Side-shift linkage options deliver pinpoint crop weeding
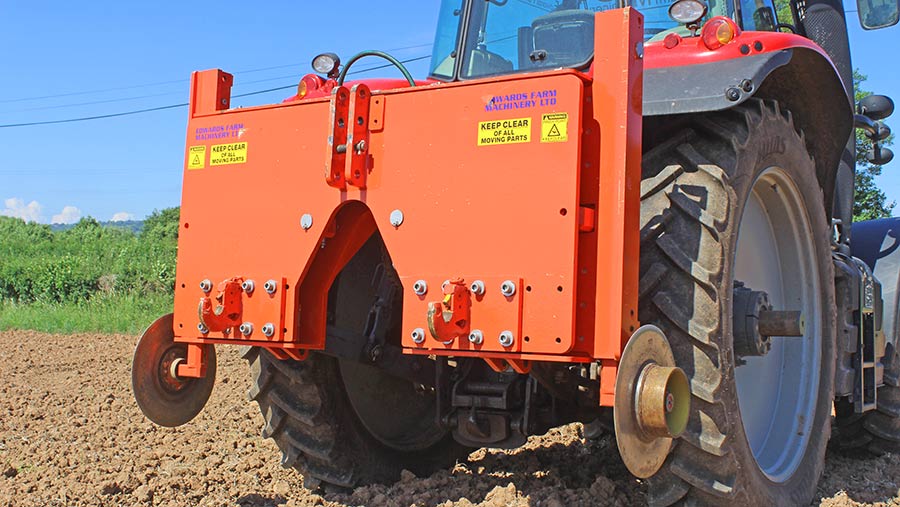
Razor-sharp RTK guidance systems have nailed the art of driving tractors in arrow-straight lines, but they can’t deal with the inevitable wandering of implements on undulating ground and in changeable soils.
For most operations, this small amount of drift is of little concern, but for those carrying out precision weeding or spraying tasks it can be enough to cause some costly errors.
The answer is implement steering. This technology gives the machine its own GPS receiver – set to the same guidance lines as the tractor – and, via a hydraulic side-shift frame, it has the ability to keep itself plumb in line with the tractor.
See also: Buyers guide: Retrofit entry-level auto-steer systems
Intelligent camera systems can also be used in place of the implement’s GPS receiver to correct its path according to the actual growth of the crop, rather than following virtual guidance lines.
Both of these setups have been around for a number of years but, like a lot of cutting-edge technology, it’s taken a while for them to filter down to farm level.
Even now they are primarily used by growers of high-value veg crops – particularly organic – where precise inter-row rotavating and hoeing is crucial for reducing the amount of tedious and expensive hand weeding.
However, these systems are also accurate enough to work in rows of wide-spaced combinable crops, which could help to lower the weed burden for organic growers, farms with herbicide resistance and those looking to reduce their reliance on agrochemicals.
Initially, the linkages that allowed implements to move from side to side were fairly lightweight, and this meant they were only suitable for surface weeding, spraying or seeding jobs. However, some heavy-duty versions are now available, which bring greater accuracy to crop establishment.
This might seem over the top, but getting crop placement right from the outset means weeding equipment can run closer to the crop later in the season without running the risk of damaging it.
Edwards Farm Machinery
Worcestershire-based veg specialist Edwards Farm Machinery has been building side-shift linkages at its workshop near Tenbury Wells for the past four years.
It makes both light and heavy duty versions, but as the price difference between the two is negligible, business director Rob Edwards usually steers customers towards the stronger one.
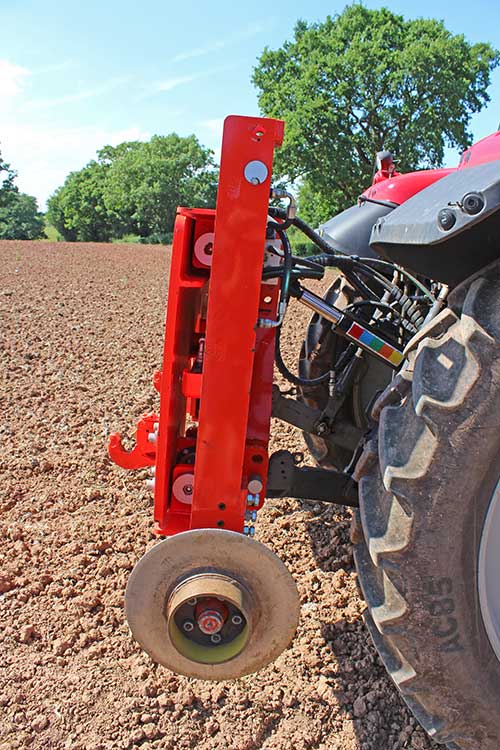
Edwards Farm Machinery side shift
“There’s more metal in the heavy duty version, but the manufacturing process and build time is identical,” he says. “So, it’s a better bet to have the heavy one and make all operations more accurate.”
The Edwards side-shift mounts between the tractor and implement and is essentially made from two 25mm-thick metal plates that slide independently of one another.
The plate attached to the tractor link arms needs to resist the pushing forces transferred from the implement, otherwise the back of the tractor would be pushed out of line by heavy ground-engaging equipment.
Mr Edwards and his team came up with a pair of discs on hydraulic rams that can be lowered to the ground. These bite in and anchor the frame, meaning the tractor stays put and the implement is forced to move into line.
As for the sliding element, this consists of four 300mm-long sections of 80mm chrome bar incorporated into the tractor side of the frame. The rear section attaches to these via some grease-free phosphor-bronze bushes and a pair of hydraulic rams pushes it from side to side as required.
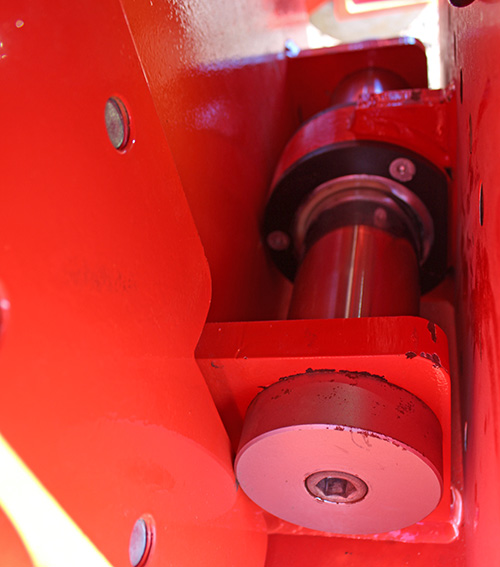
The sliding mechanism
The plate can move the full length of the chrome bars, so it has 150mm of shift in either direction. An open section in the centre of the plates also means the linkage will work with pto-driven implements.
In operation, the GPS receiver or camera system works out where the implement needs to be in relation to the tractor and, if it’s out of line, sends a signal to an electro-hydraulic valve on the side shift.
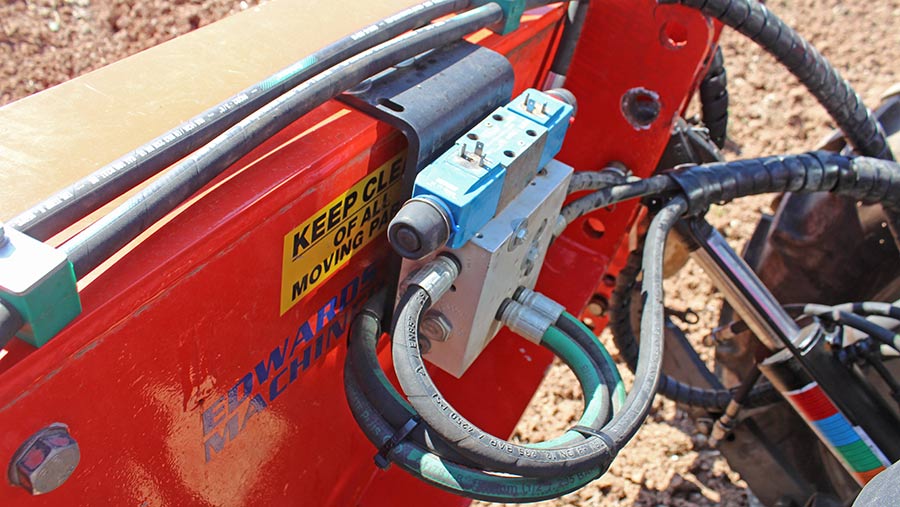
the side shift hydraulic valve
This valve then directs oil flow to the ram so that it brings everything into line. The final part of the puzzle is a potentiometer on the rams which helps the control system work out the position of the frame and allows it to automatically return to centre on the headlands.
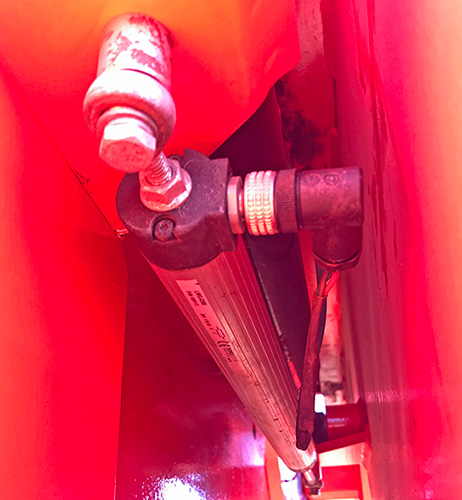
The potentiometer
To make sure there’s always oil flow available, the linkage needs to be plumbed directly into the tractor’s load-sensing hydraulic line or a spool set to constant pump.
All metal for the side-shift is laser cut to plans put together by engineer Joe Breakwell and is fabricated in-house. More than 1t of steel goes into the construction and that means it is strong enough to carry the biggest bed formers on the market.
With all this weight hanging off the rear linkage, Mr Edwards says they’ve worked hard to keep the linkage as slim as possible. “We didn’t want to push the weight any further back than we had to, so we’ve managed to keep the distance between the tractor hooks and hitch hooks to just 400mm.”
The heavy-duty side-shift costs £11,000 and it will work with most GPS and camera systems.
Case study: RB Organic, Kings Lynn, Norfolk
Keeping 145ha of organic veg crops clean requires a mechanical weeding system that’s on point.
Since it was formed in 2005, RB Organic, based near Kings Lynn, Norfolk, has been working to perfect its technique and has invested in several pieces of high-tech equipment, particularly for its 75ha carrot crop.
One of the most recent acquisitions is a pair of heavy-duty side-shift linkages built by Edwards Farm Machinery. These were chosen over a dedicated camera-guided hoe as they were more versatile and cost a lot less.
Opting for heavy rather than lightweight units also meant they could be used for both establishing the crop and weeding, allowing both operations to be run on identical A-B lines.
Before investing in the hitches, RG relied on the ridging tractor’s RTK guidance to set out the crop spacing. However, when it came to weeding with a camera-guided hoe, the original bout lines were not accurate enough.
“Even though the tractor was driving perfectly straight, there was enough drift in the ridger to mean the guidance lines didn’t match up perfectly across the field,” says farm manager Alex Parkinson.
“That meant we were constantly having to centre the GPS when we were weeding so that we didn’t damage the crop.”
With the arrival of the side-shift linkages, the farm’s John Deere 6250R tractor and ridging machine have been responsible for laying down ultra-accurate A-B lines that all other operations follow.
The base guidance line is generated by the tractor’s RTK guidance – running off a local dealer mast network – and this communicates with a slave guidance system fitted to the side-shift frame.
When the slave GPS system senses that the ridger is out of line with the tractor it sends a signal to an electro-hydraulic valve on the sideshift frame which, in turn, triggers a hydraulic ram to bring the two into sync.
Both side-shift frames run off the tractor’s load sensing hydraulics, meaning there is always oil flow available to this ram, without having to have a spool valve set to constant pump.
Once the straight and evenly spaced ridges have been established, the destoner, bedformer and planter can be kept in line without needing to use the side-shift frame.
RB Organic’s carrot drilling campaign kicks off in April and is usually wrapped up by June, but by this point the early crops are already being weeded. This clash is why the firm invested in two side-shifts, one for establishment duties and the other on the inter-row rotavator or hoe.
Camera guidance
For the weeding operation, the side-shift’s GPS unit is removed and replaced with Tillett and Hague camera guidance. This has its own hydraulic valve and wiring loom, making it simple to switch between the two systems.
In camera mode, the tractor runs on the original bout lines set out by the ridging tractor, but the camera is in charge of the fine adjustments. By accurately distinguishing between leaves and soil it allows the weeding equipment to work right up to the crop row without causing damage.
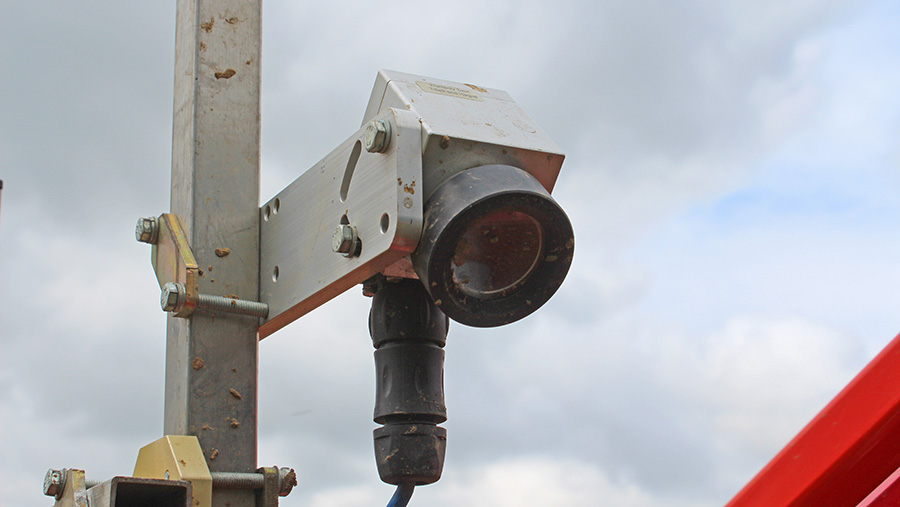
RB Organic Tillett and Hague camera system
This precision minimises the amount of hand weeding required. Hand weeding is still required in the gaps between plants in each row.
Until the plant reaches five true leaves, most of the mechanical weeding is carried out with an inter-row rotavator. After that, a triple hoe takes over and it is fitted with narrower A blades as the crop grows.
Once the crop begins to meet between the rows and the camera system can’t distinguish between them, the hoeing job comes to an end.
The side-shift frames are also used to improve accuracy of the farm’s potato and onion operations, as well as organic cereals.
In this situation, the GPS side-shift is used with a conventional cereal drill that has every other coulter blocked off, giving 25cm rows. This apparently has little impact on yield, but gives enough room to weed between rows with a narrow A-share hoe guided by the camera system.
“We’ve essentially created a lower-cost version of the [Gothia Redskap] System Chameleon drill, working with equipment we already have,” says Mr Parkinson.
Other side-shift options
Laforge
Laforge’s long-established relationship with John Deere led the French firm to develop a side-shift interface for use on Deere’s two-point-linkage trailed planters in the US.
However, since its market launch in 2014, the Dynatrac has been redesigned to work with a three-point linkage.
The two halves of the linkage arrangement slide over one another on sections of heavy-duty chrome bar, and this action can be controlled by either GPS guidance or a camera system.
Unlike many other systems of this type, the Dynatrac has one free-floating link arm that allows the machine to follow movements from the tractor. When it is lifted out of work a hydraulic ram locks it in place to prevent the implement swaying.
A vertical ram is also in place that jacks the frame up or down to level the implement, which compensates for increased tyre deflection on the downhill side. According to Laforge, this ensures implement depth remains consistent across its width.
To allow the linkages to work with heavy equipment, the frames are built from 100mm steel box section and the rams are 80mm units. Composite grease-free bearings have also been used to reduce the amount of maintenance.
Top-spec Dynatrac Ultima models weigh 1,500kg and offer up to 500mm of side shift, as do Premium models, which are designed for implements without a pto.
The smaller Premium Plus weighs 800kg, has a 300mm shift and does accommodate pto-powered implements. This is the most popular model as it’s able to work with category 2, 3 and 3.5 linkages.
A new lightweight, lower-cost model called Dynatrac Compact is aimed at growers covering smaller acreages.
Prices start at €7,000 (£6,300) and go up to €17,000 (£15,300) for a full-spec Ultima linkage. They are available in the UK through Zurn and Manterra.
Garford
UK precision specialist Garford Farm Machinery has been building side-shift linkages since its Robocrop inter-row hoes were introduced in the early 2000s.
Initially, these worked only with the Robocrop, but Garford now offers an optional quick-hitch feature that makes them compatible with most implements.
There are three sizes – SD30, HD50 and XHD50 – which can accommodate various width machines.
The SD30 offers 300mm of side-shift with a 1,500kg lift capacity, and this is suitable for implements up to 4.5m wide.
The HD50 sits in the middle of the range, offering 500mm of side-shift and a 2,500kg lift capacity, while the XHD50 offers the same amount of deflection with a 4,000kg capacity.
This makes it big enough for bed forming and planting operations, and it can accommodate a pto. It is designed to work with implements up to 9m wide, or 12m if they are fairly lightweight.
All models run on roller bearings and have two hydraulic rams to do the shifting. They are also compatible with both GPS and camera guidance systems.
There is a choice of stabilising kits to keep the tractor and implement supported when shifting, including an auto reset option for stony ground.
Garford builds about 300 units a year, selling mainly to the veg and organic markets, but it also has a number of cereal growers using the system. Prices starts at £18,000, although most builds are bespoke and the cost varies according to user requirements.
Wifo
Dutch manufacturer Wifo offers two models of side-shift linkage; one capable of housing a pto and the other built to handle bulkier implements.
The DSD-Z-500 is the bigger of the two, with 500mm of side-shift and a maximum lift capacity of 4t. It weighs only 400kg and can attach to two- or three-point linkage implements.
Prices for the category-three model start at €4,825 (£4,380).
Agmechtronix
US firm Agmechtronix builds a side-shift linkage that is primarily designed to work with its clever camera-guided lettuce-thinning machine.
It is comfortable working at speeds of up to 6.5kph, can accommodate a camera for each of the crop rows and offers up to 300mm of side-shift.
The company says these linkages allow the implement to cultivate closer to the plant, which takes some of the pressure off the driver.
A touchscreen in the cab allows the operator to make adjustments when in work and this is also set up for remote dealer access to help troubleshoot any problems.
So far, it has been tested only on veg kit weighing about 3,000kg. There is currently no option for GPS guidance and it is not compatible with pto-powered implements. It costs $16,000 (£12,760).