How a 540-cow dairy benefited from recycled bedding
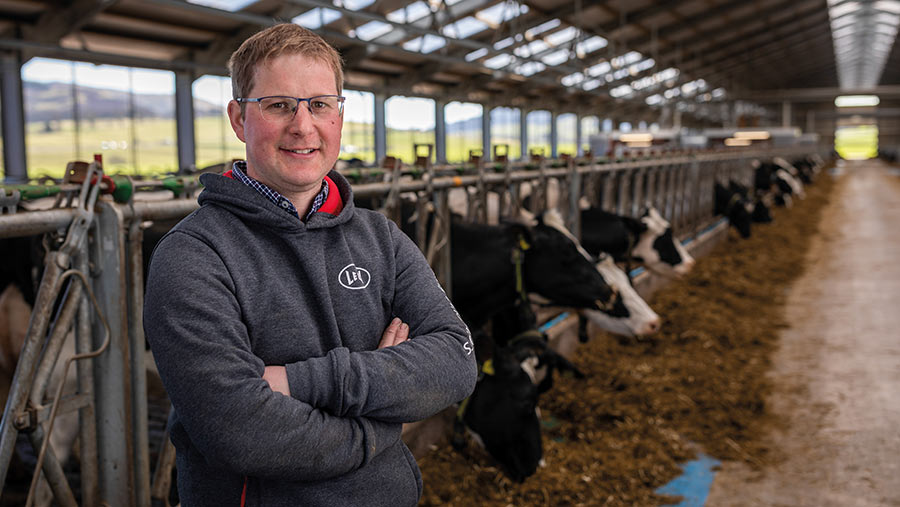
A leading dairy herd has been bedded on recycled manure solids since opening its new cubicle house in 2019.
The Laird family at Blythbridge Holsteins, West Linton, Peeblesshire, stress that keeping bedding dry and flooring clean are essential for the recycled manure solids (RMS) system.
“We wanted a deep bedding system for cow comfort and lying times, and the recycled manure solids help us achieve that,” says Colin Laird, who farms with parents Alister and Kathleen, wife Izzy and four full-time staff members.
They considered sand bedding, but this would have meant installing a lagoon.
“That didn’t seem wise with us being so near a village, and with a lot of wearing parts on the robots and the need to dig out sand from the tank, we decided against it,” says Colin.
See also: What’s in Your Livestock Shed? visits a £1m robotic dairy
Blythbridge Holsteins
- 540 Holsteins in milk
- Cows average 40.2 litres a day and about 12,500 litres a lactation
- 4% butterfat and 3.2% protein
- Supplies Tesco Sustainable Dairy Group
- 384ha (950 acres) at Blythbridge, 10% of which is arable
- 283ha (700 acres) near Kinross, 50 miles away, 80% of which is arable and where youngstock are reared
- Malting barley, feed wheat and oilseed rape sold into market
System change
Pregnancy rate has lifted 8% to 26% and daily yield has increased by 6kg a day to 40.2kg since the switch to the new cubicle shed with robots and RMS.
About 430 cows are on RMS in the new shed. A smaller adjacent shed has 110 cows milked through two robots on a mat and sawdust bedding system, which used to be the farm’s bedding method for the whole herd.
The shed has 450 cubicles with slatted floors around all cow walkway areas, and 15.75m litres of slurry storage underneath them.
It is split into four cubicle areas with two Lely A5 robots in each. Each robot takes 2,200 litres a day, so running heifers, second-calvers and mature cows together manages daily supply.
Two Lely Juno feed pushers take half-an-hour to go up and down the shed, and do this every 90 minutes.
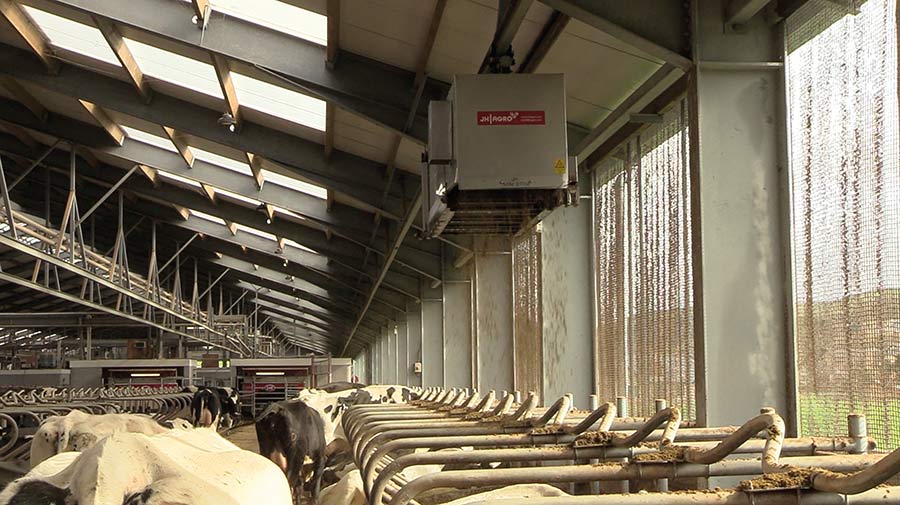
© MAG/Michael Priestley
How it works
A pump transfers slurry – mixed by eight automatic submersible mixers overnight – from the underground store tank to a 7.5kW Bauer Green Bedding Separator 3.3-780.
Here, slurry is forced through a screw press at up to 20cu m/hour, turning it from 7.5% dry matter (DM) to 36% DM in seconds.
The liquid fraction dribbles through a sieve and gravity takes it back down to the slurry tank. The fibres fall through a chute to a 1cu m bedding box.
It takes 15 minutes to fill the box, which then travels around the shed like a train on a track above the cows.
Bedding is dropped from the box via conveyor belt motion onto the cows and cubicles throughout the day.
Alister explains this distribution method suits the robotic system, as cows do not leave the cubicle shed.
A full box can top up one row of 70 cubicles in the six-row building. Each row is topped up four times a day.
Bedding is hand-raked to the back of the cubicles to the udder each morning.
To help reduce energy costs, electricity is generated from 100kW of solar panels fitted on a shed roof, and a heat exchange unit passes milk through a glycol cooling system to heat the farmhouses and pre-heat water for robots.
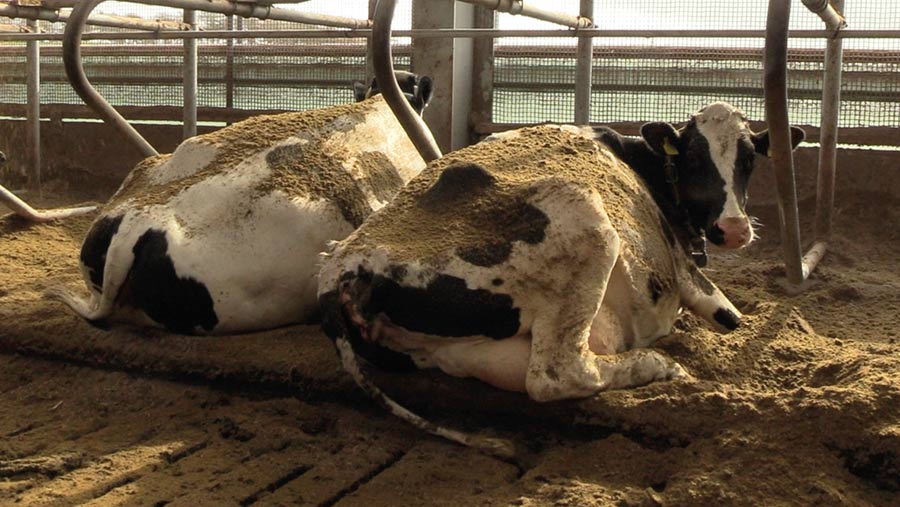
© MAG/Michael Priestley
Recycled manure solids statistics
- Current price for Bauer’s green bedding system is about £70,000 (including slurry mixers, pipework, gantry, slurry separator, control panel and installation)
- About 300 recycled manure solids (RMS) systems are now in operation in the UK, of which Bauer has about 80% market share
- Regular maintenance and replacement are important as the machines create a lot of pressure on wearing parts
- Running times will be no more than one hour a day for every 100 cows on the farm
- Legally, RMS must be 34% dry matter
Right DM level
Supplied at a depth of 15-16cm in each cubicle, the RMS bedding has replaced the need for mats.
Ensuring the bedding has the correct DM content is critical.
Too wet, and it becomes unhygienic and can stick to hooves and teats; too dry, and it can blow about and fail to form a comfortable, springy cushion under the cows, negating the cow comfort benefits.
“It’s clean and hygienic and there are no hock abrasions on the cows. It’s a great bedding for them,” explains Colin.
He lists some key parts of the shed design that help dry the bedding to 60-65% DM once it is under the cows:
- Height of bedding box Bedding drops from a height of 2.5m above the cubicle bases, giving a chance for air to pass through the material
- Position near neckrail The bedding box runs along the front of the cubicles, dropping the bedding onto the cows’ shoulders and backs. Their body heat gives the bedding another chance to dry
- Climate control Inclement weather is kept out of the shed by Airkoe curtains, which can be lifted and dropped as required (a 300mm gap is kept at the top of the curtains to always allow fresh air through). When the weather is warmer and a through draft is strong, this helps the bedding dry further.
Herd health
Three automatic slurry scrapers (Lely Discoveries) scrape the slatted floor every two hours to keep flooring, feet and bedding dry and clean.
Automated foot-washes in the back of each robot spray a mix of formalin, copper sulphate and zinc at the cows’ feet.
Mastitis issues are no different to those seen in the sawdust system in the other shed, explains Colin.
Somatic cell counts are 160,000-170,000 cells/ml on both systems, and both sets of cows are in a selective dry cow therapy programme, with about 20% of cows receiving treatment.
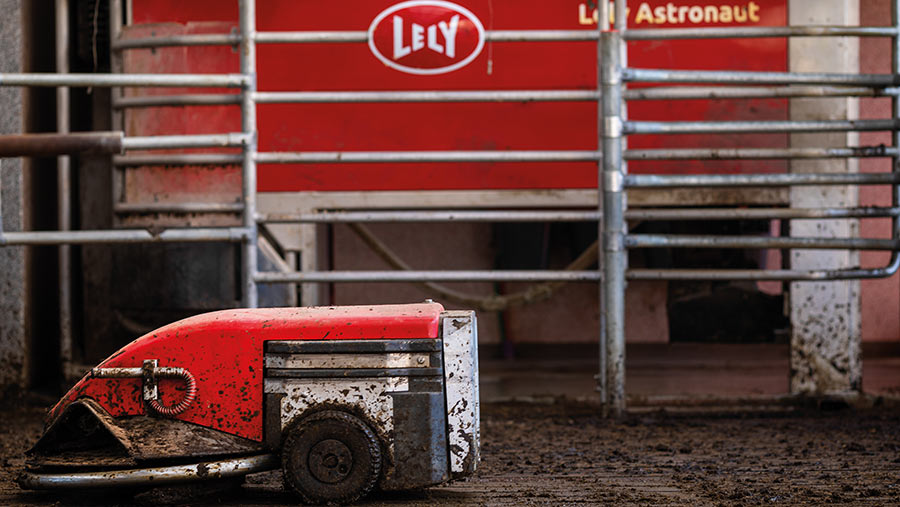
© Lely
Slurry spreading
The slurry storage capacity beneath the shed comprises two tanks.
A 4.5m-litre store beneath the robots collects the slurry and waste milk and parlour washings separately to stop bacteria going through the separator and into the bedding.
This smaller tank is accessed by a pump, which is driven by a 350hp engine on an axle-unit slurry pumper to arable and silage fields through up to 2,000m of pipe.
About 4,550cu m of slurry is applied to first-cut silage ground, and a similar amount thereafter for each subsequent cut.
About 10,000t of silage is produced each year, with up to four cuts done on about 194ha (480 acres).
The numbers
- 7 How many full-time labour units are required across both farms, including doing all slurry, silage, and cultivation work in house
- 284 How many hours a week have been saved by switching from three-times a day milking on a rotary parlour to a robotic system with automated slurry scraping and bedding
- £8,400 How much has been saved each year on 12 loads of sawdust at £700 a load