Inventions Competition 2024: Slurry separator bags top prize
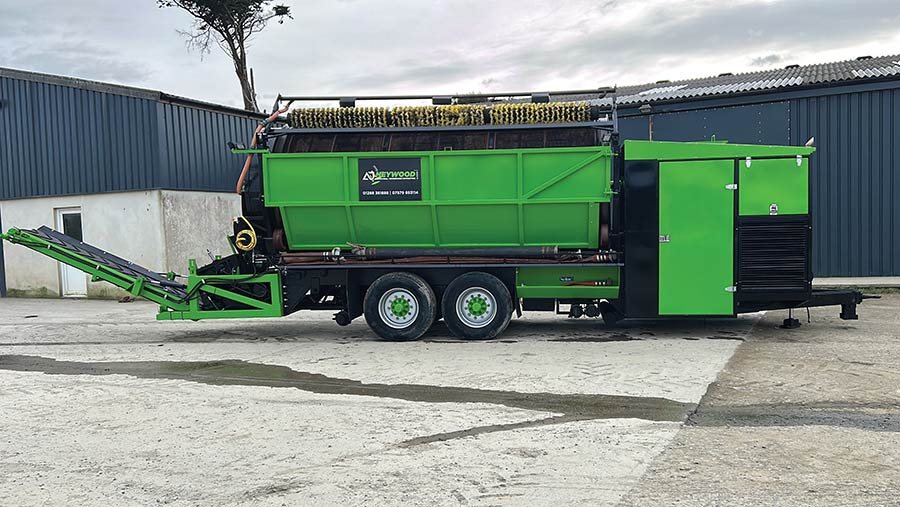
This year’s complex category winner is a self-powered slurry separator built over two years by Alan Gilkes for Cornish contractor AJ Heywood.
The machine was designed to split the liquid and fibrous elements of dairy waste, no matter whether cows are bedded on sand, straw or sawdust.
In doing so, farmers no longer have to apply thick slurry through a dribble bar, significantly reducing the risk of it sitting on top of the grass sward and contaminating subsequent silage crops.
See also: Thompson Brothers’ bespoke umbilical slurry pumping trailer
The starting point was a redundant soil screener, sourced for just £4,500. After chopping the chassis to put in a stepped frame, and rejigging the axle configuration, Alan set to work on the separation system.
This is driven by the screener’s original six-cylinder, 130hp Iveco engine that, fortunately, was in good working order. It runs four hydraulic pumps, three of which were already on the donor machine.
The fourth was salvaged from an old JCB TM telehandler.
These run the major powered units – the main pump that discharges the dirty water, the drum, a roller press and the auxiliary rams.
In work, slurry from a lagoon, reception pit or tower is pumped into the centre of the separator.
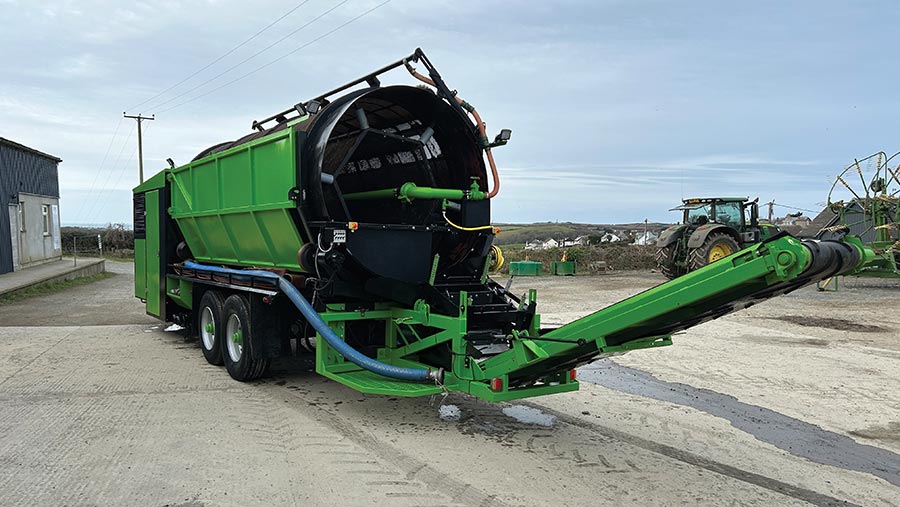
© Alan Gilkes
The twin-mesh drum turns slowly, corkscrewing the slurry in similar fashion to a cement mixer.
A hydraulic ram at the front allows the operator to alter its pitch, and, therefore, how quickly the fibrous material is moved through the cylinder.
As it rotates, the nitrogen-rich liquid drops into a sump bath below. This is then pumped back to a store, sometimes via a settlement trailer that allows any sand to fall out of suspension so that it can be removed.
Some of the liquid fraction can also be recirculated to a pair of brush-type wash bars – one internal, the second external – that keep the mesh clean.
The solids are churned out the back of the drum, where they drop into a double roller press that squeezes out the last of the juice.
The resulting material, which has a dry matter of 25-30%, is then jettisoned from a 4m elevator at the back.
At about 100cu m/hour, output isn’t quite high enough to keep an umbilical system fed, but it could potentially be rigged up to work with a nurse tank and tanker.
Total cost was about £45,000, most of which was labour, and it has so far processed about 800,000gal of slurry.