Winning Inventions Comp entry up for grabs in farm sale
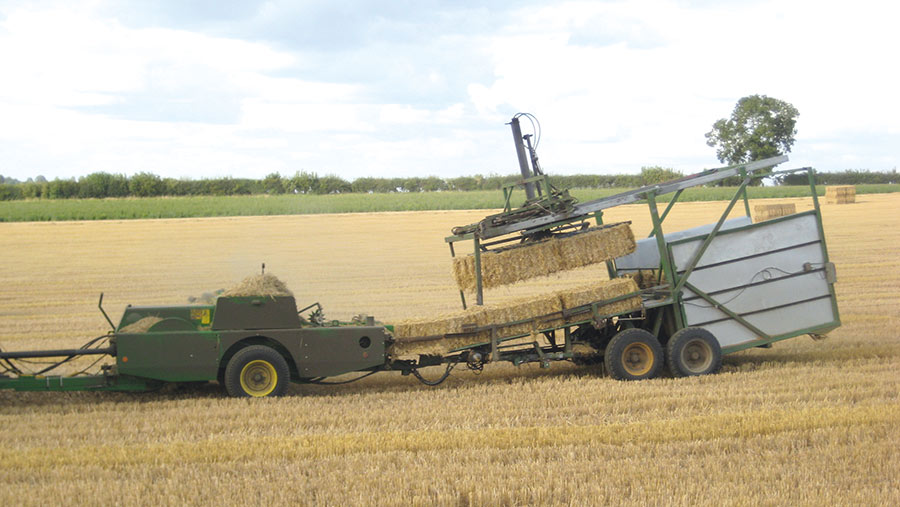
After 53 years, several million small square bales and dozens of farm inventions, Cotswolds contractor and farm-scale engineer Frank Henderson is calling time on his career – and his bespoke fleet of hay and straw machinery is up for grabs.
That includes the winning entry in the 1993 Farmers Weekly Inventions Competition, which will be sold as part of the dispersal hosted by auctioneer Taylor and Fletcher at Oathill Farm, Enstone, Oxfordshire on 23 March.
See also: Seasoned inventor reveals his niftiest farm creations
The first 40-bale accumulator was assembled in 1980 and transformed the efficiency of his small bale business.
He has since built two others, one of which continues to ply its trade in the UK. The other was shipped to Australia.
“We were originally loading flat eights onto trailers and then stacking them in the barn. But I decided it would be far quicker to come up with a machine that could be hooked on the back of the baler to form blocks of 40.
“It eliminated double handling and really cut back the cost of production by running what is essentially a big bale system for small bales,” he says.
How does it work?
The accumulator attaches to the back of the small square baler via a drawbar made from Volvo lorry chassis steel.
The mounting point is midway between the axles of the two implements, which Mr Henderson says gives true articulation.
“This means it tracks accurately, is easier to tow on the road and will go through any gateway that the baler is able to because it’s 6in narrower. Plus, it is half the weight of a modern Bale Baron.”
It originally ran on a single axle, but Mr Henderson decided to fit a second stub and wheel on the feed-in side to smooth the journey over tramline ruts.
In a decent crop, two bales are pumped out every 15 seconds. These are pushed along a tin-lined transfer channel with sprung side guards that come under tension to prevent bales jamming on sweeping bends.
As each one nears the back of the channel it triggers a steel bar to push against its flank, shunting it sideways onto the main bed of the accumulator.
Once the eighth and final bale of the set is shoved into position the whole lot nudges a second trigger – this one on the far side of the bed – that initiates the next phase of the loading process.
This sees the grab slide down its box-section mast, pressing against the bales with adequate force (roughly 400psi) for the tines to bite in.
With that, the flat eight is lifted and the grab rolls along recycled sliding door runners to a position above the stacking cradle at the back.
It then lowers, releases the bales, and returns to its original position above the accumulator bed.
The process takes 38 seconds for the first, third and fifth layers. However, the even-numbered layers take a further 10 seconds because, rather neatly, the grab turns through 90deg so that they’re oriented perpendicularly to the bales above and below to a more rigid stack.
Once a five-layer stack is complete, the whole lot is ejected on the move, with the bed pivoting down and a kicker plate pushing against the base layer.
How is it controlled?
The accumulator has eight separate hydraulic functions, which are plumbed into a Cetop valve block fed by a single tractor spool set to constant pumping.
“The beauty of a closed-centre hydraulic system is that the oil doesn’t flow until it is needed – when a bale hits the trigger, to push the grab or to eject the stack – so it doesn’t get hot and the pump doesn’t have to work too hard.”
Better still, every part of the process is automated, except for the stack discharge system.
This relies on the sort of simple, timer-based chip that is used to operate a car’s intermittent window wiper, combined with new components from Radio Spares.
It counts the layers in the stacking bed, automatically rotates the grab and doesn’t attempt to put another layer on board if there are already 40 bales in the stack.
“It might be yesterday’s technology, but it’s unbelievably reliable and still works perfectly after 40 years and over two million bales.”
No surprise, then, that several companies were keen to put the design into production in the early 1980s, including Walter Wilder, Browns of Leighton Buzzard, and Vicon.
“The stumbling block was that I wanted it to be as strong and reliable as possible – and those companies wanted to be able to sell spare parts. That made our objectives incompatible.”
What else is up for grabs?
One of Mr Henderson’s first major projects was a bale squeeze that is still going strong after 40 years’ service.
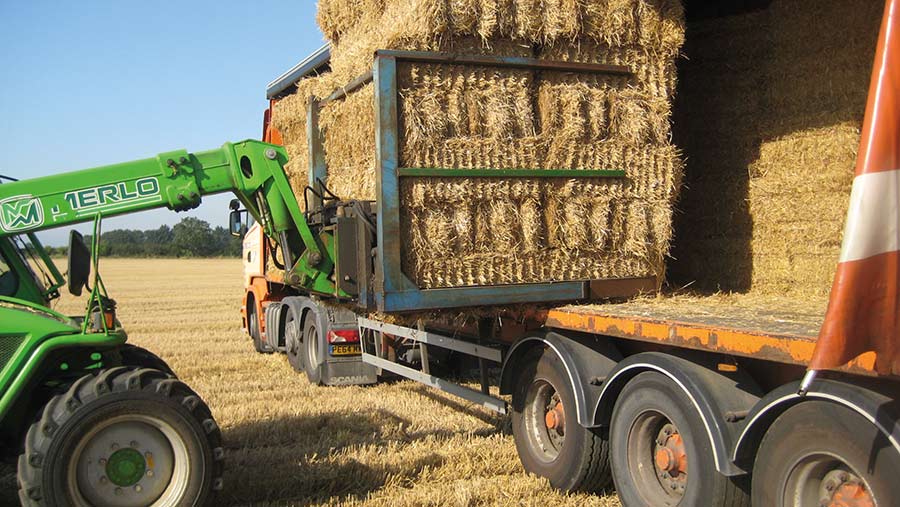
© MAG/Oliver Mark
It was originally designed to run on a Matbro Mastiff Minor, and later on a Bray loading shovel, before the introduction of telehandlers revolutionised bale collection and stacking.
“The squeeze meant I could pick up 64 bales at a time and load a whole trailer eight high in 15 minutes, which was no slower than dealing with big bales.”
It weighs 500kg and uses two rams, with a 15in stroke on each, to grab the bales with 10mm-thick arms braced on the corners with forklift tines.
Mr Henderson had better luck getting it into production, thanks to a tie-up with Cherry Products.
“Graham Cherry started his business in our yard in 1981 and the squeeze was the company’s main product in the early days – until small bales went out of fashion.”
“The company is still based here, albeit transformed from a one-man band into one that turns over £6m-a-year and exports all over the world.”
Rake and turner
First built in 1985, the three-wheeled side-delivery rake is based on a Lely-Vicon Acrobat – or three of them, to be precise.
It has 11 upright, air-suspended finger wheels that rotate in contact with the crop and pass it from one wheel to the next.
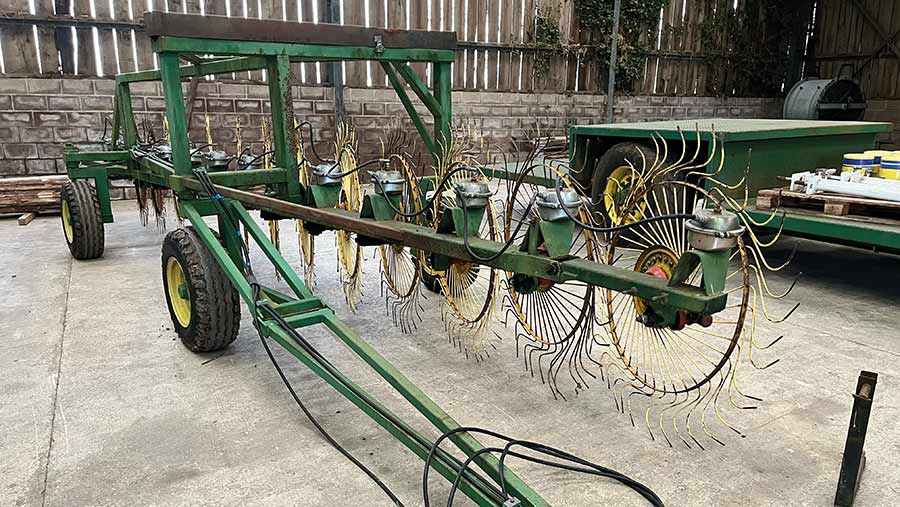
© MAG/Oliver Mark
“I liked the design of the Acrobat. It offered the potential for high output, was relatively cheap, and the lack of pto driveshafts, gearboxes and tine-lifting cam mechanisms means it is very simple and lasts far longer.
“The other advantage is that I can make as many passes as are required to get a good-sized swath – particularly in second-cut hay.”
It has a maximum working width of 18ft but can also be narrowed, which Mr Henderson says is ideal for flicking a row of straw upside down.
Suspension of the tine wheels is provided by an air system made from commercial vehicle spares.
The box section chassis forms the air tank and, pumped up to 1bar, will maintain its supply for several days. This takes 90% of the weight of each tine wheel to avoid picking up and mixing too much debris with the crop.
Also up for sale is a similar 13-wheel turner (pictured) designed to lift and move hay gently across a 21ft width.
Bale trailers
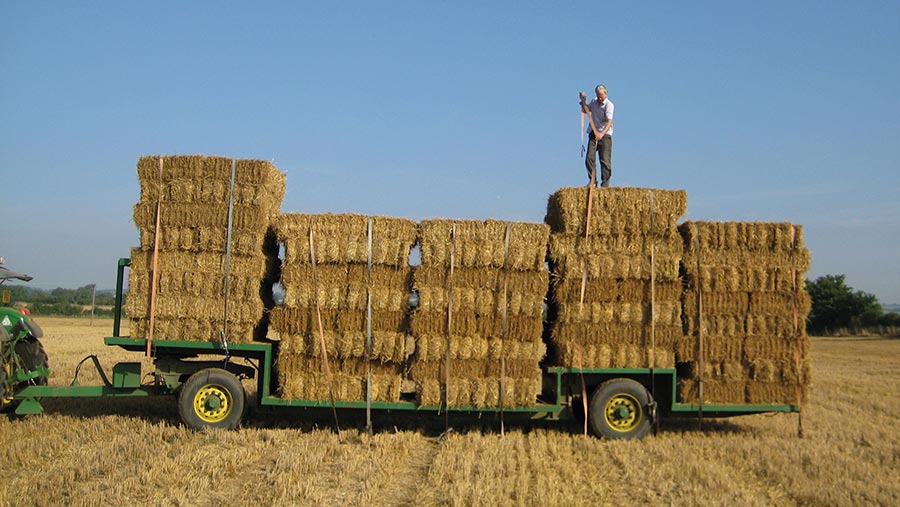
© MAG/Oliver Mark
Mr Henderson built his own 36ft step-frame trailers, designed to carry five stacks of up to 64 small squares that are ratchet-strapped into place.
The stand-out feature is the position of the fifth wheel pivot, which is 2ft 6in (75cm) from the front of the trailer and the same distance ahead of the axle.
This means the towing tractor should be able to turn in a 40ft space.
John Deere 459 baler
Mr Henderson’s 39th, and last, John Deere small square baler is a now three-year-old 459. And over his five decades of baling, he’s worked out how to tweak each one for maximum reliability.
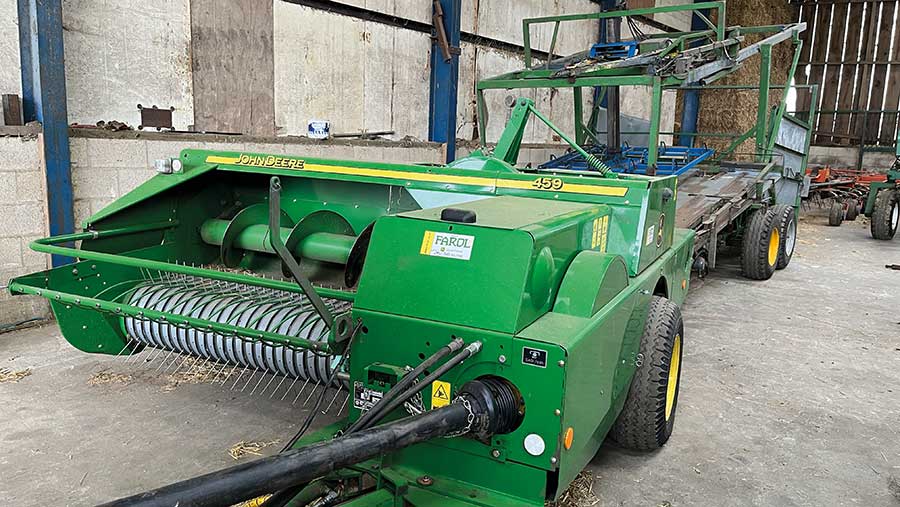
© MAG/Oliver Mark
“I used to replace the baler annually as it only cost £3,000 a year to change, which was easy to factor in as a fixed expense spread over 70,000 bales – at least when it was relatively easy to make decent money on straw.”
“But I’ve always had to adapt them to get them working reliably. I fit an air tank to blow the knotters off, strengthen the drawbar to make sure it can handle the accumulator hooked on the back, and weld a block next to the gearbox to stop it moving. I also tend to tweak the string box so that it fits eight balls inside.
“The 459 produces the tidiest package of all the balers I’ve had – if you put a level feed in, you’ll get level bales out.”
Other kit
- 2012 John Deere 6430 Premium AutoPowr, 3,460 hours
- 2004 Merlo P35-7 Turbofarmer telehandler, 5,350 hours
- 2007 Warwick 18t trailer, hydraulic tailgate, air brakes
- 2002 refurbished Vaderstad Rapid System Disc 4m 400F drill
- Amazone ZA-X Perfect 1402 fertiliser spreader