Borders contractor geared up to bag over 9,000t of forage/day
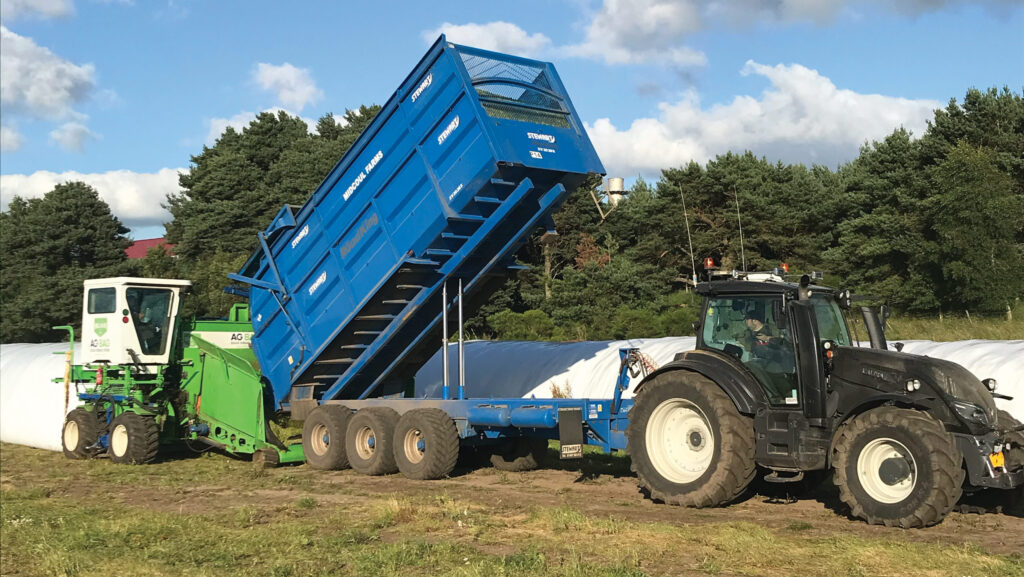
There used to be plenty of contractors offering a forage-bagging service, but the dedication required to run these machines efficiently means just three players remain.
One of those is Hawick-based Bill Rae Contracting, which has been in the game for more than 30 years and is run by father-and-son team Bill and Kevin Rae.
Together with their five bagging machines – essentially gargantuan sausage makers – they cover the whole of Scotland and northern England, travelling as far south as Hull and Manchester.
Grass and wholecrop are the main feedstuffs they work with, although they bag some maize and small quantities of moist feeds and crimped grain, plus sugar beet pulp.
See also: Keenan mixer wagon renovator offers repair tips
The duo have also recently become a dealer for German brand Budissa Bag, whose machines they use themselves.
They offer a broad range of products, but the main market in the UK is for smaller farm-scale auger baggers (see Budissa Bag dealer, below).
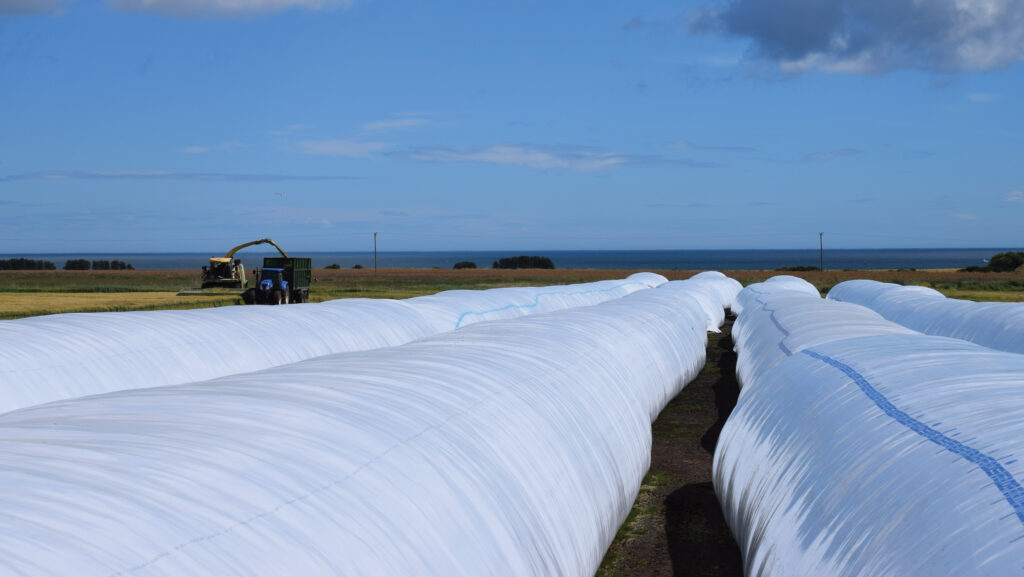
© James Andrews
Benefits of bagging
One of the main attractions of silage bagging is that no infrastructure is required, other than an area of hardstanding to put them on.
This means there’s no need to build or maintain a clamp, and no more sheeting or flinging old tyres around.
“There’s also no shoulder that goes off – you get out exactly what you put in,” says Bill.
The bags provide handy extra storage for those that want to carry out third or fourth cuts when their clamp is already full.
Or for farms that want to temporarily store the remains of last year’s feed, freeing up the clamp for the next crop.
But the main customer base is those who have decided to move away from round bales.
Far less work is required, as the feed is safely stored in the yard as soon as the contractor leaves, and there’s only one third of the plastic to recycle at the end of the season.
Like any good silage, it’s crucial to get decent compaction and remove as much air as possible. The machines do this by packing the material in tightly as the tubular bags fill.
On smaller models, this is achieved by pushing against a net that’s secured to the end of the bags on wire ropes, but larger models use anchors that secure into the silage.
Both ends of the bag are fastened with an airtight sealing strip and a vent is installed to allow fermentation gasses to be released. This can then be closed after a couple of weeks, completely sealing the bag until the fodder is needed.
To achieve the best quality feed, the crop should ideally be ensiled with a dry matter of 28-40%. Fermentation begins almost immediately and after three weeks the pH will drop to about 4, keeping the contents stable during the storage process.
Just like wrapped bales, the plastic can get pecked by birds, but nets are available for those who have trouble with this.
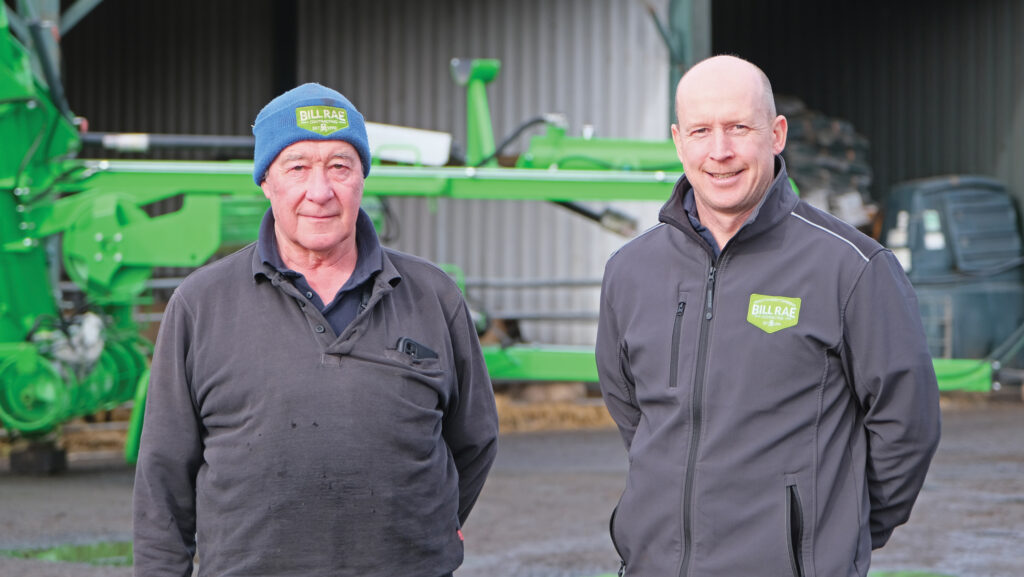
Bill and Kevin Rae © James Andrews
Complex logistics
Having such a large area to cover means the Raes’ logistics have to be on point.
As most of the products they ensile are picked up by self-propelled forage harvesters, they tend to simplify the process by dealing directly with the contractor.
“This is the easiest way of making sure we’re in the same place as a forager, and massively cuts down the number of phone calls,” says Kevin.
It also allows them to carry out smaller jobs as they aren’t having to make special trips from their yard.
“If we get a good run of weather, we can have one machine stationed in an area for a couple of weeks, catering for farms of all sizes.”
In catchier times there’s a lot more travel involved as they dart around to find people who have dry enough weather to work.
“On the plus side, the fact we cover such a large area means there’s often somewhere we can go,” he says.
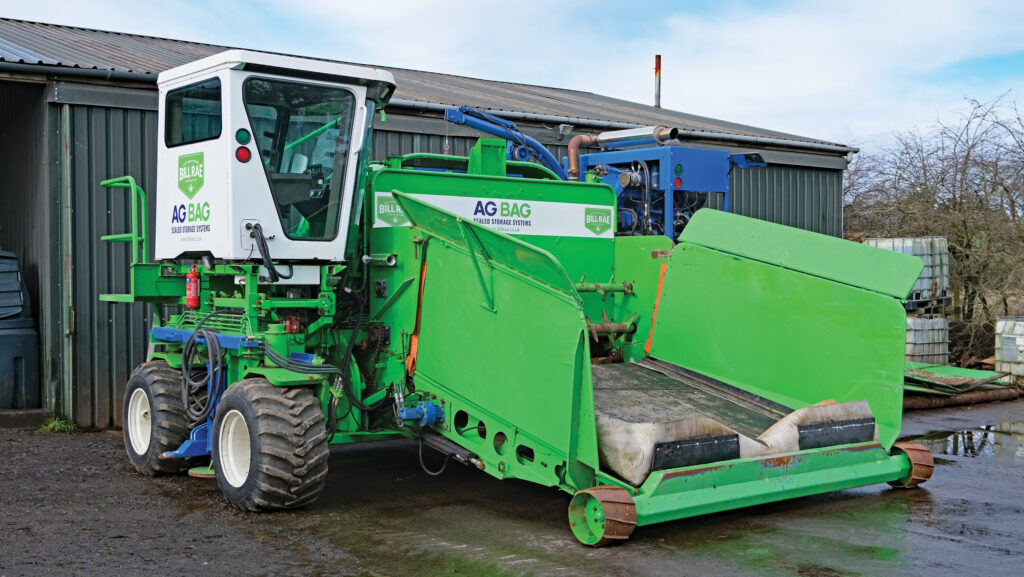
© James Andrews
Transporting machines
A pair of HGVs with low loaders are used for transporting their two largest 12ft machines, and their three 10-footers tend to be pulled by tractors.
For this reason, the smaller machines do a large chunk of their local work.
Both models work in a similar fashion – the process starts with a trailer tipping on to a conveyor belt that feeds into a heavy-duty horizontal rotor.
This forces the feedstuff into the bag, which starts out concertinaed on a frame around the rotor and unfurls as the silage is pushed in.
Operators have several ways of controlling the rate of fill, such as adjusting the speed of the elevator and the pressure of the brakes.
Because the action of the bag filling pushes the machine along, if the brakes are applied it helps increase the crop density.
The pressure in the tensioning system also has an effect, so there’s a constant balancing act required to do a tidy job.
Output of the largest 12ft models is about 2,000t a day when filling 150m long bags, each of which can hold 900t.
As the bags can be sealed at any point, there’s no problem doing smaller jobs for customers. In these instances, they just use a part bag and take the remainder to the next job.
This means the cost for most customers remains consistent at about £7/t, including plastic.
The only limitation of the 12ft machine is that it sits at 23ft when folded out for work. This can be a bit tight in some yards, which is where the 10ft models come into their own.
Another benefit of these is that the smaller diameter bag has less of a face to go off when feeding is less frequent.
Output isn’t that much lower than the 12ft models either, so they can still manage 1,800t or more a day. In fact, for both sizes of machine the trailers hauling the silage are the biggest limiting factor.
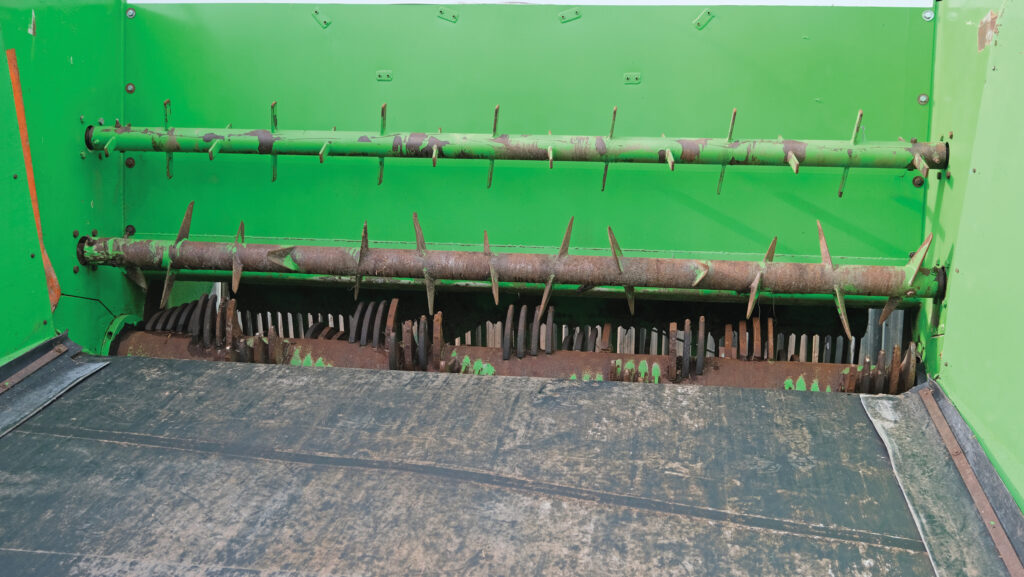
©James Andrews
Keeping them running
With the price for a 12ft bagging machine at present sitting at about £500,000, they need to give years of service to pay for themselves.
The oldest model on the Rae fleet is an original US-built AgBag MB10000 powered by a 450hp John Deere six-cylinder engine. It is now 10 years old and still going strong.
Part of this is down to the fact that it, like the rest of the fleet, gets a thorough service and rebuild every winter, with any worn components being replaced.
“The last thing we want is them breaking down in the middle of the job, so we go through them carefully before the season starts,” says Kevin.
Typical replacement parts include new wear caps on the rotor teeth, feed elevator belts and chains.
“There aren’t too many electrics, so we can do most of the work on them ourselves and keep refurbishing them,” says Bill.
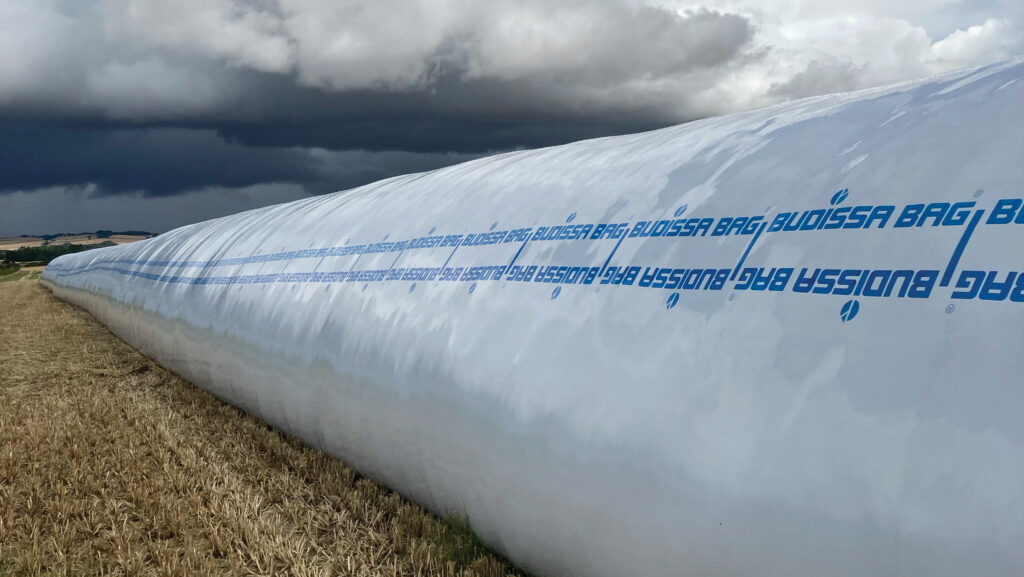
© James Andrews
Budissa Bag dealer
Bill Rae contracting has been the UK dealer for Budissa Bag since June last year.
Although it offers large, contractor-focused rotor bagging machines, the main market is for smaller auger-bagging models designed for on-farm use.
A popular option is the GBK-W Grain Bagger, which can be used to fill 5ft or 9ft diameter bags with wet or dry grain, or any other material that can be fed through an auger.
The primary use in this country is for storing crimped grain, brewers’ grains and distillers’ grains, but there’s also potential to use it for low-cost dry grain storage on arable farms.
This is common in North America and parts of Europe, but has yet to take off in a big way here.
Loading is carried out either by filling the integrated hopper with a bucket or tipping into an optional side auger from a trailer chute.
The machine then winds the product into the bag, which extends automatically as it fills.
Grain bags are available in continuous lengths of up to 120m and filling rates of 200t/hour are possible.
Emptying involves another piece of kit with a series of augers that wind the material out of the bag into trailers.
Uploading rates of up to 250t/hour are possible and the discharge auger is tall enough to load into an HGV.
Combined price of the GBK-W Grain Bagger and Grain Bag Unloader is about £43,000 and the plastic costing works out at roughly £2.31/t of material stored.