2016 Farmers Weekly Awards: Pig Farmer of the Year finalists revealed
The Farmers Weekly Awards celebrate the very best of British farming by recognising and rewarding innovation, hard work and passion for agriculture.
Our three finalists combine high welfare with strong business performance to succeed in a highly competitive sector. Karl Schneider reports.
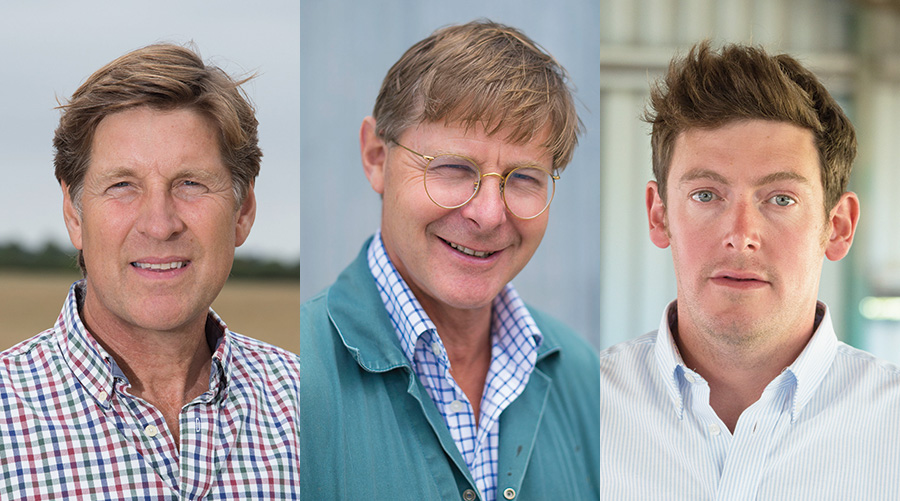
From left: Steve Hart, Robert Lasseter, Tom Wright
See also: Keep up with the latest from the 2016 Farmers Weekly Awards
Steve Hart
Norfolk Free Range, Norfolk
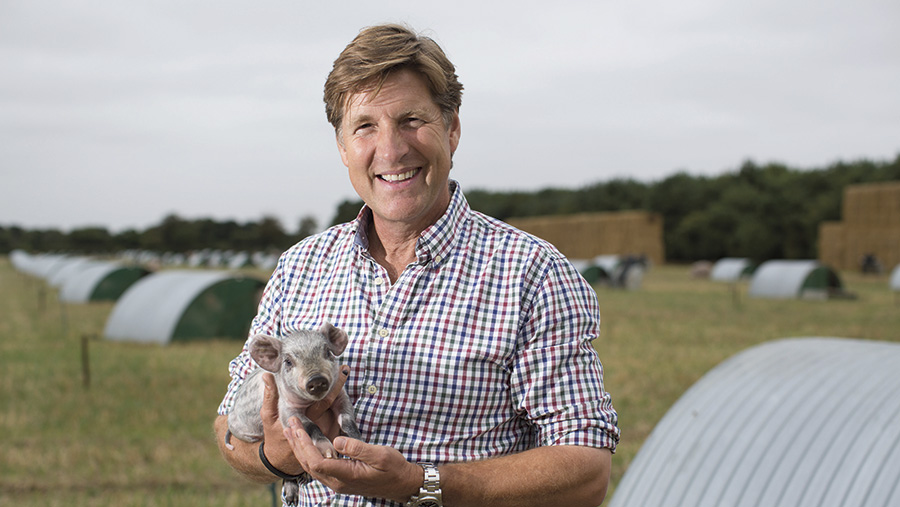
Steve Hart has been breeding his own replacement sows thanks to a close link with genetics firm PIC © Tim Scrivener
In the early 1990s, after an unsuccessful attempt to make a living as a contract weaner producer, Steve Hart found himself in Norfolk with no business and £500 in his pocket – but a burning drive to work for himself.
Today he is a successful high-welfare farrow-to-finish producer, with 13,000 outdoor sows and 75,000 growing pigs, supplying highly demanding end customers including Waitrose, McDonald’s and Chipotle.
His success has been made possible by a clear vision for his business, ongoing innovation, a significant investment in team development – and a lot of hard graft.
Steve’s pig business, Norfolk Free Range, is based near Wisbech on the Cambridgeshire/Norfolk border, but his pig units are spread widely across the surrounding area – access to land is one of the biggest challenges for the growing business.
The judges liked
Strong performance and welfare metrics
Focus on building an effective team
Ongoing innovation
Although Steve runs an independent business, he works closely with his main direct customer, BQP, part of the Dalehead business which supplies Waitrose, sharing ideas and trialling innovation.
Steve runs 10 breeding units for his own business, plus another five where he is contract breeding.
The breeding units operate on a three-week batch farrowing basis, using 100% artificial insemination.
A close link with pig genetics firm PIC led to Steve breeding his own replacement sows.
“We feel this gives us a robust animal suited to our system, and security of supply,” he explains. “PIC’s genetic progression helps to keep us competitive”
Two years ago he switched to single parity herds – keeping sows together from their first litter and not introducing new gilts to the herd – to reduce aggression and help control disease.
Sows are kept until their fifth parity – about two years.
He has also introduced feeding-to-appetite for his lactating sows, through individual ad-lib feeders, combined with clean water nipple drinkers.
In the wake of these changes, output has increased from 23.5 to 25 pigs weaned a sow a year and average weaning weights are up by 0.7kg.
His pre-weaning mortality rate is 10-11% and he is in the process of rolling out bigger farrowing huts to reduce this even further.
Farm facts
High-welfare farrow-to-finish business
13,000 outdoor sows, 75,000 growers – 50,000 outdoors.
400ha of arable – wheat, triticale and millet
Most of Steve’s pigs are finished outdoors, on 15 free-range sites with a total capacity of more than 50,000.
These sites operate on an all-in, all-out basis, with all batches sexed.
They are achieving an impressive feed conversion ratio of 2.4-2.7, with an average daily weight gain of 750g.
He also runs 21,600 indoor straw-based finishing places, including eight new 1,000-place sheds built specifically to supply Waitrose.
Pigs are selected for slaughter by eye. “I have a team for this and that is all they do, so they are experts,” Steve says.
Effective disease control is important for any pig producer.
Steve’s business has managed to maintain healthy herds while entirely eliminating the use of antibiotics in feed.
Water is acidified to help protect growing piglets against disease.
When required, antibiotics are added to the water supply via highly accurate dosage meters usually used in the poultry industry.
To keep tight control of biosecurity the business runs its own fleet of lorries, hauling all its pig food, weaners and finished pigs.
Steve attributes much of his success to the strength of his 90-strong team.
He puts a lot of thought and effort into recruitment, people development and the way his team operates.
“It really is a perfect example of a team being stronger than the sum of its parts,” he says.
Two fieldsmen oversee day-to-day operations, one for the breeding units and one for the finishing operations.
Steve meets them every Friday morning.
“I’m a control freak,” he acknowledges. “I need to know what’s going on everywhere”
Most of his pig units are run by a team of two.
“One of them is in charge, but we make them both feel that they are a manager,” Steve says.
Additional staff work as floaters to help out at individual units at busy times, such as weaning day.
Staff work to a set of standard operating procedures that Steve has developed jointly with BQP.
Managers are given clear targets, focused around improving the quality of weaned piglets and reducing time to slaughter.
The business takes on apprentices from Easton College – six have just completed their apprenticeships and two more are due to start this month. But Steve brings in staff from a range of sources.
“Our challenge is to make this an attractive career to school leavers and path changers alike,” he says.
“It can be really rewarding, as much with a 16-year-old apprentice as a battle weary 50-something who has been made redundant, as they start to feel part of a team.”
Steve reviews staff wages every month – those that are performing particularly well get a pay rise.
Where staff are underperforming, Steve tries to get to the bottom of the problem.
“It often turns out to be something wrong at home, or problems with money,” he says.
Looking to the future, Steve is looking to further expand his business, possibly making a step change in size by acquiring another large pig producer.
He also has ambitions to build his own brand for processed products such as sausages.
He has been looking into the potential for products aimed at specialist consumer markets, such as people on “paleo” diets or those requiring gluten-free products, particularly in the US.
Robert Lasseter
Corton Farm, Dorset
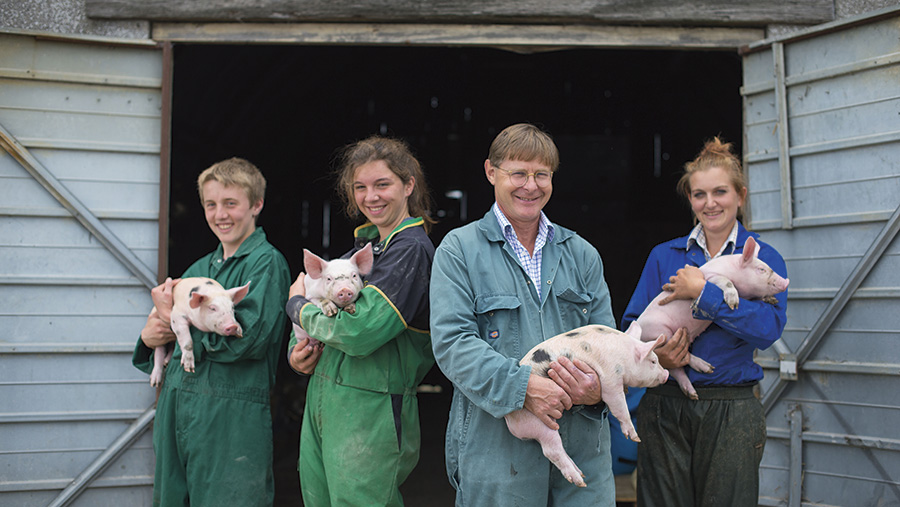
Robert Lasseter believes strongly in developing the skills of his younger staff © Jim Wileman
Robert’s first brush with pig rearing came early in life.
His grandfather gave him £50 for his 15th birthday and used the money to buy a sow at Yeovil market.
After a 20-year gap, building a successful career as a farm consultant and manager, he now runs a 250 sow high-welfare indoor farrow-to-finish business alongside an arable operation near Weymouth in Dorset.
He is pioneering the use of 360deg “Freedom Farrower” farrowing pens, designed to give sows freedom of movement, which he says has improved welfare and output.
Robert batch farrows 29 sows every three weeks, and his primary metric is the total amount of pigmeat produced from each batch.
Farm facts
250 sow high-welfare indoor farrow-to-finish business
Batch farrowing every three weeks
160ha arable business growing grain to feed pigs
“We get paid for deadweight pigmeat sold, so this is what we target and record,” he says.
The target is 21,600kg per batch, which he expects to hit early next year.
In 2014, after a period of research, Robert upgraded his maternity unit with 52 360deg farrowing pens, designed to meet the RSPCA’s latest farrowing standards.
The pens, developed by Martin Baker of Midland Pig Producers, are designed to fit into the same footprint occupied by traditional farrowing crates.
In January the pens, nominated by Robert, won the Oxford Farming Conference and Royal Agricultural Society of England Practice with Science Award, which recognises inventions that result in valuable benefits to agriculture.
Robert believes he was the first UK producer to change all of his farrowing to the new system.
“It’s made all the difference,” he says.
“We went through some pain as an early adopter, but we are through that now”.
He says the main advantages of the new system are:
Sows can express their natural behaviour, such as nest building and eating the afterbirth.
His team works with the sows in the pens, not from behind bars.
- Sows produce more milk, eat more and wean in better condition. As a result, the wean-to-service interval has reduced and birth weights of piglets are improving.
- The greater space afforded results in more teats being used, so they are ready for the next parity
- Weaning weights have increased, which is starting to reduce the number of days to slaughter.
Robert has introduced more measures designed to further improve farrowing performance. These include:
- Using cameras to monitor the reasons for pre-weaning mortality, in a trial with the Food Animal Initiative financed by the Co-op.
- Recording teat numbers and tracking weaned weight per teat. “We have occasionally achieved over 10kg per teat at weaning,” Robert says.
- Adopting AHDB Pork’s best practice farrowing protocols.
- Using green LED lighting in a bid to reduce pre-weaning mortality (shown to reduce aggressive behaviour in poultry though the evidence in pigs is less clear).
- Installing creep feeders in the pens, specially designed to stop the sows accessing them.
Robert is using farrowing arcs on concrete for gilts, which now don’t enter the dry sow house until they have been weaned twice.
He says this is paying dividends: “Second parity drop is a thing of the past”.
Weaned piglets are housed in a nursery building that is 40 years old.
Despite this, Robert says he is achieving outgoing weights on the top 5% growth curve of feed supplier ABN.
He acidifies the water to reduce disease, delivering it through turkey drinkers installed over the past two years.
The herd has been closed for a long time – Robert has not bought a live pig since the turn of the century.
The judges liked
Innovation in farrowing pens
Developing the next generation of producers
Strong involvement in the industry and local community
“This is the core of our stable health status,” he says.
He criss-crosses breeds, using purebred Large White and Landrace alternatively and Maxgrow for the sire line.
Robert’s finished pigs are marketed through Thames Valley Cambac, to Tulip which supplies them to the Co-op.
Robert is a committee member of the Co-op’s Sustainable Pork Group and values the influence this gives him, and the knowledge exchange between producers.
He is also a director of the Oxford Farming Conference
Looking ahead, Robert aims to move to five-week batch farrowing groups of 58 sows. Using the 360degs pens once every five weeks will enable the business to increase the number of pigs sold by about 20%. “This should also enable us to sell weekly rather than fortnightly,” Robert adds, “and so will enable us to tighten up weight range and increase our slaughter weight.”
In time, Robert hopes to be able to pass on the pig business to a young person. He believes strongly in developing young people.
Hannah, a 23-year-old who Robert took on from school when she was 17, handles all of the day-to-day jobs on the farm.
Another youngster, Zak, joined the team in May when he left school. He is going to Kingston Maurward agricultural college – Robert has taken several of their apprentices in the past and has become a governor there.
Robert’s niece, Daisy, is also joining the business after completing her degree,
So it looks like Robert will have no shortage of young hands to pick up the reins when he is ready to hand over control.
Tom Wright
Spring Farm, Norfolk
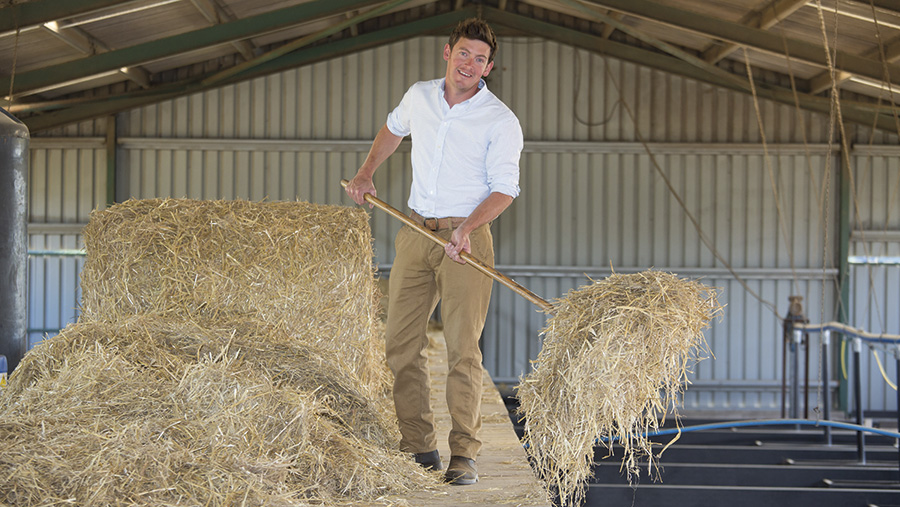
Tom Wright runs his sheds on an all-in, all-out basis © Tim Scrivener
It’s just 10 years since a very young Tom Wright borrowed £180,000 from the bank to set himself up as a contract pig finisher, on a couple of acres of land bought from his father.
Today, still barely in his 30s, Tom is running a profitable 2,000 place contract-finishing business that combines high-efficiency with high-welfare.
He has also built up a very successful business erecting pig-finishing sheds for other producers, based on his own innovative design.
And he has somehow also found the time to build himself a house.
Tom started in 2006 with two finishing sheds he built himself, after visiting as many other pig finishers as he could to study shed designs.
He quickly realised many sheds used for pigs are far from ideal.
The judges liked
Successful finishing business started from scratch
Impressive performance and welfare metrics
Innovation in shed design
“It’s not so common for someone to build a shed from scratch,” Tom explains.
“Lots of straw-based operations are based in buildings that were previously used for something else, so they are not designed for purpose.”
In particular, Tom noted that many sheds were too low to allow for adequate ventilation.
His sheds stand 6.5m at the roof ridge.
A 2m wall along the sides of the sheds is topped by a further 2m of curtains that open and close to control ventilation.
Tom became dissatisfied with the curtain system, supplied by a Dutch firm. So in 2009, when he added a third shed based on the same design as the first two, he looked for alternatives.
Having failed to find another curtain system that he was happy with, he developed his own.
BQP was so impressed with Tom’s improved curtain design that it incorporated it into its own recommendations for pig sheds.
Soon Tom was receiving a steady flow of visitors keen to view his sheds and as a result set up a business to build sheds and supply curtain systems to other
pig farmers.
Tom runs the shed-building business, Spring Farm Systems, with his brother. So far he has completed about 20 new-build sheds and supplied more than five miles of curtains.
The business keeps him almost fully occupied on weekdays, so he employs a pig man to run his own pig sheds from Monday to Friday.
Inside, each of Tom’s sheds has 16 pens running from side to side across the full width, with 42 pigs in each pen.
The pens have a central bedding area and gates at either end of each pen can be pulled across the pens to create scrape passages along each side of the shed, making mucking out a simple process with a mini-JCB.
A canopy can be pulled across the bedding sections of the pens when young piglets first arrive, to help keep them warm while they are small.
The canopy is rolled back as the pigs grow.
The shed curtains are controlled from a panel that Tom developed with environmental control systems firm Climatec, adapted from a system that Climatec supplies to poultry farmers.
The control panel is linked to sensors that monitor temperature, wind and rain.
The sheds on an all-in, all-out basis, with the piglets all arriving on the same day from different breeding herds.
Tom splits the sexes but keeps piglets from the same source together. “It keeps them happier,” he says.
The sheds are disinfected between batches to control the spread of disease.
The key metrics Tom focuses on are feed conversion ratio (FCR) and pig mortality. BQP runs league tables on these and other metrics and Tom is regularly at or close to the top.
His FCR is running at an average of 2.2-2.4, with mortality averaging 2.7%.
No doubt, the pleasant environment in Tom’s sheds helps to keep stress levels down and contributes to his strong performance metrics.
Farm facts
2,000 place contract finishing business
Pigs grown indoors on straw
Spin-off business installing finishing sheds and curtain systems
And having happy pigs also means he doesn’t have a problem with tail-biting.
Due to his success, Tom’s farm regularly gets visitors keen to view his sheds and his pigs, often pointed in his direction by BQP.
He recently hosted a group of New Zealand lamb producers on a UK study tour and has also received visits from South Korea and Canada.
Tom is looking to further expand his pig business.
He hopes to bury electricity cables running across his existing site that will enable him to add two to three more sheds.
And is looking for another suitable site in the surrounding area, far enough away from houses but close enough to a water supply and other services.
He is also in the process of diversifying his business – he recently got planning permission to set up a campsite on some land that he bought last year, 12 miles from his home farm.
The plan is to sell his own sausages and bacon through the campsite shop.
Based on his impressive track record to date, few would doubt Tom’s ability to realise these ambitions.