Getting the best from an Agribuggy
Power Farmings’ ‘Getting the Best From’ series continues with a look at Kellands Agriculture’s Agribuggy 2500 – a self-propelled sprayer powered by a 132hp, 2.8 litre turbocharged and intercooled engine driving through a four-speed automatic box.
This sprayer has a 2500 litre tank with 24m aluminium booms and among its features are spray recirculation, boom section cut off and an option for GPS guidance.
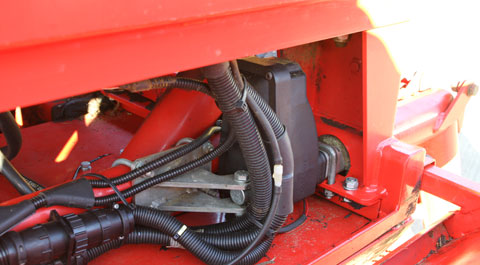
This is the actuator motor which raises the steps to avoid it running in the crop. A mechanical system which uses a worm-drive, ensure it is in working order and safe.
The front grill needs to be kept clean – all the air used to cool the engine radiator passes through here. Also check the tightness of the bolts holding the crop deflector.
The carbon filter for the cab needs to be replaced every seven months.
If there are electrical problems this is the place to start looking. Check fuses and relays for condition and that the whole box has not become a residence for vermin.
Keep hydraulic oil clean – change the filter at least every 1000 hours and more frequently if there has been contamination when the demount sprayer is swapped for a fertiliser spreader and vice versa.
Check tyres for cracks or splits and ensure they have the correct pressure. These Trelleborg 560/60/R 22.5 tyres should operate at a pressure of 8psi.
Check the bolts on the prop shaft for tightness and grease the universal joint regularly.
Check oil levels in the epicyclic final drive by undoing the level plug.
An inspection of the suspension system should discover any excessive wear on the leaf spring shackle bushes. Be prepared to renew.
The ZF four-speed automatic transmission complete with torque converter and transfer box. Oil levels need to be checked through use of level plugs.
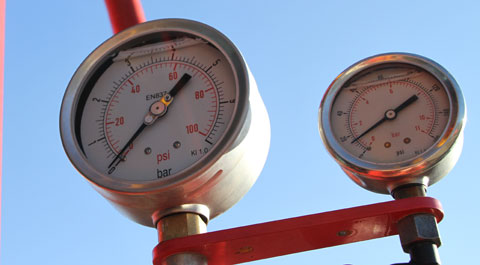
These gauges need to work properly if the spray operator is to monitor pressure and application rate. The one on the right is the Ramsey air pressure gauge and the other one provides the liquid spray pressure. Check for erratic readings which may indicate leakage.
Dry sight gauge for the main tank. Inspect the condition of the cord which connects the tube weight with the float in the tank.
Aluminium booms will not tolerate sudden jerks and jolts. Keep the suspension system well lubricated and give the boom a shake to see if it is working. In particular check wear pads, boom dampers, the centre frame suspension spring and the boom height rubber stops.
Brake-back hinge should be tested by pulling back on the end of the boom. Check the condition of the pipes at this key junction.
With spray recirculation, an air shut off solenoid stops the spray entering the spray jet. When spraying commences the air is used to open the solenoids in all the jets. Ensure all is working as it should be and the air supply pipes are not leaking.
This is the hydraulically powered diaphragm pump with the air compressor on the same drive shaft. Check for operation, pipe condition and that there are no leaking connections.
The Ramsey valve is responsible for rate control. Check for leaks – if there are it will not hold pressure and this will be seen on the gauge by the cab
The suction filter should be inspected at least every week during the spraying season.
Drain the air reservoir tank of accumulated water every day.
Freezing conditions can cause expensive damage to sprayers which have not been properly protected – and it goes a lot further than adding anti-freeze to the engine coolant.
Kellands recommends filling the sprayer with about 100 litres of water and then adding 20 litres of neat anti-freeze via the induction bowl.
This mixture should then be circulated through all the sprayer systems by progressively changing the functions of the machine using the two main taps.
Don’t forget to let some spray out through the nozzles and ensure the clean water tanks – rinsing and hand washing – are properly drained.