Advice on cleaning free-range poultry sheds
Planning turnaround and the logistics is a big undertaking. But a well-executed clean can help set a new free-range flock off to a flying start.
Andrew Watson of Bowler Eggs – who also has 18,000 birds of his own – advises first getting a good cleaning contractor booked well in advance of the depopulation date.
“The big mistake is leaving it too late before you make that booking. Allowing plenty of time will help a producer book the right company to make sure the job is done well,” says Mr Watson.
See also: How poultry farm data can improve performance
“When producers try to tackle the job themselves and they haven’t got the experience or are trying to cut costs it can lead to a failure of the correct standards of cleaning being applied.
“That means there can be a carryover of viruses and red mite and other health challenges to the in-coming flock. Trying to save money on cleaning but ending up with a disease outbreak is counter-productive.”
Mr Watson advises getting as much material out of the shed as possible before any water is used.
“And having good pressure and an adequate reservoir of water to work with is essential. There has to be a dialogue with the contractor well ahead of time so you are clear of what’s required.”
Mr Watson says high-powered “turbo” lancers fitted to pressure washers are pieces of equipment that now play an important part in achieving the highest standards of cleaning.
“But they are best handled by experienced operators and used correctly as part of the strict and methodical cleaning routine once the shed is emptied.”
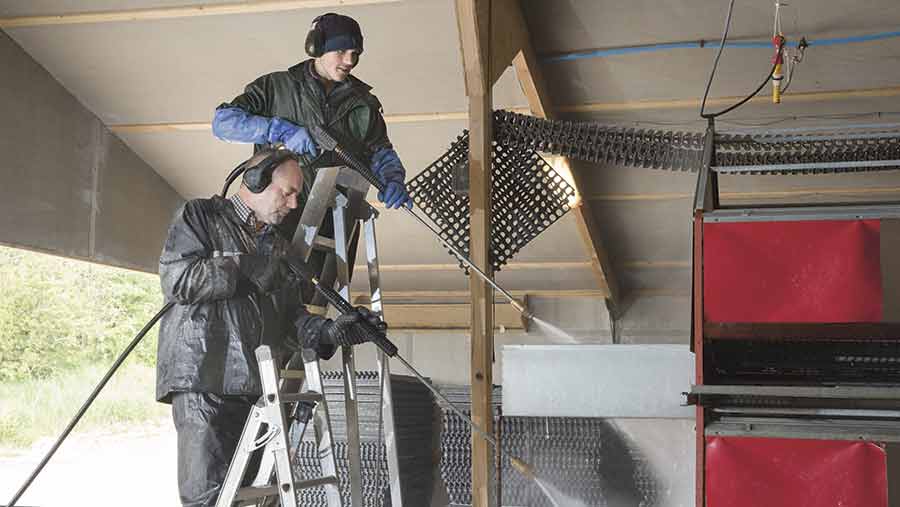
© Tim Scrivener
Flooring
Invest in good floors – that’s the advice of Bob Gooderham, whose Norfolk-based company has been providing cleaning services for poultry producers for more than 30 years.
“There are a lot of poultry businesses where producers haven’t invested enough in the floors of their buildings. We clean all floors to the very best of our ability but some floors have holes in or the concrete is virtually detonated, while some have lost their top and are badly cracked.
“We always do the best we can but a poor infrastructure is a major challenge.
He stresses that the higher the quality of the floor the better it is to clean. “A lot of people ask why a newer shed is better to clean and the answer is simple – it’s all down to the floor.”
Mr Gooderham says his company has a policy that undertakes a second washout of a shed if the floor is poor quality.
“When we have cleaned a bad floor we will wash out the shed again because the bad floor will send up a fine mist of dirty water. When you clean a good floor that problem doesn’t occur.
“When we clean out we want no organic matter left in a shed, absolutely none.
“The floor is the most critical part of the wash-out. When the floor is concrete there are expansion joints but no part of any of the infrastructure of the shed should be left untouched to harbour any organic matter after the clean.
“The final stage of the cleaning is the disinfection because it is a complete waste of time applying disinfectant on top of dirt.”
Rehousing
Mr Gooderham says the most important piece of information he needs to know from a producer is when the house is going to be re-populated. “Once we know the last birds are out we can start work but we need to know exactly how much time we have.
“It’s all part of the good communication that must be exist between the producer and the cleaning service company to make sure the job is done properly.”
Another consideration is having enough space and water readily available for the cleanout.
“A lot of people don’t have enough water flow so water supplies must also be checked. A water supply that satisfies the needs of the birds is not necessarily sufficient to meet the needs of the wash-out stage of the cleaning process.
“We use water bowsers to feed our pressure washers and all dirty water has to be collected to meet Environment Agency regulations.”
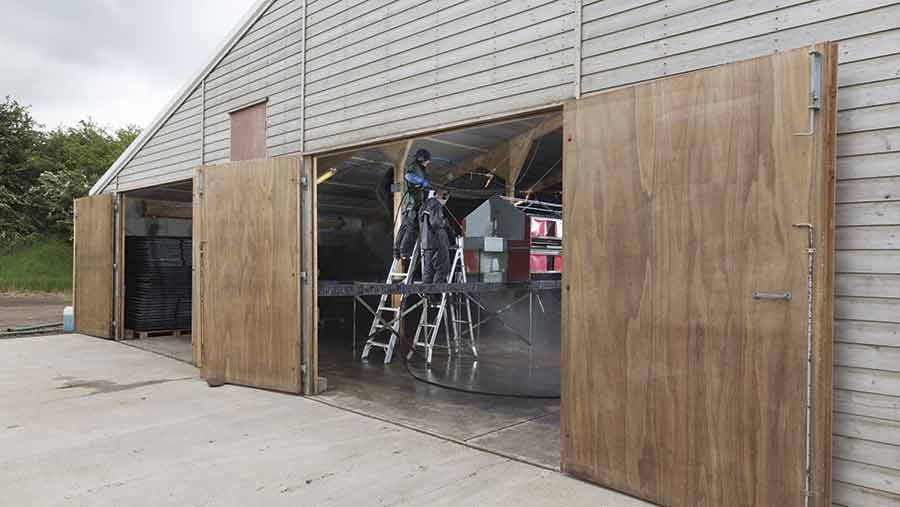
© Tim Scrivener
Pre-soak
The firm begins by pre-soaking a shed with a detergent which includes all the equipment, recesses, ceilings and finally the floor.
“It’s important to allow the detergent to work for about 15 minutes or longer so that it can act on the grime and grease. We then begin to wash the shed from the top downwards using a range of lancer settings and even turbo-nozzles to remove the worst of the soilings.”
The big dilemma facing producers is on cost of cleaning, adds Mr Gooderham. “The question they ask themselves is: “Do I want to have my cleaning job done 20% cheaper but risk a lower standard or should I consider the cost of cleaning to be a part of my production costs?”
“There are always those out there who will do a job more cheaply but a health issue linked to poorer quality cleaning standards that eventually affects production can be very costly in the longer term,” says Mr Gooderham.
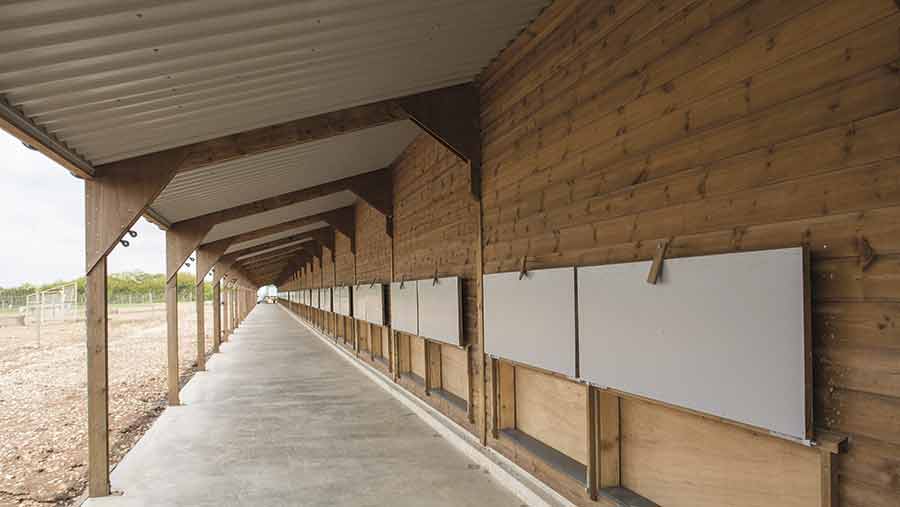
© Tim Scrivener
Feel the heat
Spend time selecting the correct pressure washing equipment and consider a hot water system rather than cold, advises Eddie Beardsley, agricultural development manager at Karcher.
“Cold water machines are very good but there are significant benefits with systems that deliver hot water – both in terms of the higher standard of cleaning achieved and the reduction in the actual cleaning time,” says Mr Beardsley.
Having the correct water pressure available on site and a machine that will deliver the correct pressure to the surfaces being cleaned are the two key considerations to help achieve an effective clean but Mr Beardsley says: “Don’t get too wound up about pressure.”
“Good water flow is essential when you are needing to deliver 700 litres of water an hour, so it’s important to make sure the unit’s water system can cope with that, although we can tailor machines to suit the water availability if that’s required.”
The Vets View: Phil Hammond, Crowshall Veterinary Services
Proper auditing and getting range management right should be top of the agenda for farmers turning around poultry sheds, says poultry vet Phil Hammond of Crowshall Veterinary Services, Norfolk.
The audit system that accompanies disinfection procedures applied during turnaround is an invaluable tool for producers.
“The independent audit provided by the disinfectant suppliers to the contract cleaners means producers have a means of checking how well, or perhaps how not so well, the procedures have been carried out,” says Mr Hammond.
“It’s in the interests of the disinfectant manufacturers to do this but it’s also a big help to producers. It’s a check to ensure the right products have been used in the right environment and used at the right rate.
“Making sure the correct disinfectant is used that will work effectively within the turnaround time is important. Disease resistance to disinfectants will lead to health issues and poor performance if the wrong product is being used to kill a particular virus.”
But as well as using effective disinfectants the use of desiccant agents is recommended after the shed has been cleaned and before the new birds are introduced.
“And producers also need to make sure they are tackling potential problems from gut viruses and respiratory viruses by using a virucidal disinfectant.
“There may be worm issues affecting laying hens. Worms can build up in the house as well as on the range so if there have been worm problems in the house we advise using Cresol at a high rate to will kill the worm eggs.”
Mr Hammond says it’s just as important to consider the cleansing of the range used by free-range hens as part of the turnaround routine.
“Managing the range’s worm burden by harrowing the field to break up the surface as well as benefiting from exposure to sunlight for a couple of months is very important.”
Dividing the range area into paddocks for rotational access will give birds fresh ground every four weeks. And attention to drainage to avoid poaching and to cleaning beneath slatted areas which have been installed in places of high “hen” pressure, should be part of the turnaround procedures.
Mr Hammond says producers should be vigilant about maintaining clean water supplies. “Clean water is critical to poultry health and it’s important to clean the drinker line during a turnaround. And we always recommend the use of a hydrogen peroxide cleanser to completely remove the biofilm in water systems.
“Farms should also have an on-going water hygiene policy for all drinking systems. Feed bins also need to be considered during turnaround to control risks from salmonella and we would advise a total clean-out or the use of a formalin gas bomb.