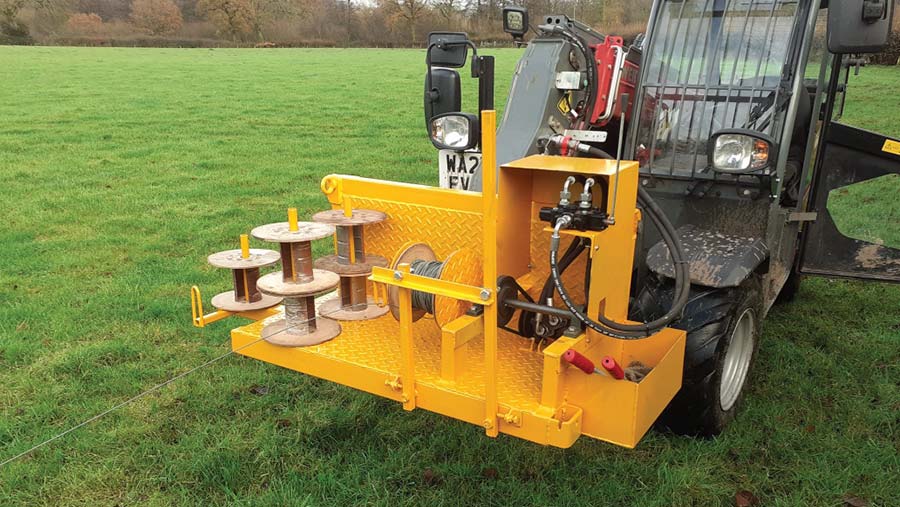
© Ken Hopkins
Suffering the familiar problem of fence posts rotting off while there’s still plenty of life left in the plain and barbed wire, Devon farmer Ken Hopkins built a tool for salvaging it.
His winder is carried on a frame that hooks to the front of his telehandler and it uses a hydraulic motor operated via a variable spool valve to gather used wire onto bobbins. A series of sprockets and chains get it running at a sensible speed.
As it’s being loaded, the wire runs through an adjustable guide that the operator can shift from side to side using a lever to ensure even winding.
Once full, the bobbin can be placed on one of the integrated storage poles.
There’s also a side bobbin holder for winding wire out onto new fences and a storage box for tools and equipment.
The tool will work with mild and high-tensile plain wire up to 3.2 gauge, as well as mild and high-tensile barbed wire.
Jack Conner’s lamb creep feeder
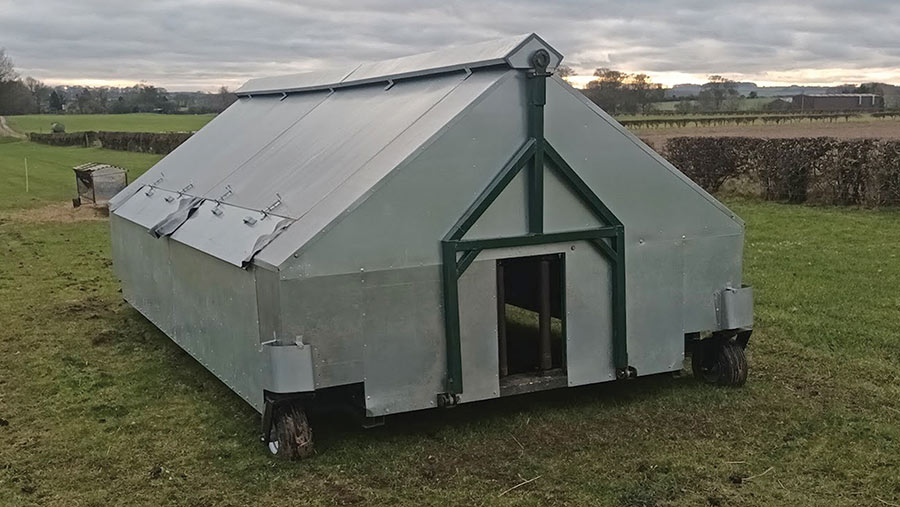
© Jack Conner
Unimpressed with the design of off-the-shelf lamb creep feeders, Yorkshire farmer Jack Conner built his own featuring a tough box-section steel frame clad with galvanised steel.
Adjustable rollers are fitted in the openings to control access and the feed hoppers are filled by lifting external lids on either side.
Ventilation slots are incorporated into the apex of the roof and it runs on wheels, which allows it to be moved around easily by the farm’s Kubota UTV.
The frame was all Jack’s own work, but he got some help from a local engineering firm to cut and fold the galvanised sheet.
James Cooper’s bucket auger
Fed up of shovelling grain into cattle troughs twice a day, Inverurie farmer James Cooper decided to build a feeder bucket.
He found an old auger and a hydraulic motor on a scrap heap, which he married together using a bought-in pulley and a belt, before bolting the assembly into his grain bucket and connecting the hydraulic pipes to the telehandler’s third service.
Now he can scoop up grain and drive down the feed passage as the auger winds it out. It’s been used twice a day for the past eight years and cost just £20 to put together.
The only modification has been to fashion a pulley cover out of an old mineral bucket, as the belt tended to slip when it rained.
The auger is only attached to the bucket with a bolt at the top and bottom, so it’s simple to remove when not required.
John Coleman’s bulldozer post knocker
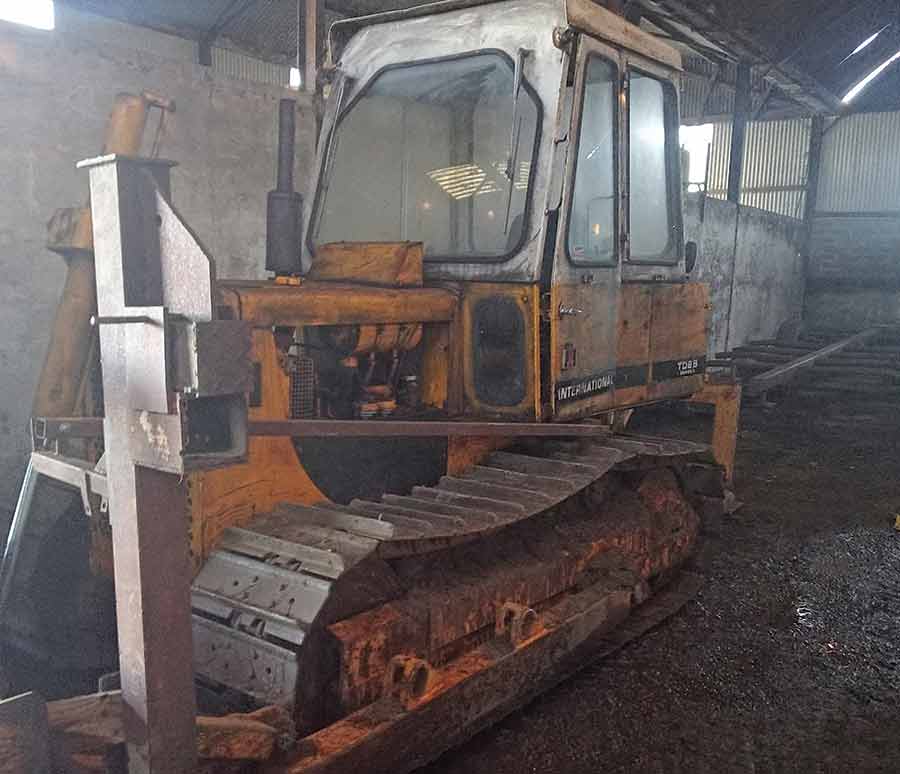
© John Coleman
Looking for a low-cost method of pushing in fence posts, Northern Irish farmer John Coleman fashioned a simple knocker that mounts to the side of the blade on his International TD8B crawler.
To make sure it travels in a straight path and hits the top of the post square, he attached it using a scissor linkage and he built it from heavy box-section steel to make sure it stays in one piece.
He says it works well and the tracked machine travels easily on wet ground, causing considerably less compaction than a tractor. The fact that the knocker is side-mounted also means he can drive along the line of a fence without having to turn and churn up the ground.
Arwel Davies’ lambing shed shelf
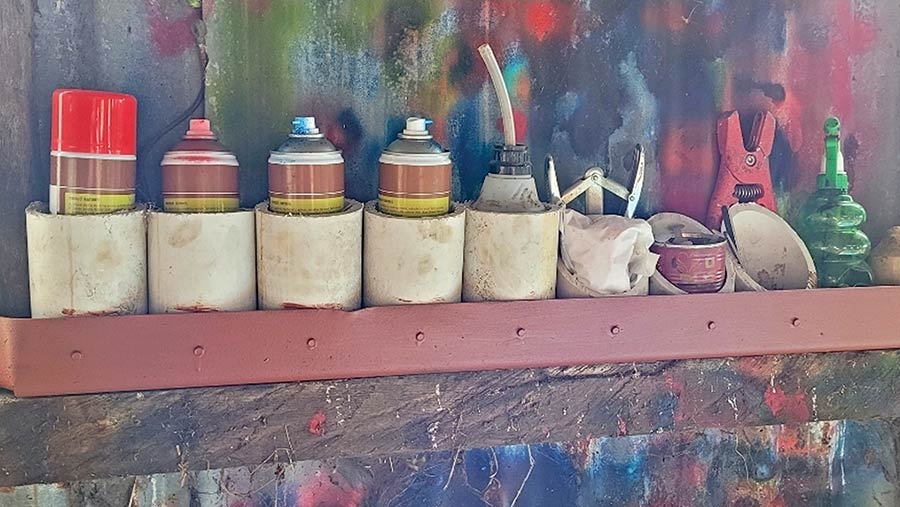
© Arwel Davies
Keen to find a way of stopping marker spray and other paraphernalia getting knocked onto the lambing shed floor, Ceredigion farmer Arwel Davies built a slotted shelf.
The main support was a length of lightweight angle iron from an oil tank, which he screwed to the shed and filled with short lengths of plastic bale wrap centre tube, which were the right diameter to hold a rattle can.
He also cut some of the pieces at an angle, making it easier to access smaller items. The tubes are secured into the angle iron using short self-tapping screws.
Trevor Davey’s solar-powered fencer

© Trevor Davey
Devon farmer Trevor 75 has assembled a low-cost solar array to power his electric fence.
After shopping around, he found a 10W, 400x280mm solar panel from Solar Technology for just £40 – one-third of the price charged by mainstream agricultural distributors.
This is mounted on a couple of galvanised 45deg brackets to the lid of an old feed box.
The battery is slotted inside, where it sits on a block of high-density insulation board and is sandwiched down the sides by filler foam.
This makes for a weather-proof case that has eliminated any cold-induced deterioration, so it has run a 600m length of twin-wire sheep fencing since the summer with no need to recharge it in the intervening period.
The leads from the panels are held against the top of the battery terminals by self-tapping screws, leaving plenty of space to attach the crocodile clips for the Falcon Hotline energiser.
Graeme and Steven Christie’s portable gate
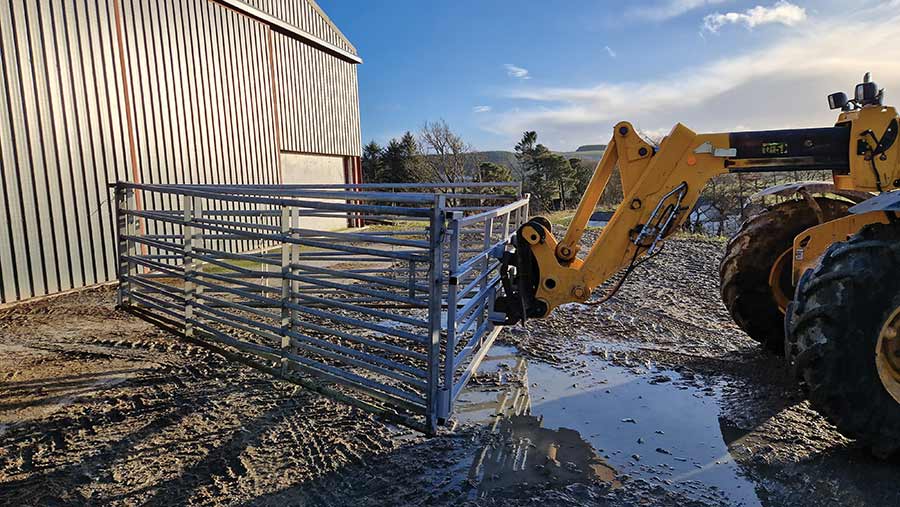
© Graeme and Steven Christie
Previous simple category winners, brothers Graeme and Steven Christie, returned to this year’s competition with their 18m portable gates.
The Banffshire natives assembled five separate gates that are hinged together and attached to the JCB telehandler via a quick-release bracket.
This means they fold up for easy transport and can be set up in less than a minute when required, saving the usual faff of forming temporary barricades when moving sheep or cattle.
Ken Hopkins’ solar-powered fencer
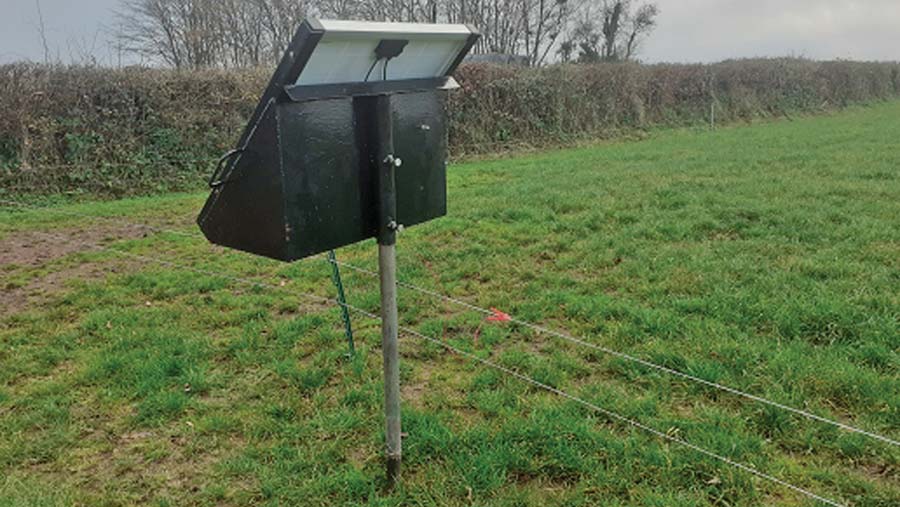
© Ken Hopkins
When putting his sheep on winter keep, Ken Hopkins wanted a secure and maintenance-free electric supply that was capable of putting out a decent punch over 1,000m of fencing.
His solution was to build a self-contained unit with a 2J fencer running off a 40Ah battery, which is charged by an 80W solar panel. He says the setup is entirely self-sufficient, capable of running 24 hours/day, 365 days/year, even taking the shortest and cloudiest winter days into consideration.
To make it both easy to use and hard to tamper with, he built a neat steel box to house the fencing unit, charge regulator and battery, which the solar panel bolts to the front of.
The whole setup is designed to slot onto a length of galvanised scaffold pole, which can be driven into the ground to give it a secure mounting and provide an earthing.
Kenny Fraser’s weigh crate trailer
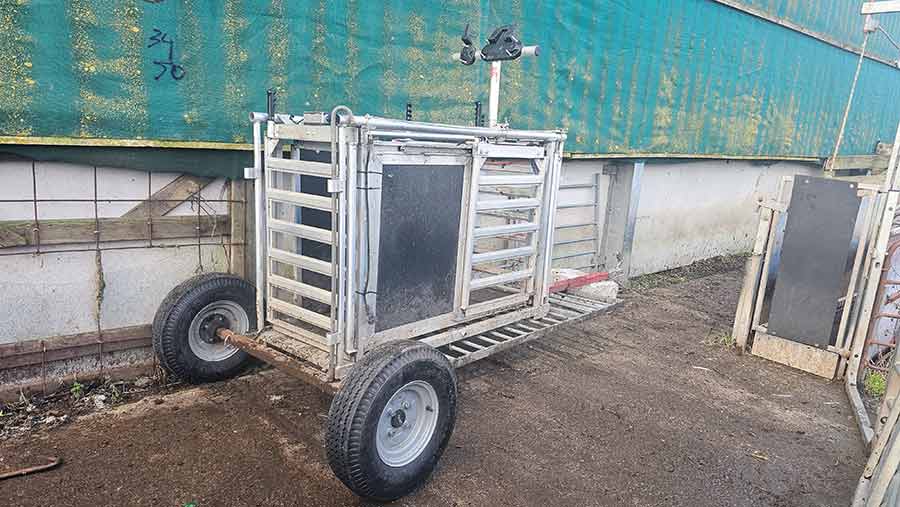
© Kenny Fraser
With ewes and lambs spread across 17 different fields in the summer, Fife farmer Kenny Fraser grew increasingly sick of the squished fingers and pulled muscles caused by constantly lumping his lamb weigh crate into the back of the pickup.
His solution was to bolt it to a purpose-built trailer, which was made from a spare metal fencing panel.
This has a far bigger footprint than the crate, making it more stable on wet and undulating ground. As a result, it gives far more accurate weight readings.
To the front he grafted on a length of 4in box section with a ball hitch coupling, and more of the same steel was used to form sockets further back.
This allows him to slide the stub axles out to drop it to ground level once in the field.
The total construction time was less than three hours, and the bill for the hitch, stub axles and wheels ran to £250.
Tom Charge’s telehandler mirror bracket
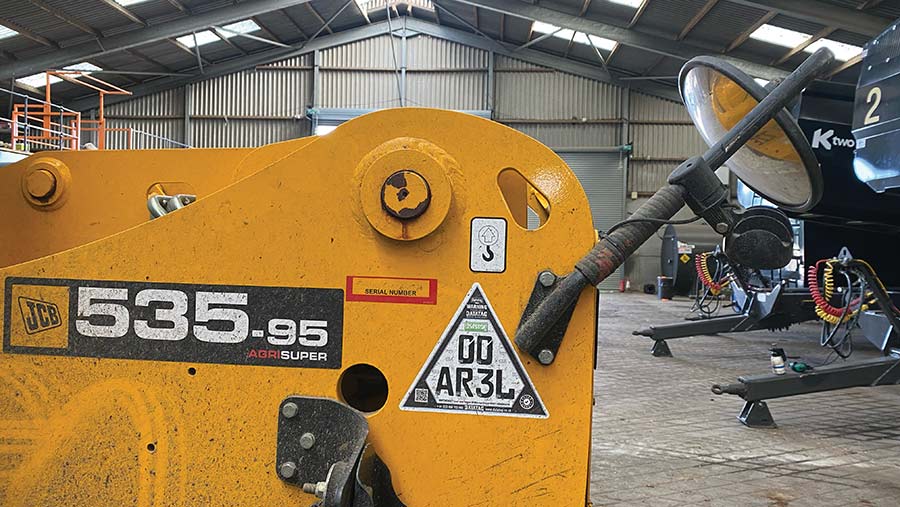
© Tom Charge
Shed stanchions have seen to the end of many a telehandler pick-up hitch mirror, but Buckinghamshire-based Tom Charge has come up with a simple means of minimising the damage.
By replacing the short length of steel that connects mirror and machine with a length of old hydraulic pipe, the version fitted to the farm’s JCB 535.95 Agri-Super has far more flex for those who drive by touch rather than eye.
Meredith George’s budget dryer
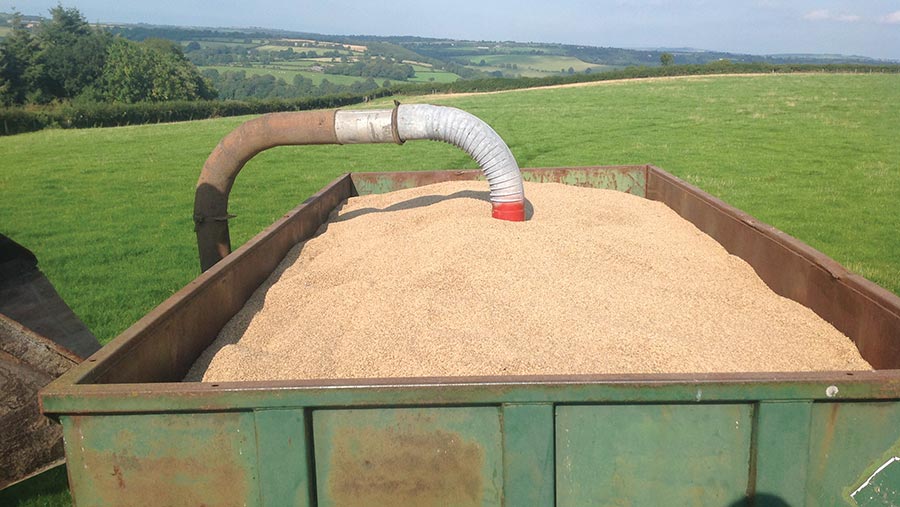
© Meredith George
By fitting a false mesh floor in his grain trailer, Pembrokeshire farmer Meredith George has formed his own lost-cost batch dryer.
He tends to blast fresh air down the central pipe but, for more effective drying of grain or woodchip, he can also rig up a workshop heater to warm the wind as it leaves the fan.
Peter Scott’s ‘sheep shedder’
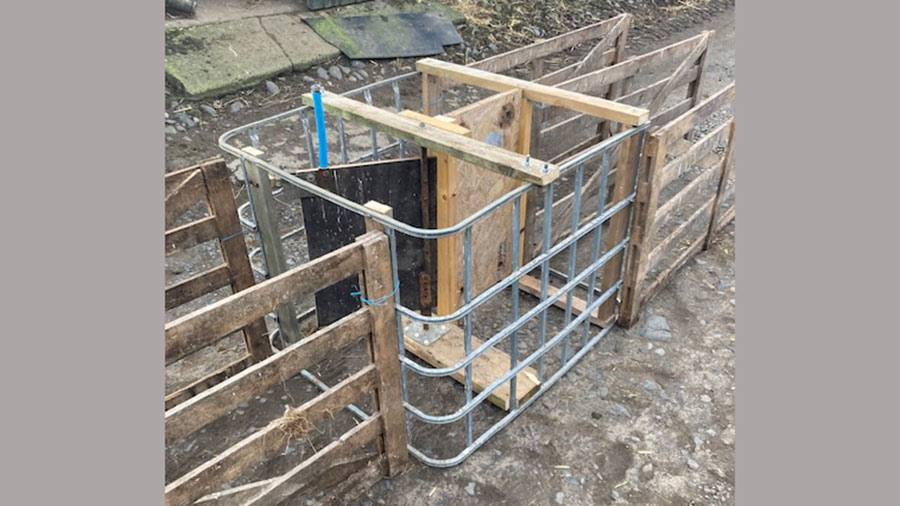
© Peter Scott
Peter Scott of Alnwick, Northumberland, assembled a budget drafting gate housed inside an old IBC cage. A few wooden hurdles help to guide the sheep in and out.
It took a little over three hours to put together and, he says, has been a handy backup for handling stock around the farm.
Kenny Fraser’s pin holder
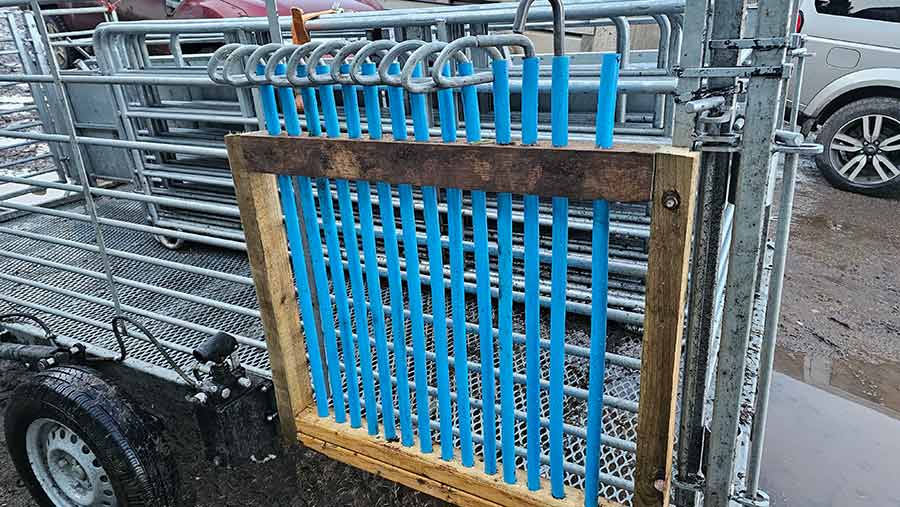
© Kenny Fraser
Lost gate pins are no longer a problem for Kenny Fraser, thanks to a simple holder attached to his mobile sheep trailer.
Rather than being left in the gates for transport, where they’re at risk of bouncing out, the pins are instead slotted through lengths of 25mm MDPE water pipe set inside a wooden frame.
This means they are always with the gates and, as they sit snuggly in the pipes, they no longer rattle around, making the trailer far less noisy when being towed between fields.
Richard Coleman’s sheep snacker
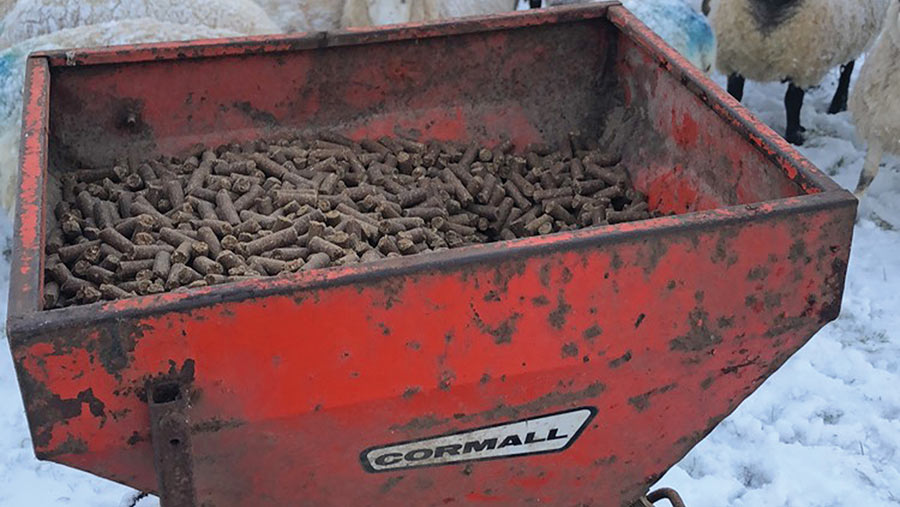
© Richard Coleman
Northern Irish farmer Richard Coleman liked the idea of using a trailed snacker to feed on fresh ground every day.
But having to move the quad bike long distances between blocks of land, it would have been a clumsy outfit to repeatedly load onto a trailer behind his Land Rover.
His solution was to build a smaller unit that mounts to the rear rack of his ATV, fashioned using a hopper from an old Cormall feed mill.
A simple frame was made so that it could be attached to the rear of the bike, and he built a chute with a lever-operated paddle to start and stop the flow of pellets.
William Baird’s track grader
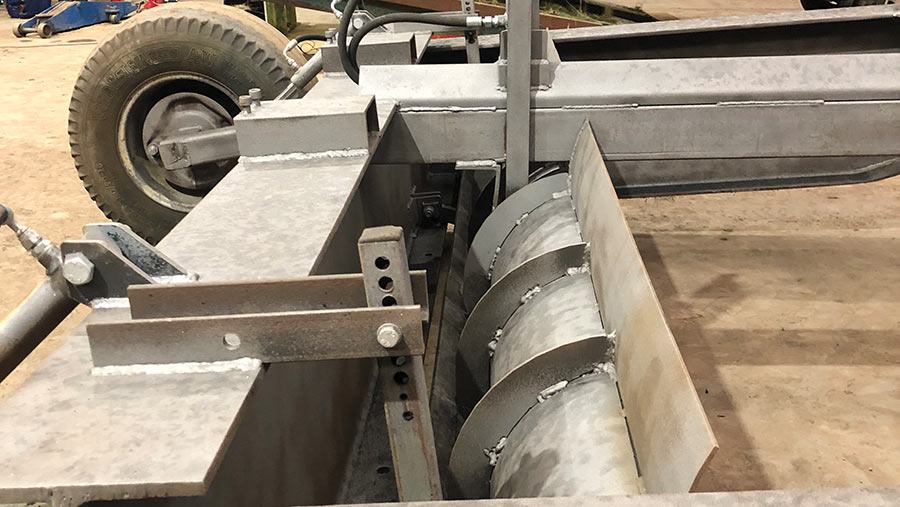
© William Baird
Plenty of heavy-duty metal went into the fabrication of William Baird’s “Farm Freeway System” track grader.
A loading shovel bucket blade carves off the top later of material, with its position set by a central hydraulic ram. This is then locked in place using hole-and-pin brackets at either end.
The wheels at the back can also be lifted and lowered hydraulically, allowing them to be tweaked individually to form a camber.
Connecting the rig’s drawbar to a quick-hitch system on the rear linkage of the tractor allows him to tweak the pitch, thus altering the amount of material applied to the track.
Peter Richardson’s hydraulic engine starter
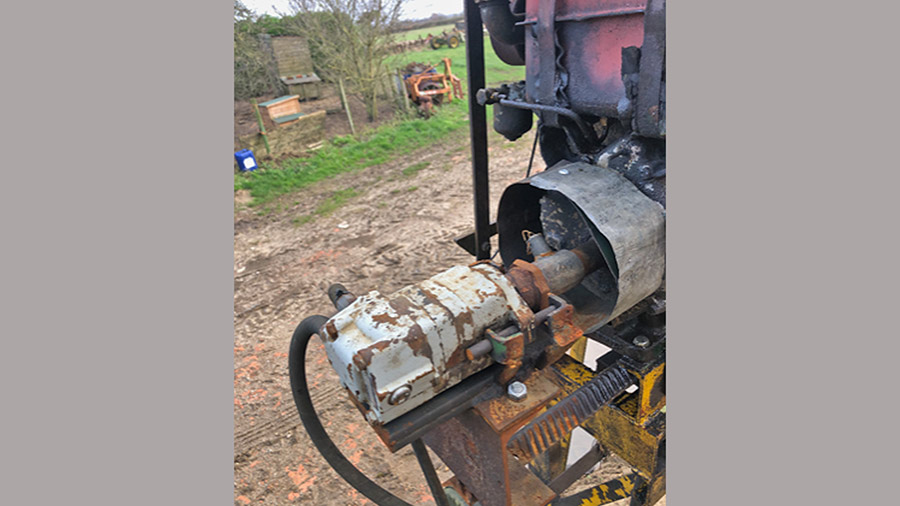
© Peter Richardson
Finding his engine driven beet loader tough to start by hand when cold, Peter Richardson rigged up a small hydraulic motor connected to the tractor hydraulics to spin it over.
The motor is mounted on a sliding bracket, allowing it to be pushed onto the starting handle shaft when the contact is up. He then pulls the spool in the tractor, the motor turns and the engine sparks into life.
Handily, the engine vibrations cause the motor to slide back along its mountings, disengaging it automatically.