Dairy wins sustainability award and reduces energy costs
Buckwell Lodge Farm won VetPartners dairy sustainability award this year for its work on improving genetics, cow health, grassland and soil management.
Father and son team, Marcus and Sam Hunt, have also offset higher power charges this year with a 50kW wind turbine, which generates 75% of the farm’s electricity.
This also enables them to meet Arla’s requirement for organic milk producers, which states that 100% of their energy should be renewable.
The remaining 25% is bought from a renewable electricity provider.
See also: How to prepare for wind turbine planning issues
Farm facts – Buckwell Lodge Farm, Lutterworth, Leicestershire
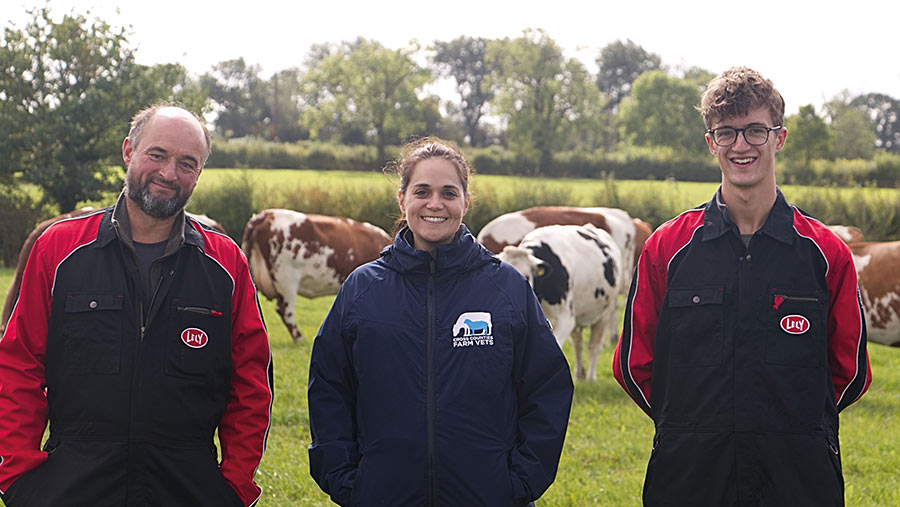
L to R: Marcus, vet Alba Moran and Sam © MAG/Rhian Price
- Farming 138ha (340 acres), all grass
- Milking 80 cows through two Lely robots
- Calving May to September outdoors
- Producing 6,500 litres at 4.3% butterfat and 3.5% protein
- Organic milk sold to Arla
- Running an ABC grazing system
- Three-way cross of Fleckvieh, Norwegian Red and, Normande
- 40 beef calves finished at 20-24 months and sold to ABP annually
- Using Wagyu and British Beef semen after three services
- Two Lely robots and two slurry robots.
- Two sheds each with one robot and a total of 150 cubicles bedded with mattresses and paper
Cow genetics
The duo farm in partnership with Marcus’s parents, David and Daphne, and his wife, Katrina, milking 80 three-way-cross cows at Buckwell Lodge Farm, near Lutterworth.
Cows are grazed for nine months of the year and milked through two Lely A5 robots.
Breeding cows that thrive in this system has been integral to their success.
They previously had Meuse Rhine Issel cows but when they converted to robots, they found the udders were too low.
Instead, they have settled on a three-way cross of Fleckvieh, Norwegian Red and Normande.
“The Fleckviehs give us strength and are dual-purpose,” explains Marcus.
“The Norwegian Reds bring high health and the Normandes have high fat and protein and are producing fantastic beef.”
Finishing
He adds that the Normande-sired calves are easy to flesh off forage and quick to finish. This is important, given they finish all the beef calves they produce.
Calves are multi-suckled, usually to older cows, for 14 weeks before being weaned.
They are fed grass and forage outdoors and are housed for just three months of the year over two winters.
In their final winter, they will be fed 3kg of concentrate a head a day and are finished by 24 months.
The Hunts started multi-suckling calves out of necessity when they bought their first robot in 2011.
“We had 100 cows when we put our first robot in, and we were milking 30 through the parlour, but the novelty soon wore off, so we tried multi-suckling calves,” explains Marcus.
Once four cows have calved, those calves are put on to one cow; after 14 weeks, she re-enters the milking herd.
While only two calves were treated for pneumonia last year at weaning, they are now trialling two-stage weaning using nose tags to reduce stress.
This will see the calf remain with the cow, but it will be unable to drink milk. Then, after five days, the cows will be removed.
The Hunts are taking more natural approaches when it comes to cow health, too.
They use a probiotic from Pruex in the water troughs to help populate beneficial bugs. This is also applied to cubicle beds and, when exiting the robot, cows’ feet are sprayed with the product.
This is reducing cell counts dramatically and has enabled them to treat fewer cows with antibiotics at drying off – 25% this year compared with 36.5% in 2021.
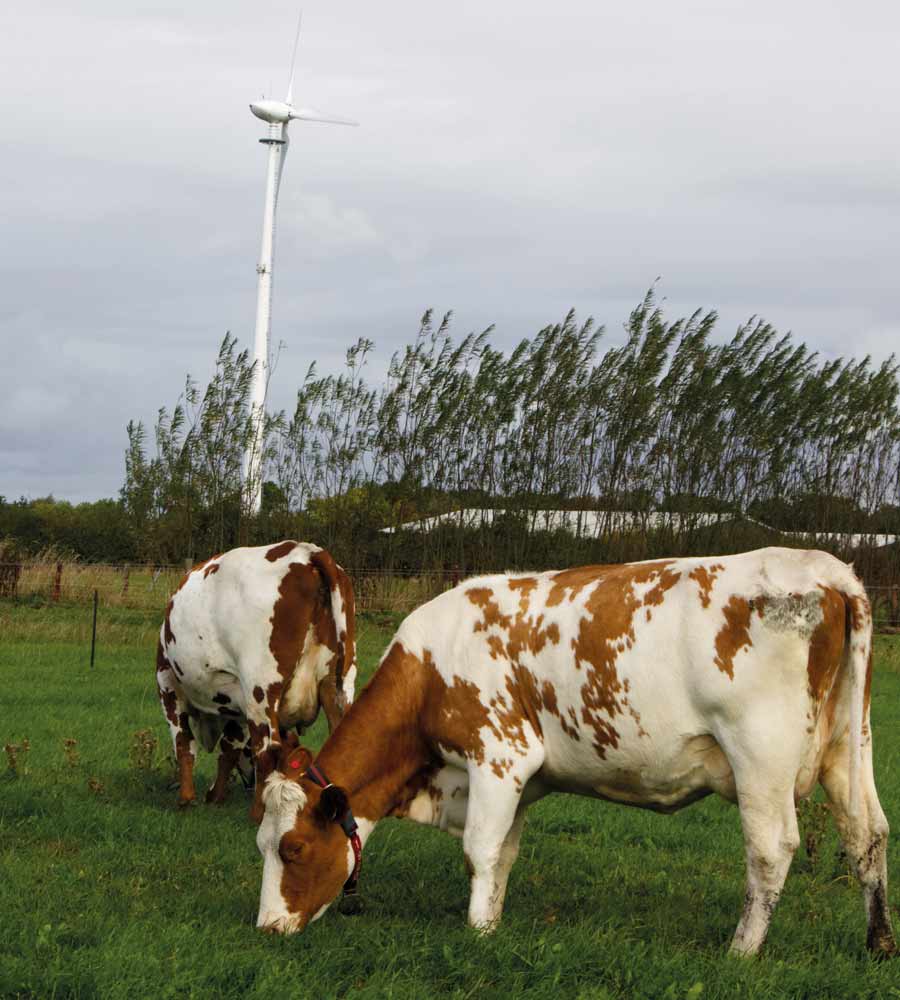
© MAG/Rhian Price
Grassland management
Cows are averaging three visits a day to the robots, which Marcus credits to running an ABC grazing system and keeping cows and heifers separate.
In this system, graze gates at the exit of the sheds provide cows with a fresh bite of grass in a new paddock every eight hours.
Then, when animals enter the shed to be milked, cows and heifers are sent to different cubicle sheds and robots.
This has helped reduce bullying and increase visits from 2.5 to 3.4 for heifers.
They operate what Marcus calls “a wagon-wheel grazing system” with paddocks fenced diagonally off a central track where one water trough is situated. It means less infrastructure is required.
To further reduce costs, tracks have been laid using woodchip. Willow trees have been planted to soak up moisture and stop the tracks becoming waterlogged.
These will also be coppiced and woodchipped in coming years to top up the tracks. Closer to the sheds, walnut trees have been planted because they give off a pheromone that repels flies.
The Hunts officially converted to organic more than a year ago but say they were organic in all but name a lot longer ago.
“We have not used nitrogen for 15 years. Instead, we use clover to fix nitrogen,” says Marcus.
They have been using Better Grass, a biological fertiliser that includes essential minerals and gibberellic acid, a natural plant-based hormone, to stimulate grass growth.
But more recently they have started experimenting with herbal leys. Now about half of the 29ha (72-acre) grazing platform is made up of a herbal mix.
“We’ve been brown and bare [over summer]. We would be in a much better place if we had more herbal leys,” says Sam.
“The grass and clover haven’t come back great while the herbal leys have rocketed away and kept coming.”
Future plans
Because the herbal leys have worked well, the Hunts plan to use more, along with peas and barley as a break crop to clean up the ley and provide protein for the winter months.
Since installing the second robot inside a new cubicle shed 18 months ago, they are using sexed Norwegian Red semen to lift numbers to 100.
They are also considering how to capture and store more renewable energy to become 100% energy self-sufficient.
The downside to the wind turbine is that on low-wind days it does not meet the farm’s demand of 25kWh, while on high-wind days there is no way to capture and store that energy ready for peak demand.
“We need to be able to level out the peaks and troughs so we can use more of our own energy,” admits Sam.
A company is currently trialling battery storage at a site on the farm, and the Hunts believe this could be a good addition to the wind turbine.
In figures
- 3: Average number of visits to the robot a cow a day
- 0.4ha: Size of grazing paddocks (1 acre)
- 20%: The % of cows that receive antibiotics tubes at drying off
- 8-year: Payback period for the turbine when factoring in Feed-in Tariffs (Fits) and energy savings