11 ways to make your slurry pump last longer
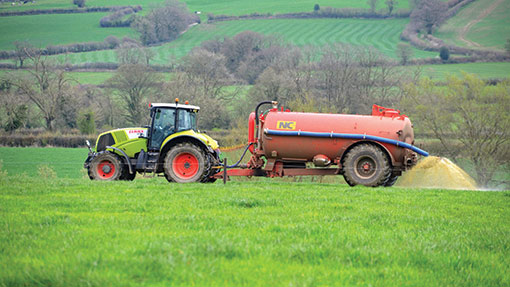
There’s a serious knack to sorting out any farm’s slurry set-up and it’s generally assumed that once it’s up and running, it’s best left alone.
All those pipes, valves, pumps, jetters, impellers, agitators and controllers are enough to send any normal mind back to the kitchen for more coffee.
Central to any system is the pump – and with a bit of gentle maintenance it can be coaxed to go on longer than its creator might ever have imagined.
Whether it’s a vacuum pump on a tanker, a pto-powered lagoon pump or a rotor-stator pump for a dirty-water irrigator, spending years immersed in some of the most aggressive liquids known to man means they all can benefit from a bit of TLC.
Lagoon pumps
Immersed-impeller pumps suffer some of the toughest lives of any farm implements, whether driven by electric motor or hitched up to the tractor.
Most use a slurry-lubricated rubber bearing at the base of the shaft submersed in the lagoon or reception pit. Over time this inevitably wears and needs replacing. Telltale vibrations and knocking will suggest it’s gone.
1. On this NC lagoon pump it’s a case of digging the old corrugated rubber bearing out of the housing just above the impeller cowling and sliding the new wrap-around piece back in. It costs about £20.
2. Up at the top end, oil levels will need checking in the 90deg gearbox – either a dipstick or level plug.
3. There will also be some sort of self-aligning bearing and UJs on back-to-back yokes that will need greasing. Waggle the shaft back and forth to check for play.
With a ring of corrosive water constantly sitting around the shaft, bearings often suffer – this one’s lost its seals and balls. Replacing it will mean lifting the pump out and dropping the impeller shaft off the bottom of the gearbox.
With it out of the muck, it’s also worth checking the roll-pin that secures the impeller to the bottom of the shaft.
If this snaps and it is allowed to spin for a long time, both the impeller bushing and the main shaft will be scarred.
A simple but officially frowned-upon solution is to tack-weld it to the shaft – no problem if overload protection is provided by a shear-bolt on the gearbox input shaft.
Dirty water pumps
Dirty water systems all vary in the way they’re put together but at their core is often a rotor-stator pump. Effectively a screw rotating in a helically profiled rubber sleeve, it draws liquid in from the motor end and pressurises it, propelling out the end of the rotor into the pipework.
Generally maintenance-free, over time both rotor and rubber stator sleeve wear out and need replacing, especially if there’s sand in the slurry (a dealer job).
If this is the case, the first noticeable thing will be that the irrigator it feeds won’t be functioning properly. If it’s a Briggs RotoRainer it won’t spin as fast as it should and liquid will just drizzle out of the nozzles as the pump struggles to maintain pressure.
4. If coupled up to a jet-gun such as NC’s Pulse-Jetter, it will take a lot longer to build up to the pressure that triggers it to blow-off.
Most commonly it’s not actually the pump that is at fault, but leaky pipes, joints and valves that let the side down. However, if there’s grinding coming from the stator sleeve then it’s likely to be scored.
If not, it may just be that air is being drawn in where the gland at the motor end has got slack over time – there will be a sucking noise if this is the case. Expect to see a few drops of liquid around the gland – it provides lubrication – however, tweak it up until it drips at a rate of about two drops a minute.
5. Somewhere in the pumpset pipework there should be a check valve and flow filter. These need cleaning out from time-to-time and the system needs back-flushing daily to clear any strainers and gauze filters.
A submerged filter basket on the inlet line is an absolute must to keep unwanted solids from entering the system. This will need occasional clearing but is the best way of extending any pump’s lifespan.
Clearly the irrigator itself will need a bit of attention – RotoRainers have greasers while Pulse-Jetters have a tube of oil that acts as a reservoir to feed the blow-off piston that needs topping up.
Tanker pumps
The vanes in the pumps used on vacuum tankers wear out over time but are generally a relatively straightfoward fix.
If it takes a long time to build a vacuum then typically the vanes aren’t working correctly. Often over-oiling is the cause, gunging up the slots in the rotor so that the vanes can’t slide in and out freely under centrifugal force.
6. Either way, a pump strip-down is required – but this needn’t be a bench job. With the pto shaft off and three of the mounting bolts removed, the pump can be rotated on the drawbar to allow access to the backplate. With this exposed, unscrew the ring of allen-studs to remove it, taking care to hang on to the O-ring seal.
7. An oil pump is secured to the main shaft with three studs. Undo these and carefully withdraw the pump being wary to retain the drive key that slots into the shaft.
8. Next undo the ring of bolts securing the cast oil pump housing, and then wind two of them back into the threaded holes used to prise it off the main pump casting. This process is likely to damage the gasket.
9. Now it’s possible to access the back of the rotor and slide each of the composite vanes out of their slots. If they’re burred over on their outer edge, scored from sliding up and down in their slots or narrowed at the base then they’ll need changing. It’s worth steam cleaning to remove any oil residue, too.
Coat the new vanes with a light misting of oil and slide them back in. Refitting, in the words of the Haynes manual, “…is the reversal of removal”. However, a new gasket will be required and care is needed to align the oil pump and its drive key on the main shaft.
10. Before setting off for the next load there are two crucial jobs. Set the clear gearbox oil dropper sight-glasses to supply the correct amount of lubrication. In this case it’s one drop every four seconds.
11. Finally, open up the ball trap and steam clean to remove any gunge that might be causing the ball to stick as the tanker gets full.
While individual vanes can cost anything from £20-40 each, a full kit that includes vanes, seals and gaskets for the Battioni Pagani Mech pumps used by NC and other tanker makers will cost between £165 and £225.
Thanks to Matthew Noble of Somerset-based machinery specialist Noble Machinery for his expert advice throughout this article