Tips for maximising AD plant performance
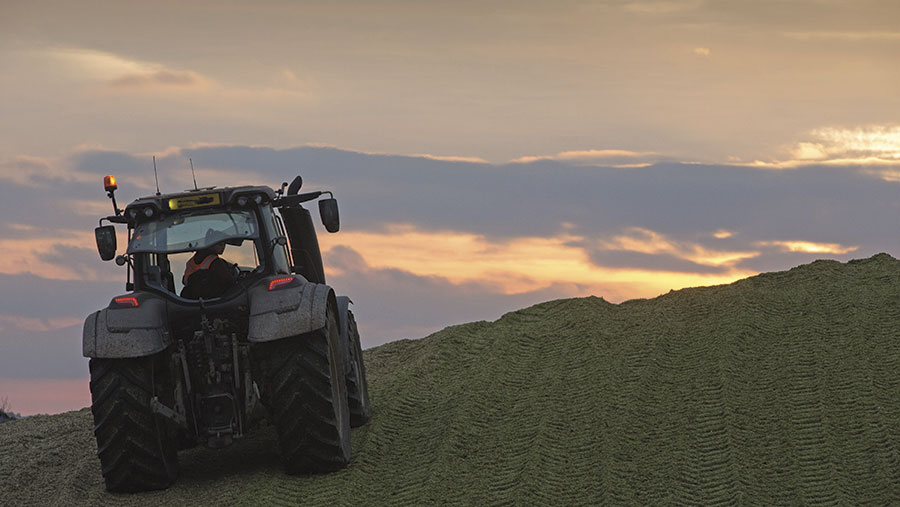
There is scope for operators of farm-based anaerobic digestion (AD) plants to improve biogas yields and increase efficiency.
Analysis of German and Austrian biogas plants by Phil Hobbs, technical director for renewable energy project funder Privilege Finance, found efficiency improvements of 10-30% were possible and he believes similar gains are achievable for many UK plants.
“From a farmer’s viewpoint there are three key areas to focus on, namely: feedstock, mixing and monitoring. All are closely interlinked,” he says.
Feedstock
The quality and mix of feedstocks used is the biggest factor affecting gas yields and offers the greatest scope for improvement, says Dr Hobbs.
Gas yields vary greatly, with maize silage typically ranging from 150-210m3 per tonne (fresh weight), grass silage at nearer 150m3/t, farmyard manure at 80-100m3/t and cattle slurry 20-25m3/t.
See also: Farm energy legal pitfalls and how to avoid them
Seasonal factors influence the type and quality of feedstocks available, so careful planning and monitoring is needed to ensure the right mix is maintained throughout the year, he says.
Digester bacteria requires a suitable ratio of carbon to nitrogen for their metabolic processes, so the C:N ratio is key to gas yield, Dr Hobbs adds.
This can be accurately assessed with a lab test, although guideline values for different feedstocks are available. The ideal ratio for microbes is 24:1.
Manure or slurry contains a lot of nitrogen and therefore has a low C:N ratio (e.g. 6-12:1), which means carbon supplies may be exhausted first and excess N is lost as ammonia gas.
Equally, crops have a higher C:N ratio (e.g. 44:1 for maize silage), which can mean N is used first, carbon is left over and digestion slows.
Local availability of feedstocks and type of technology installed greatly determine the optimal mix, but there are other things operators can do to boost gas yields, especially with crop materials, says Dr Hobbs:
Pre-treatment
Depending on dry matter (DM) content, crops typically take 40-100 days to be digested in a conventional AD plant, but pre-treatment prior to entering the main digester improves digestibility and reduces retention times.
A range of mechanical, thermal and chemical options are available. There is an additional capital outlay – typically £1,000 to £100,000 – but gas yield uplifts of 10-15% are possible.
Harvest timing
Harvesting crops at the optimum dry matter is key to any good quality silage and for biogas 33-35% DM is optimum.
Leaving crops too long results in more indigestible lignin, which reduces gas yields. Shorter chop lengths can improve digestibility, but farmers must balance this against increased forager fuel use.
Silage additives
Numerous microbial or enzyme-based additives are available to aid fermentation of materials and improve silage quality.
These can be incorporated on the forage harvester or added to clamps. The former gives a more uniform distribution. Some treatments also adjust acidity to ensure the clamp is at optimum pH for fermentation.
Mixing and maintenance
Poor mixing of digestate within the fermentation vessel has a big impact on gas yields, says Dr Hobbs.
“The first sign of a problem is a floating layer of feedstock inside the digester, which in the worst cases can form a crust that is hard to break and may result in expensive downtime if the digester needs to be emptied and restarted.”
Plants using feedstocks with higher proportions of solids may require more vigorous mixing, he notes.
Good maintenance is key to ensuring mixers work efficiently. “Don’t just wait until gas yield drops and react to a problem. Take a preventative approach with regular monitoring and maintenance.”
Gas quality is a big issue for operators of combined heat and power (CHP) plants and it is essential gas is kept clean. Minimise sulphides and siloxanes. in particular, to reduce engine damage, says Dr Hobbs.
Importance of monitoring
Anaerobic digestion is a 24/7 industrial process, so close monitoring of all aspects affecting performance is essential to get best performance, says Dr Hobbs.
Although many advanced plants have automatic monitoring built-in, simpler or older designs may require more operator involvement.
Regular analysis of digester substrates is useful for identifying potential issues that reduce performance, he says. A lab test typically costs around £500 and can measure factors such as dry matter content, pH, acid:alkaline ratio and trace elements.
“Considering a breakdown costs thousands in lost revenue, the price of testing is relatively small in comparison, so it’s much better to be proactive,” he says.
Advanced near-infrared scanning techniques are also available to accurately determine a range of values such as DM, crude protein and metabolisable energy.
The upfront cost (around £5,000) and annual licence fee (typically £1,000) can be expensive, but there may be scope for a group of operators to invest jointly, he suggests.
Trace elements including iron, sulphur, nickel, cobalt, selenium, manganese and molybdenum are essential for biological activity within the digester and Dr Hobbs says that, with feedstocks varying in their content, close monitoring makes all the difference.
“If any one element is too low, it can be a limiting factor for gas yields.”