How Velcourt cuts grain production costs in tough times
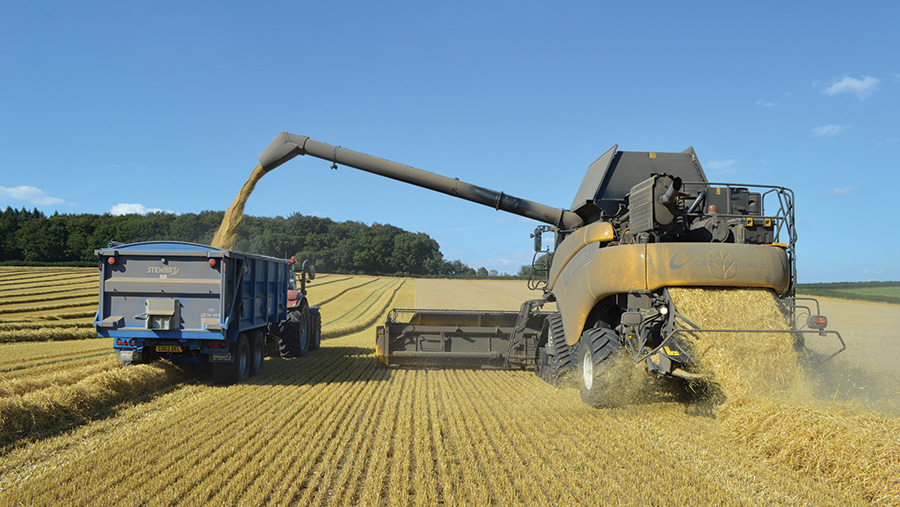
How do you make money growing wheat which costs more to produce than you can sell it? This is the conundrum facing all growers and in particular Britain’s biggest farming company Velcourt.
With production costs for feed wheat forecast by analysts at £135/t and the grain selling about £100/t, it is arithmetic that simply doesn’t add up.
Of course, the £135/t figure is an estimate of a nationwide picture and most would hope to be way under this level, such as Velcourt’s farms director Nick Shorter.
“How do we address this shortfall? We look at all our costs with the efficiency of production being key and this is where there is a huge variation,” he tells Farmers Weekly.
See also: Spring barley comes out as top profit earner in Wiltshire
He adds that the group, which farms 55,000ha from Northumberland to Devon, uses its expertise to push up yields and trim costs, and has a marketing strategy to maximum grain prices.
The £135/t figure includes all costs including rent – and even takes into account subsidies such as the Basic Payment Scheme (BPS) – so everything comes under scrutiny.
Looking at costs per hectare basis, the economic case does not look any more promising. Variable costs for growing wheat at £450/ha to £550/ha – including seed, fertiliser and sprays – are difficult to cut without impairing yields.
This puts the focus on other costs, so the efficiency of labour, machinery and fuel all come under the spotlight, as well as the use of fixed equipment, such as buildings and grain dryers, which together make up another £550/ha.
So a 10t/ha wheat crop is needed to cover the £1,000/ha variable and fixed costs, even before an average rent of say £350/ha is included, which will be somewhat offset by a BPS subsidy of £165/ha.
Mr Shorter points out the group needs to get a lot more than £100/t for its feed wheat and grow more than 10t/ha, while keeping all costs under control.
“Our core focus is to grow as much as possible and sell for as much as possible, while lowering the cost of production,” he says.
Another area under scrutiny for Velcourt is its management agreements which it has with 101 landowner partners, which are typically of a three to five-year duration.
“The relationship of long-term returns from land and the price of land is a key dynamics for us,” he says.
So how does Velcourt grow wheat at a profit. Well, firstly the group’s 42 farm managers are all trained agronomists who make all the decisions.
See also: Cover crops and no-till help beat profit crunch
At its Fonthill Farms unit in west Wiltshire, its average wheat yields are an impressive 10.6t/ha across 650ha of predominantly light land. So what are some of the key decision it takes growing wheat.
Choice of variety
Feed wheats take priority at Fonthill due to the light chalky soils and local demand from animal feed mills
Ed Whitton manages 2,400ha of Fonthill arable land based at Berwick St Leonard, some 12 miles west of Salisbury close to the A303 trunk road.
Five main wheat varieties were chosen for this season, namely Reflection, Revelation, Evolution, Relay and Dickens.
“Variety choice is based largely on yield, good specific weights and good septoria resistance,“ says Mr Whitton.
He adds that wet weather-loving septoria is a particular risk in his area of Wiltshire with rainfall levels well above those seen in the drier East Anglia.
The feed wheat strategy fits in with other crops at harvesting as spring malting barley takes priority over wheat which this season was all harvested in September.
Drilling date
Winter wheat sowing only gets under way at the relatively late timing of end-September to give maximum time to control blackgrass and limit disease development in the autumn.
Mr Whitton can drill his 650ha of wheat with two drills in seven to 10 days which gives him the flexibility to delay drilling into the first two weeks of October.
See also: How wheat genetics can help counter low grain prices
A range of establishment methods such as strip-till and min-till are used with at least two applications of glyphosate used between harvest and drilling to control grassweeds.
Mr Shorter says the group is not tempted to start drilling earlier to make sure all the ground is covered, as he believes that not drilling at all is sometimes the best option with bad blackgrass.
“We do all we can to control weeds before the crops go into the ground.
“Ignoring your blackgrass strategy to get wheat in the ground is what has caused the blackgrass problem in the first place,” he says.
Another advantage of late drilling is that pre-emergence residual herbicides such as diflufenican and flufenacet work better in cooler conditions.
“Drilling in cooler temperature and less sunshine with more moisture does not stress the chemistry as much,” says the group agronomy services manager Tim Mayhew.
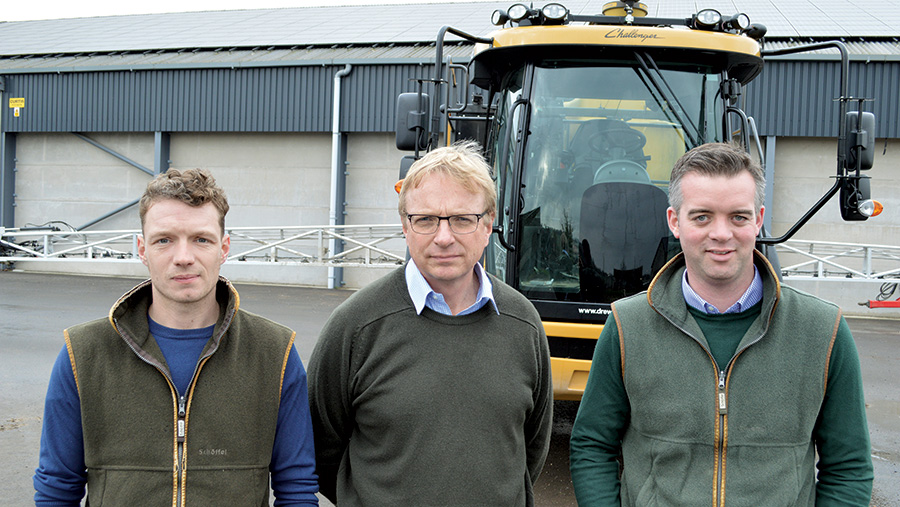
Ed Whitton, Tim Mayhew and Nick Shorter
Disease control
A fungicide programme is worked out using the two main risk factor of drilling date and spring temperatures, but again key decisions are made on individual farms.
Septoria is the main disease risk so the relatively mild winter of 2014-15 put the farm on alert for the disease in the early spring.
A traditional four-spray fungicide approach was used costing about £100/ha to £110/ha, with only minor savings able to be made.
“If you are looking to save money on fungicides, save it early, as the flag-leaf timing is still key,” says Mr Mayhew.
The majority of wheat had a T0 spray of just chlorothalonil to protect against septoria while no azole was used as the use of this fungicide group is questionable in a non-yellow rust area.
In hindsight, the T0 might have been omitted as the spring turned out to be cool and dry, and not conducive to the development of septoria.
Later T1 and T2 sprays were conventional SDHI/azole/chlorothalonil mixes with the T3 head spray being a prothioconazole azole spray.
“These variable costs are pretty fixed apart from some saving at the early T0 timing,” says Mr Mayhew.
Fertiliser rates
This is an area which can show big variations, and compost, sewage sludge and chicken manure are all used at Fonthill to save £30/ha to £40/ha on bagged phosphate and potash fertiliser.
The farm has moved to liquid nitrogen for better accuracy on its 36m tramline system and convenience with no on-farm storage available for solid nitrogen.
On Fonthill’s generally shallow soils over chalk, nitrogen level are towards the higher end of what might be typical at about 240kg/ha, but there is a recognition of having to keep fertiliser levels up.
“If we are harvesting crops of 10t/ha to 11t/ha and 3t/ha of straw then we need to put nutrients back to replace those taken off,” says Mr Shorter.
Good marketing
Varieties are only chosen after talking to farming co-operative Openfield, which markets all Velcourt’s wheat, barley and oilseed rape.
Some 40% of Fonthill’s wheat has been sold at an average of £123/t, good considering current prices of about £100/t.
Last season’s high yields have help compensate for lower prices with winter wheat averaging 10.6t/ha, winter feed and malting barley 10.4t/ha – with even Maris Otter making 6.9t/ha – spring barley Propino yielded 8.2t/ha and high erucic acid rapeseed at 4.2t/ha.
“This year all crops had good yields of about 1t/ha above five-year average on the farm,” says Mr Whitton.