What’s in Your Livestock Shed? visits a state-of-the-art pig unit
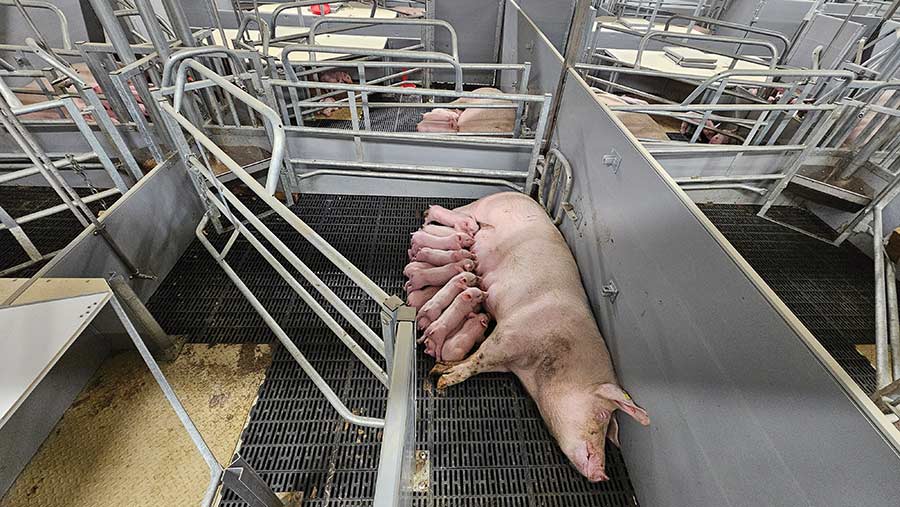
A state-of-the-art indoor pig farrowing and dry sow unit, projected to produce more than 10,000 piglets a year, is showcasing some of the highest levels of indoor pig welfare and biosecurity.
The brand-new farrowing house at Bishop Burton College, Yorkshire, has been fitted with 72 freedom farrowing pens, while an old bacon house has been adjusted to accommodate dry sows and gilts.
The site also includes a canteen, office space and provision for excellent hygiene measures designed to minimise contamination risks.
See also: How lean management saved pig business £50k
Farm facts
- 300 sows
- Five-week batch farrowing system
- Sows farrowed on a bed-and-breakfast basis and owned by White Rose Farms
- First batch of gilts farrowed an average of 15.9 piglets and reared 14.2
- Target to produce 10,000 piglets a year
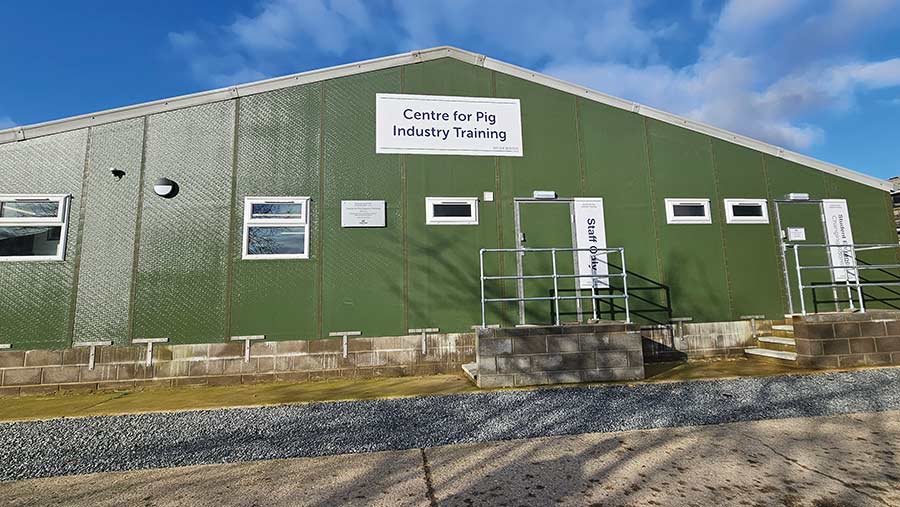
© Sarah Alderton
The unit has been built as a Centre for Pig Industry Training and is run as a commercial operation and collaboration with White Rose Farms, part of Cranswick.
Pigs are managed on a “bed-and-breakfast farrowing” basis before being weaned and moved to units owned by the partners.
James Richardson, Bishop Burton College’s farm director, talks about the new investment, which welcomed its first sows on 6 November 2023 and saw the first piglets arrive a month later.
Why did you invest in the new centre?
The college was running a farrow-to-finish operation with 300 sows. It was very labour-intensive, with the bacon pigs housed on straw and mucked out by hand.
We had also moved to outdoor farrowing in huts, which resulted in high piglet mortality.
Rather than focus on throughput, we decided to scale things back, focus on one area, and do it well.
We chose farrowing because, from a college point of view, this provides more educational opportunities, such as serving, weaning and management of the piglets.
What are the main features of the farrowing accommodation?
The farrowing accommodation (46.2×16.8m) is made up of two rooms, each containing 36 AM Warcup adaptive farrowing (freedom farrowing) pens.
We know crates are being phased out, but we still have no indication when this will be, so we wanted to ensure that what we installed was future-proofed.
We went above the standard size of 5.75sq m and opted for a 2.4×2.7m pen, giving an overall area of 6.5sq m.
We have seen a huge progression in genetics, with litter sizes up to 14-15 piglets a sow, so we wanted to build in that extra space.
At the point of farrowing, a temporary crate is formed to house the sow, where she remains for 24-48 hours or until the piglets are mobile and strong enough to avoid being crushed.
The temporary crate has all the features of the fixed crate, but on opening, it allows the sow to move around the pen. However, it does prevent her from accessing the creep.
The creep area has a solid, heated floor and a two-part lid. The rest of the floor is slatted.
Two sides of the crate move, which gives the stockman different options for restraining the sow if any intervention is required.
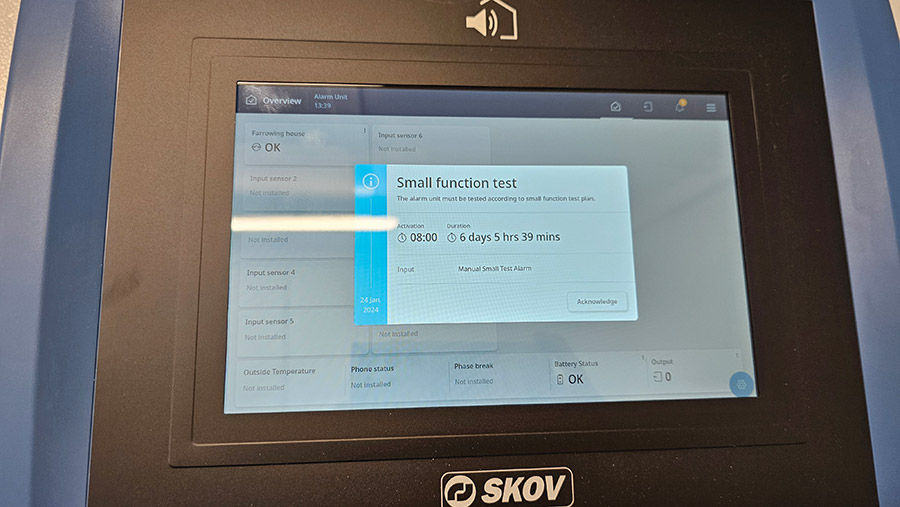
© Sarah Alderton
The farrowing building contains a plug-and-play Skov ventilation system, which sets the temperature, air quality and humidity, and controls the fans outside, which blow the air in.
It also controls the sprinkler system, which we turn on once the farrowing room is empty to pre-soak each pen before pressure washing the room down.
We have also installed wiring for heat lamps above each pen, should we need to add them.
Enrichment is provided in the form of wooden blocks.
Sows are fed using manual feeders in the farrowing house, but these can be upgraded to electronic sow feeders (ESF).
We couldn’t see the return on investment in ESF feeders here. Manual feeding also means each pig is checked at least twice a day.
Piglets are fed manually using a plastic dish in the pen. Nipple drinkers are also provided for the sow and piglets.
This is how we see the future of high-welfare indoor pigs.
What are the benefits of this type of system?
In our new pens, we provide enough space for the sow and paper nesting material for her to express her natural behaviour, while safeguarding the piglets.
We’ve only had one batch go through the system, and they were gilts. They farrowed at 15.9 piglets a sow and weaned at 14.2.
What is your favourite feature?
The pen itself and the flexibility with the gates. The piglets can also be restrained in the creep area if needed.
We want visitors, students and staff from across the college to engage in and learn from our work in this new facility, so we encourage them to use the viewing gallery to see what’s happening in the unit.
What is the students’ favourite feature?
The creep area in the pen makes it easier for the students to interact with the piglets without any risk from the sow.
How much did the project cost?
Just over £1.2m, including VAT. This included everything from the planning permission and consultancy fees to the building.
AM Warcup was the principal contractor. The design was an off-the-shelf system.
There were some unexpected costs that we had to incorporate, such as a full emergency lighting system and a fully integrated fire system, which added about £20,000 to the cost, but these were a requirement for a college site.
This took us over our £1.2m budget.
Have there been any teething problems?
We had a water leak at the start, and we also had to install a timer on the auger that filled the ESF in the dry sow shed so the feeders didn’t go empty.
If you had to change one thing, what would it be?
I’d probably add a passage at the bottom of each farrowing room to save having to go out of one door and back in the next.
However, we have foot dips outside each door, so, from a biosecurity point of view, our design maximises that.
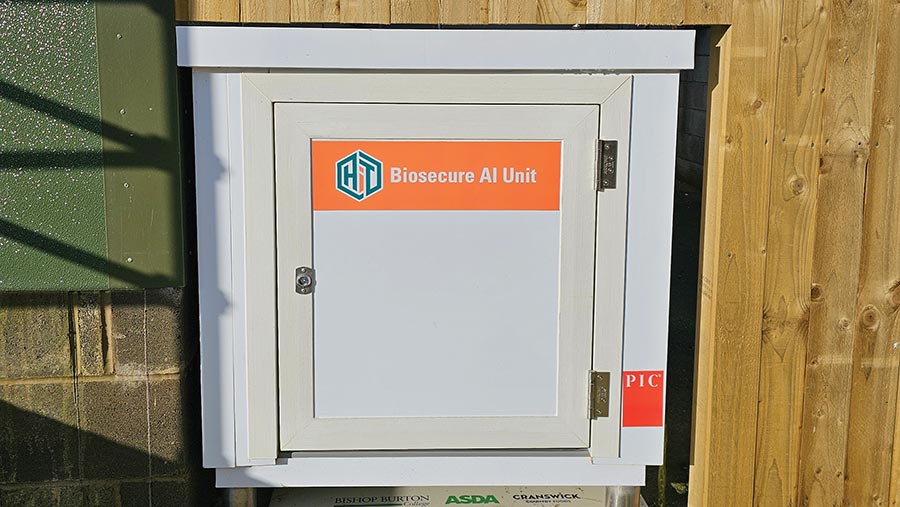
© Sarah Alderton
How else have you maximised biosecurity?
We operate the site as a shower-on, shower-off unit. We have dedicated changing rooms and provisions to maximise hygiene and minimise contamination risks.
We have a biosecure artificial insemination (AI) unit, which can be accessed from both sides of the pig building, so semen can be delivered without anyone entering the unit.
On the other side of the pig building is the “dirty” end. This is where we scrape the muck and where our slurry is stored before being pumped into the slurry tank.
It’s also where animals leave the unit. We have a dedicated loading area where lorries pull up to load stock.
We have even installed controls for the slurry pump outside the pig unit perimeter, so engineers can access it without entering the biosecure site.
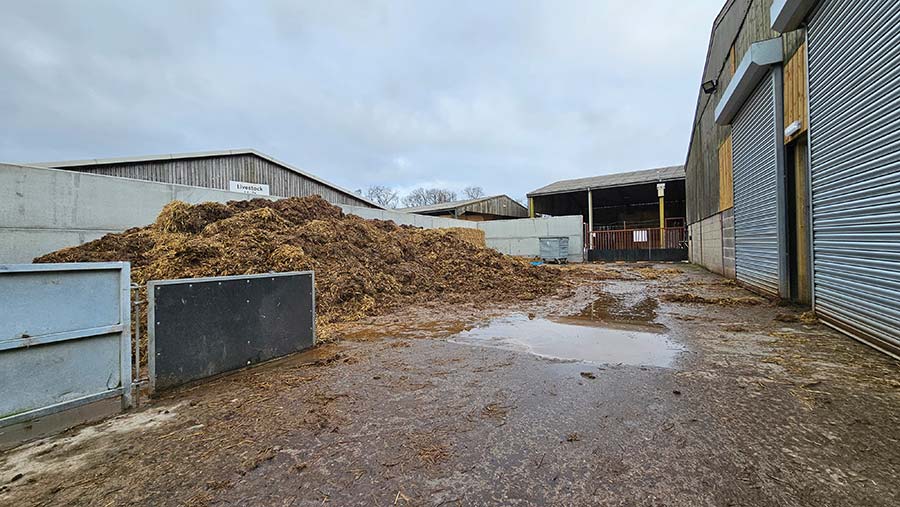
© Sarah Alderton
What about future plans?
In the next five-to-10 years, the ambition is to be a farrow-to-finish unit. We have had plans drawn up for this.
We are also considering investing in a pig counting system called Ro-Main, which uses a camera mounted in the corridor to count pigs with 99.9% accuracy.
Figures suggest there can be up to a 10% discrepancy when counting pigs manually, so this will remove that.