Deere’s high-tech slurry system allows real-time nutrient analysis
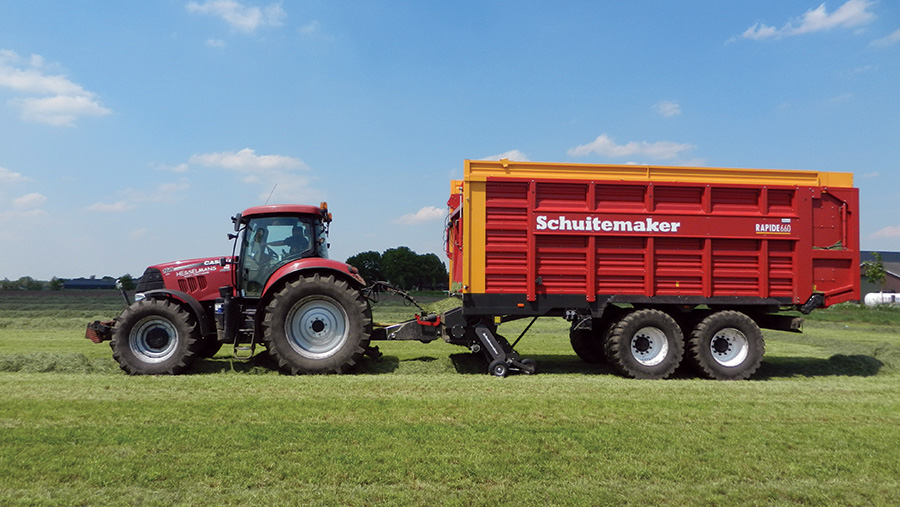
Farmers could soon be able to regulate their application of slurry and AD plant digestate according to real time nutrient analysis, thereby exploiting the value of these materials to a much finer degree than possible at present.
It is all thanks to the development of on-board near-infrared reflectance spectroscopy (NIRS) sensing and analysis technology that uses sensors mounted on slurry tankers and umbilical applicators.
See also: NIRS technology to improve manure test accuracy
Once a target application rate has been set for the primary nutrient, fluctuations in slurry analysis are then compensated by altering the forward speed of the tractor, and the whole process can be accurately documented.
Who’s doing it?
One scenario nearing commercial reality involves John Deere, as part of its FarmSight technology programme, and by Dutch slurry tanker manufacturer Veenhuis.
“Our Nutri-Flow system is at an advanced stage of development and we are now doing tests on different machines and with various kinds of manure,” says Hans Huisjes, sales manager at Veenhuis Machines.
“As part of the development, we have produced a system for adding liquid fertiliser at the boot of the injector to optimise a site-specific manure application.”
In the UK, meanwhile, three years of collaborative study sponsored by Defra through the sustainable arable Link programme and involving research and commercial organisations showed that NIRS can provide rapid, low-cost and reliable analysis of total and readily available nitrogen, phosphate, potash, sulphur and magnesium.
It will also measure slurry dry matter content above 5%.
One of the project partners, the Eurofins laboratory testing business, is licensed to use the project data and provide NIRS-based analysis of solid manures, biosolids and slurries. It is validated for cattle and pig manure and slurry, with other materials likely to be covered in future.
Comparatively rapid preparation and analysis helps keep fees down to £22 for a minimum quantity of 1kg, which Eurofins believes makes it cost-effective to submit a larger-than-usual number of samples to provide a more accurate picture of nutrient content.
Real-time analysis
As helpful as that service may be in helping to set up conventional applications, on-board sensing that provides real-time analysis goes a step further in taking account of nutrient variability on the day.
The Veenhuis NIRS system was first evaluated on a road transport tanker for online registration of slurry and digestate applications without the need for physical sampling and analysis.
But the Dutch firm, working with sensor specialist B&N Proscan, is now testing onboard analysis for a field application system by equipping a single-axle vacuum tanker with an NIRS sensor and data processing system; Isobus electronics; and GPS for application maps, process documentation and applicator section control.
A tractor-mounted front tank and feed pipes for liquid fertiliser can supplement the nutrients provided by the slurry.
Automated speed control
John Deere proposes automated speed control as part of its manure sensing system, which employs the HarvestLab NIRS unit that has been used for the past 10 years or so for onboard forage analysis.
On a slurry tanker, the system takes more than 4,000 readings a second, measuring nitrogen, phosphorous, potassium, ammonium and dry matter, with volume measured by an in-line flowmeter.
The system is controlled through a GreenStar 2630 display, which is used first of all to define the target quantity for a nutrient and also a threshold value for a second nutrient.
Predefined application maps can be uploaded if required.
During application, the NIRS sensor and manure sensing software compare actual nutrient levels with target levels.
The operator can then adjust forward speed to compensate for nutrient level fluctuations or it can be left to the Tractor Implement System (an automated system with an Isobus link between the tanker and tractor) to regulate forward speed.
Another potential benefit comes when you’re driving uphill – a tanker with variable flow-rate can maintain its output despite speed changes.
UK umbilical experience
Suffolk slurry contractor and equipment supplier Tramspread is testing the HarvestLab system with umbilical application in partnership with dealer Tuckwells.
The firm’s Terry Baker suggests that a continuous flow of umbilical application via a dribble boom or shallow injector should provide the ultimate in nutrient site-specific accuracy.
“Even with a high-capacity tanker, stopping to refill and starting again, which is not always on the headland, interrupts the flow,” he points out.
“An umbilical application is constant from start to finish.”
Data from the HarvestLab sensor is being compared with samples analysed using an Agros kit and a laboratory service to help refine calibration of the system for typical UK slurries.
It has been used with a 24m dribble bar in spring crops and on a 9m macerator dribble-bar in the autumn.
Laurence Baker, who manages Tramspread Contracting, points out that he can already supply customers with records of the nitrogen applied but using the HarvestLab with Manure Sensing provides records of N, P, K and dry matter.
“That would give more scope for customers to calculate the savings in mineral fertiliser that can be made,” he says.
“We consider it a useful add-on to our service and it’s proved user-friendly, with the extra detail available to customers making GreenStar documentation even more useful.”
Forage analysis
Onboard near-infrared reflectance spectroscopy analysis of forage constituents is already proving a valuable and reliable source of management information for growers and contractors.
The HarvestLab system, developed by John Deere and Carl Zeiss, uses a forage harvester spout-mounted sensor to determine moisture content/dry matter, protein, starch and fibre content.
In combination with yield mapping, the results can help improve crop management through site specific (rather than whole-field) measures.
It also helps producers manage livestock feeding programmes more effectively, and offers contractors simpler job recording and invoicing, as well as a value-added service.
Dutch forage wagon specialist Schuitemaker is applying similar technology to its latest Rapide grass harvesting machines.
A near-infrared reflectance spectroscopy sensor mounted in the front wall of the wagon determines the dry matter.
It then combines that with information from load cells on the drawbar and between the body and chassis (and also uses the hydraulic suspension of larger models) to provide the dry matter weight of forage harvested in addition to the gross yield.
“With help from Field Track & Trace software, this data can be made available on the farm office computer and we envisage producing yields maps in future,” says Henk Brons, export manager.