How to get the best from a McConnel hedgecutter
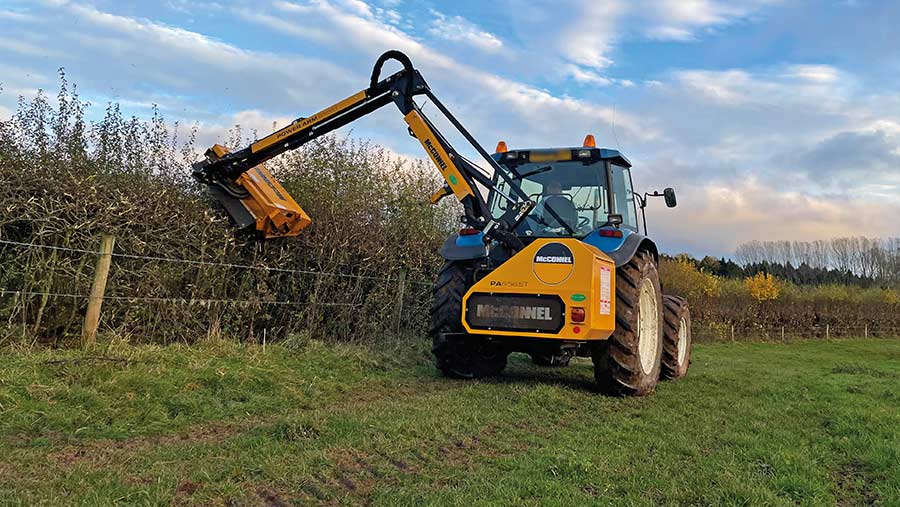
Since the launch of its first Power Arm trimmer in the early 1950s, McConnel has been a dominant force in the world of flail hedgecutting.
From a starting point of just one rear-mounted machine, the Shropshire firm’s product line-up has ballooned to the point that it now offers more than 40 models split across 12 ranges.
See also:Â Buyers guide to 6m-reach hedgecutters
Of these, the PA6565T is its biggest seller. Offering 6.5m of reach (1m of which is telescopic) and a 65hp hydraulic motor, this versatile model is small enough to mount on an 80hp tractor, yet powerful enough to carry out serious contracting duties.
Standard features include hydraulic power slew, a hydraulic auto-reset system and soft-start rotor engagement.
A comprehensive list of options also means it can be configured to suit many tastes and budgets.
The PA6565T forms part of the firm’s five-model 65-series, all of which feature 65hp motors and the same basic components.
The only difference is the length of the arms and presence of a telescopic function.
These might seem like simple machines, but with an on-board hydraulic system, clever articulating arm and a fast-spinning flail, there’s plenty for operators to keep their eyes on.
Those who scrimp on the maintenance, or knock them about, will soon find themselves on the phone to the local dealer.
To help us point out the key pitfalls, we enlisted the help of long-serving McConnel dealer Frank Alviti.
He’s been selling, servicing and repairing the brand’s hedgecutters for more than 20 years and knows them inside out.
Frank Alviti
Frank Alviti is based less than three miles from McConnel’s factory in Ludlow, Shropshire, and has been a dealer for the brand for more than 20 years.
He runs the business with his son, Dave, and as well as selling new machines, they offer a wide range of services to support those running second-hand models.
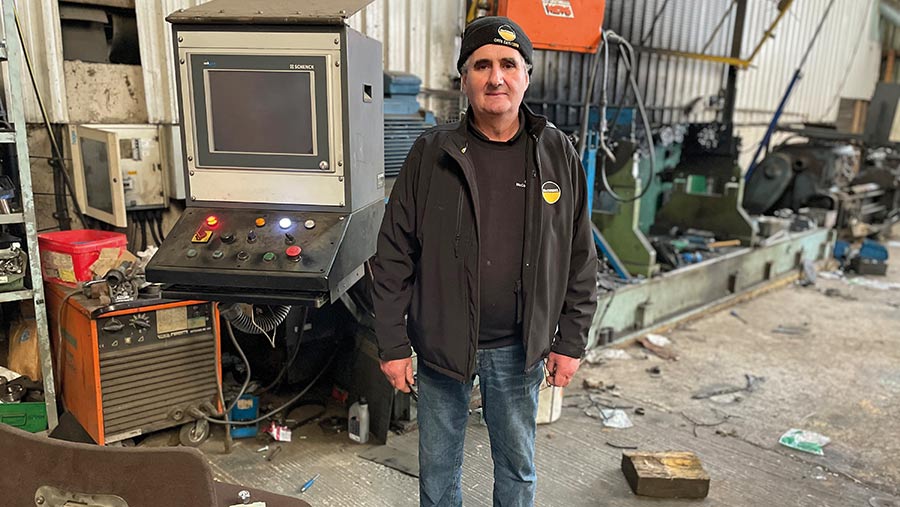
Frank Alviti © James Andrews
These include routine maintenance, repairs and parts supply, through to more specialist jobs such as rotor balancing and rebuilding damaged machines.
They also run a fleet of hire machinery from tractor-mounted toppers and cultivators to Robocut mowers, stump grinders and access platforms.
We’re using a PA6565T as our example machine, but as most McConnel trimmers have the same basic configuration, these tips can be applied to almost any model and range.
Wiring
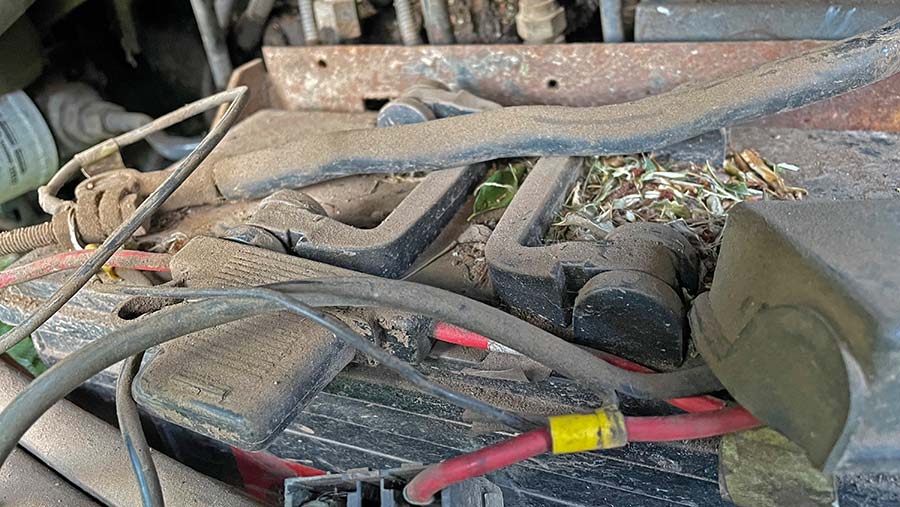
© James Andrews
The first order of business is to make sure the machine is wired up properly. This involves connecting wiring looms for the controls and oil cooler directly to the battery or starter motor.
Some people try running them off the tractor’s three-pin socket, which will cause the plug to overheat and runs the risk of blowing fuses.
Gearboxes
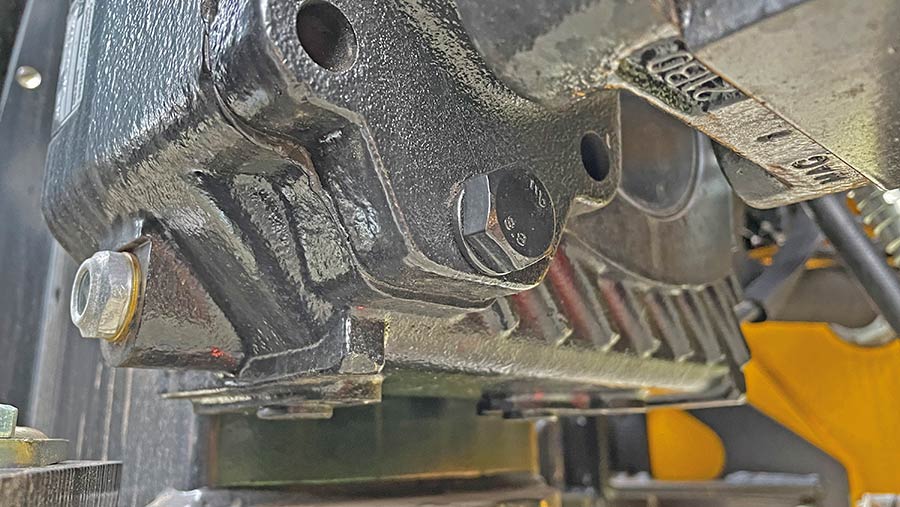
© James Andrews
Well-maintained gearboxes can last for thousands of hours, but if the oil isn’t changed regularly – after the first 50 hours and every 250 hours thereafter – they can fail prematurely.
Newer machines are fitted with Coma units that run on 75/90 fully synthetic oil, while older versions have Bima boxes running on 80/90 mineral oil.
If the gearbox does start to make a noise, it’s important to stop and investigate. Dirty graphite-coloured oil means the bearings are on their way out and, if you’re lucky, these can be replaced.
However, sometimes the gearbox will be too far gone and a new unit will be required. Prices for these range from £1,200- £1,300.
It’s a bad idea to run a noisy gearbox until it packs up, as it can chew the shaft off the hydraulic pump. This blunder will add a new pump to your shopping list.
Gearbox ratios and overheating
McConnel has recently switched to fitting 760rpm gearboxes from the factory, but older versions had 540rpm gearing, unless the buyer specified otherwise.
The problem with 540rpm gearboxes is that some operators are tempted to run the tractor in the 1000 or 1000E pto setting to reduce engine revs.
This does help lower fuel use, but it can cause problems with the emissions systems on some modern tractors.
There is also a temptation to increase revs when manoeuvring, which runs the risk of overheating the trimmer’s oil.
If operators do this, it can cause hardening of the O-rings in the valve block and pop the ends off hydraulic pipes.
Buyers do have the option of retrofitting 760rpm gearboxes to existing machines.
Pump
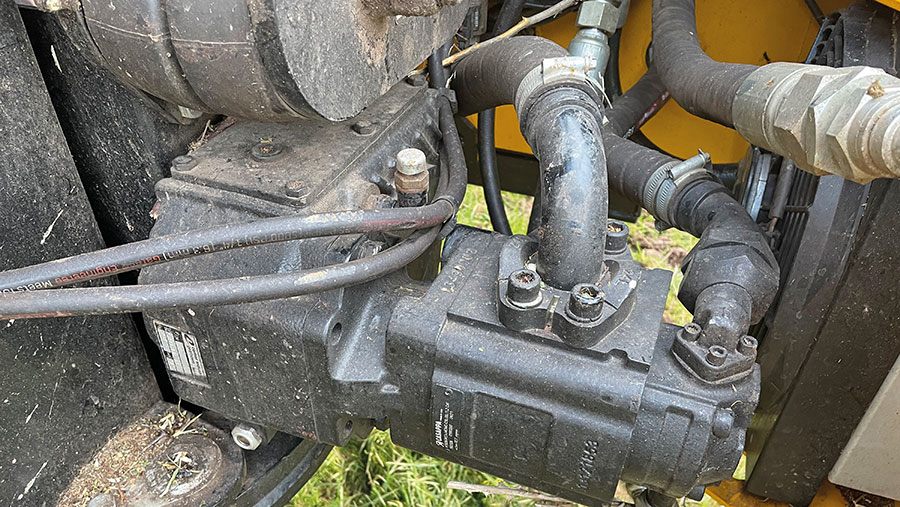
© James Andrews
Pumps will be either Casappa or Parker and both are reliable, providing the machine is properly run and maintained.
Problems arise when the oil is allowed to overheat, which can damage seals, or if a dying gearbox breaks the driveshaft. Replacement pumps cost £1,000-£1,500.
It’s also important to change the hydraulic oil filter every 500 hours to prolong the life of the pump and motor.
Hydraulic pipes
When replacing damaged or leaking hydraulic pipes, it’s crucial to use hoses that are rated to the correct pressure – otherwise there is a serious risk of premature failure.
The bare minimum for 1in pipes on 65hp machines is 3,200psi, with 85hp models needing in excess of 4,400psi. For a belt-and-braces approach, go for the highest-rated pipe you can get hold of.
Oil cooler
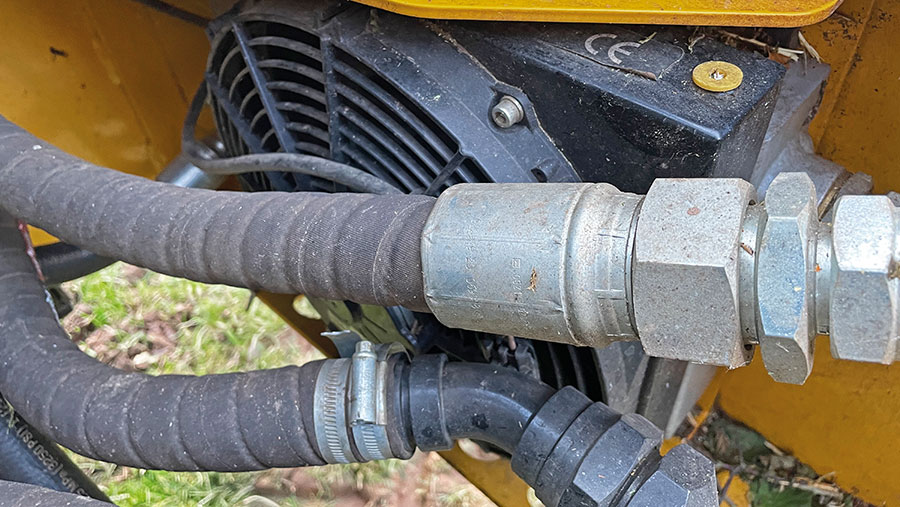
© James Andrews
The oil cooler is crucial for keeping the trimmer running smoothly and avoiding unnecessary stress on components.
Blow the radiator matrix out periodically, particularly if working in dusty environments, and check that the electric fan kicks in as it starts to get hot.
If maintenance is neglected, the oil will overheat, possibly damaging seals and triggering the thermal cut-out.
Auto-reset system
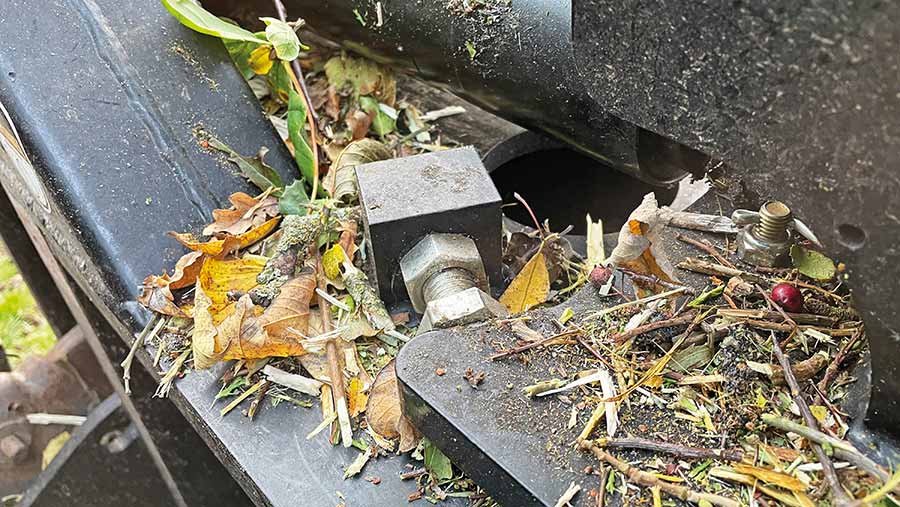
© James Andrews
Auto-reset is a function that allows the arm to break back if it hits a solid object and then automatically return to its working position.
When engaged, the arm will be held tight against the stops by using pressure from the lift ram.
If the system isn’t turned on during work, the arm will float around, making it hard to do a tidy job and accelerating wear on the arm bushes.
It’s also worth noting that pressing the auto-reset button will cause the arm to move, even if the pto isn’t engaged.
This runs the risk of whacking the head into the tractor or colliding with other objects – it has been done. For added security on the road, make sure the locking pin is fitted.
Pins and bushes
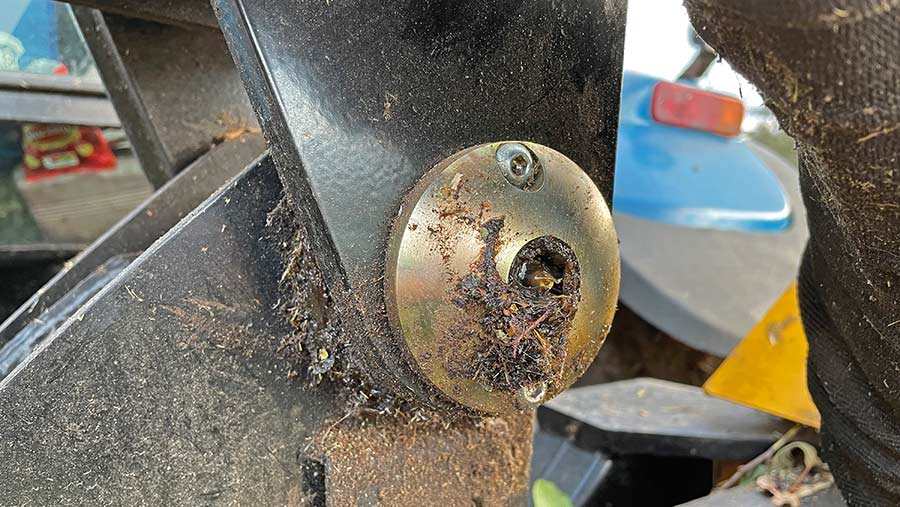
© James Andrews
Arm bushes are put under a lot of strain, so they need a shot of grease every day. Even with regular maintenance, they will wear over time, and it’s a good idea to replace them before they damage the pins.
This is a quick, simple job and, at less than £10 a pop, they’re considerably cheaper than replacement pins.
Replacing flails
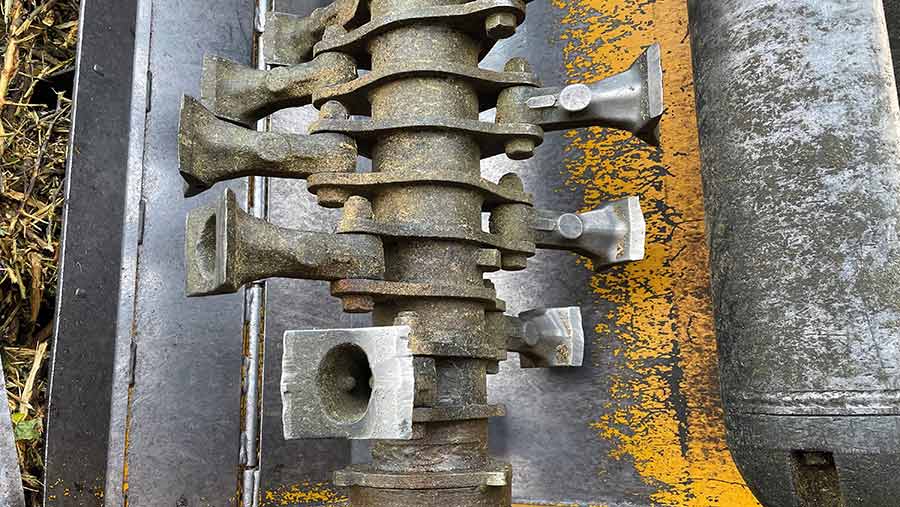
© James Andrews
If a flail becomes damaged and needs to be replaced, change its opposite number at the same time.
If this isn’t done, the rotor will be out of balance, causing vibrations that can rattle bolts loose and lead to cracking in the head.
Bushes are another thing to watch out for – these are specific to the flail type and, if the wrong versions are used, flails will rattle from side to side, causing unnecessary wear.
Flail type
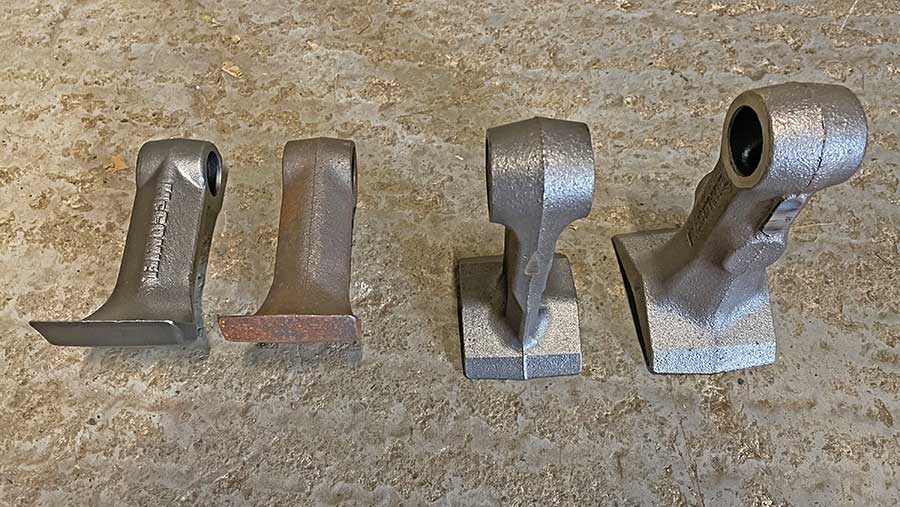
© James Andrews
There’s a wide range of flails on offer, but the most common fitments in the UK are T-shaped F10s and F14s, as well as the single-bladed F10 Competition units.
F10s are the standard option, offering decent performance in most conditions for a reasonable price. F14s have a similar shape, but are heavier, giving extra momentum for knocking down multiple years of growth.
Additional strength also helps them withstand harsher operating conditions.
F10 Competition flails are becoming more popular, as they give the tidiest finish and are less liable to hook grass when cutting verges.
The long leading edge also means they can be sharpened more times before needing to be replaced.
T-shaped flails can be reversed to extend the lifespan, but by the time one side has worn down they’re rarely in good enough shape to warrant this.
Prices start at about £6.50 apiece for F10 and F10 Competition flails, with F14s coming in at £9.50.
A 1.2m head holds 24 flails, a 1.5m has 28 and there are 32 on a 1.6m.
Rotor balancing
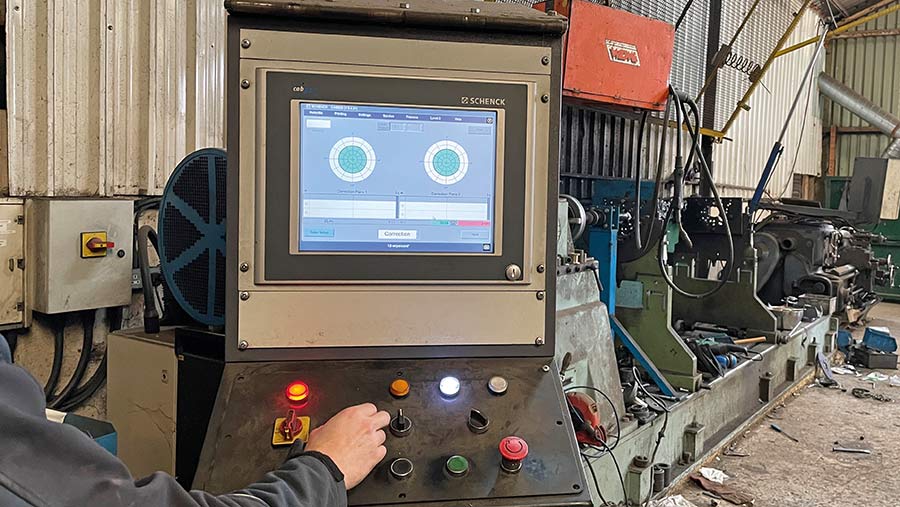
© James Andrews
Over time, rotors will go out of balance, either by whacking into something solid, or as a result of uneven wear.
The only way to get it running sweet again is to have it professionally balanced; several firms offer this service in the UK, including Frank Alviti.
The process involves loading the complete rotor into a balancing machine, which spins it at the correct operating rpm.
This is generally carried out with a fresh set of flails, bolts and bushes fitted, to avoid balancing out imperfections in worn parts.
Any damaged lugs, or those with oval holes (caused by running the rotor with loose flail bolts) are also replaced before the process starts.
Once the rotor is up to speed, the computer system picks up any imbalances and shows where weights need to be welded on to get it running true again.
Prices for a simple balance start at about £250, but vary according to the amount of additional work involved.
Rotor bearings
Rotor bearings take some stick and, ideally, they need a few shots of grease twice a day.
Even with regular maintenance they will eventually need replacing, but a lack of maintenance brings that day around much sooner.
The first indicator that they’re on the way out is a smell of burned grease, but the longer they’re left, the more obvious it will become.
Replacement bearings cost £50 each and they’re straightforward to fit.
However, it’s essential to shim them up properly before the machine is put back to work. Dealers can tell you how to do this.
Motors
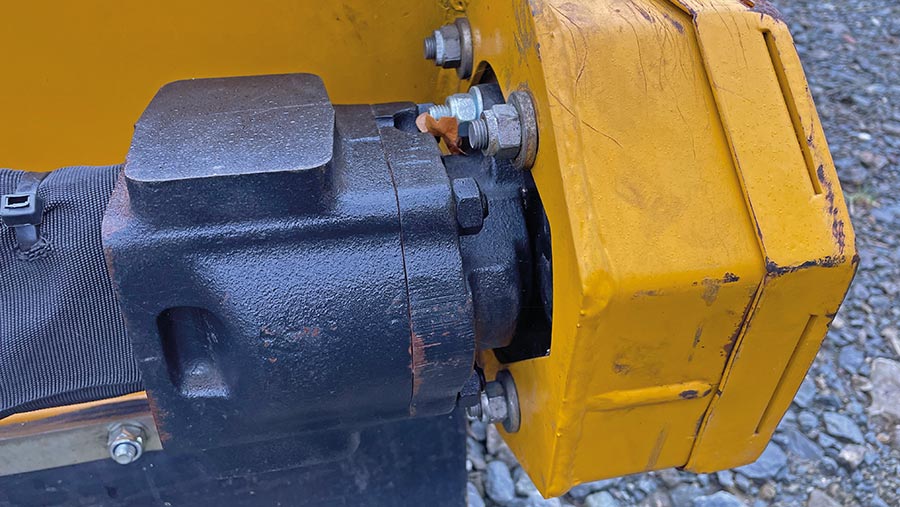
© James Andrews
Head motors are either direct-mounted, meaning the output shaft attaches to the rotor, or belt-driven.
The benefit of the latter arrangement is that the motor is neatly positioned at the rear of the head, rather than hanging off the side. It’s a desirable option, particularly for verge mowing contractors that need to get close to obstacles.
Debris blowers
Unlike larger machines that have an integrated debris blower, 65-series models have one that mounts externally to the rear cover.
This is powered from one of the tractor’s spools and it needs to be plumbed into a free-flow return. Oil flow also needs to be turned down so the fan doesn’t over-rev.
The setup performs just as well as the integrated units, but it isn’t as neat and it’s more at risk of getting clobbered when reversing.
Many people who want a blower will upgrade to the larger 70-series.
Hood flaps
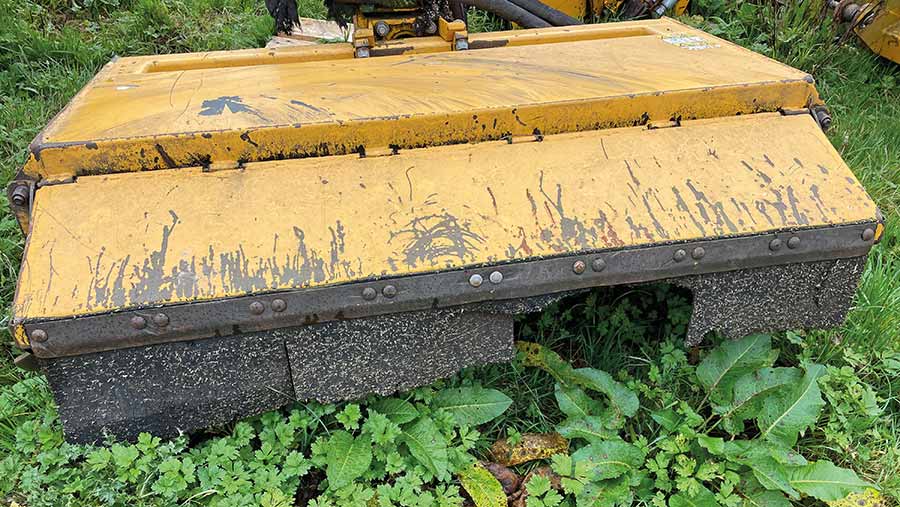
© James Andrews
A toothy set of head flaps will allow material to fly out, which is particularly undesirable when cutting roadsides.
Replacements are available in a standard form or heavy-duty, with steel reinforcing bands bolted on the bottom.
These are more durable and flex less, holding more of the material in the head. Prices for a set of heavy-duty flaps start at about £200 for a 1.2m head.
Mounting options
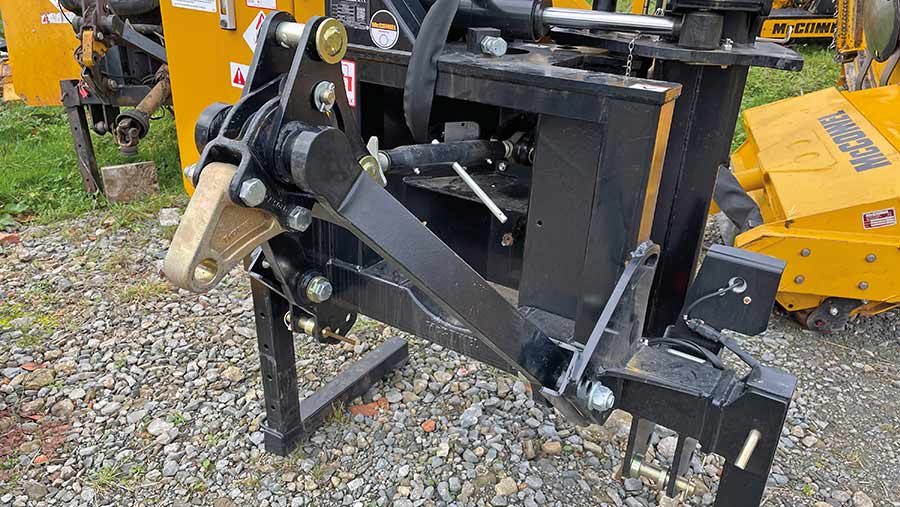
© James Andrews
Buyers have three mounting options, all of which are interchangeable on the 65-series. This means second-hand machines can easily be adapted.
The simplest option is three-point linkage mounting, which offers quick and simple hitching at the expense of stability.
Upgrading to a five-point sub-frame makes the outfit far more solid, and once operators have used these they rarely want to go back.
The final option is McConnel’s recently introduced four-point system. This uses the three-point linkage, but comes with an additional brace that attaches to the pickup hitch.
Those buying a machine with three-point linkage can have a five-point sub-frame fitted for £1,500-£1,800 plus tractor fittings, with prices varying according to how awkward the host vehicle is. Prices for four-point braces range from £550-£650.
Head options
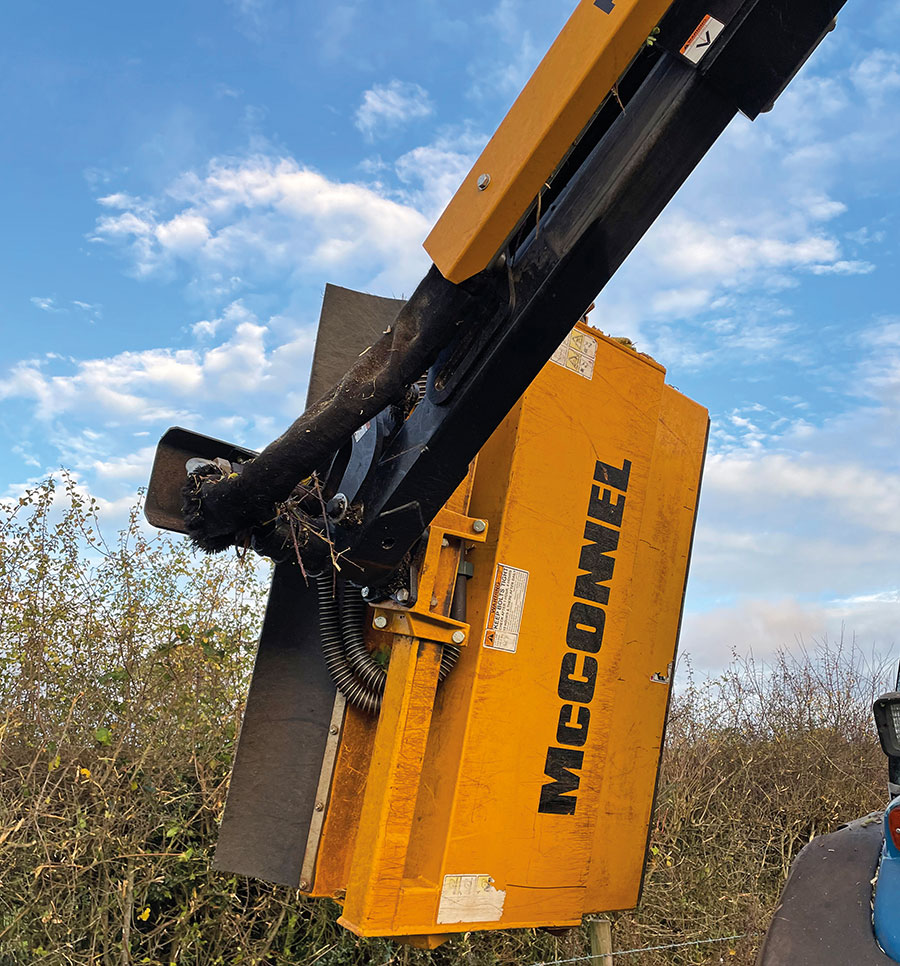
© James Andrews
The standard head for a 65-series machine measures 1.2m, but there is growing demand for 1.5m versions that offer a noticeable increase in cutting area. Some operators go for the largest 1.6m variant, too.
Orbiter heads are also getting more popular. These give added articulation so the head can tuck in the same width as the tractor when cutting vertically.
Many are specced from new, but it is possible to retrofit them to an existing machine.
Prices start at about £1,400 for a simple setup that’s plumbed into one of the tractor’s spool valves. However, a slicker approach is to hook it up to the trimmer’s hydraulic supply and run it through the electronic controller, which sees prices rise to about £1,600.
Additional options include a hydraulic hood that allows the front of the head to be opened for taking a larger bite of long growth, and hydraulic rollers for better control when verge mowing.
Controls
The most common control unit on 65-series trimmers is the Motion armrest, which comes with a small joystick controller and a bank of buttons for additional functions.
Buyers have a couple of upgrade options, such as the Evolution with larger multifunction joystick that’s more comfortable to use.
The top-spec Revolution control system adds a screen for displaying information such as power reserve and hours worked.
More importantly, it gives access to the firm’s EDS system, which automatically adjusts the head to follow ground contours when verge mowing.
Second-hand market
The second-hand market is strong for trimmers of this size, and good examples rarely hang around for long.
Early PA6565T models in tidy condition (around 2013) will sell for £13,000-£15,000, but there will be some variation according to the number of options included and the type of flail fitted.
New ones cost £21,000-£24,000, so there are some decent savings to be made if you can drop on a good example.
When shopping for a machine privately, it’s worth paying close attention to the pointers in this article.
However, a simple visual inspection usually gives a good indication of what state it’s in – if it looks rough on the outside, it’s usually the same story inside.
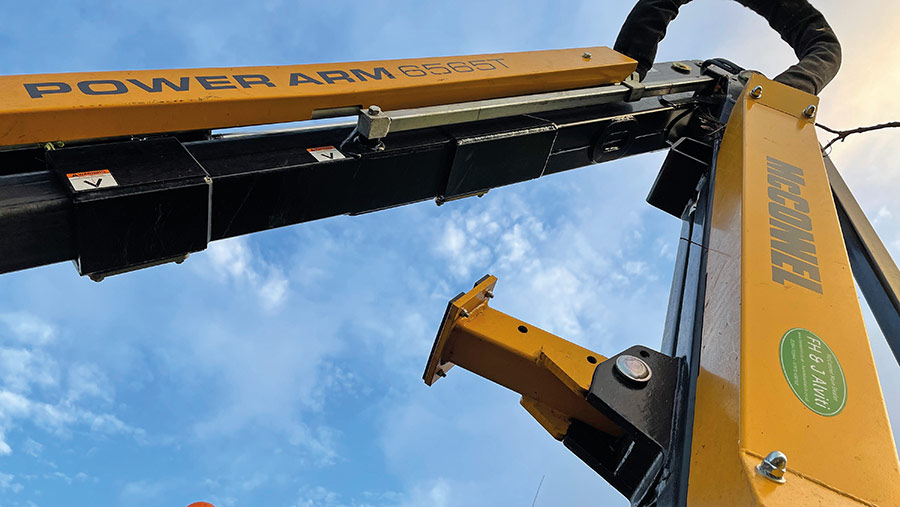
© James Andrews
If considering a battle-scarred model, it’s worth carrying out a more detailed inspection and taking the time to weigh up the cost of replacement parts.
Some operators have been known to bend arms, which cost about £2,000/section. For a simple alignment test, fold the machine up and check that the beam sits centrally on its rest.
McConnel 65-series specs |
||
65-series |
Reach |
Power |
PA5565 |
5.5m |
65hp |
PA6065 |
6m |
65hp |
PA6565T |
6.5m (including 1m tele) |
65hp |
PA7065T |
7m (including 1m tele) |
65hp |
McConnel numbering explained
Most recent McConnel Power Arm hedgecutters use the same numbering system, with the first two digits denoting the reach of the arm and the second two representing the horsepower.
The addition of a T on the end means the reach figure includes 1m of telescopic adjustment, and those with VFR in the title have an arm with variable forward reach.
Each series of machine is categorised according to the horsepower, so all 65-series machines will have a 65hp motor and all 70-series are 70hp.