Advice on clamping sugar beet for optimal harvest storage
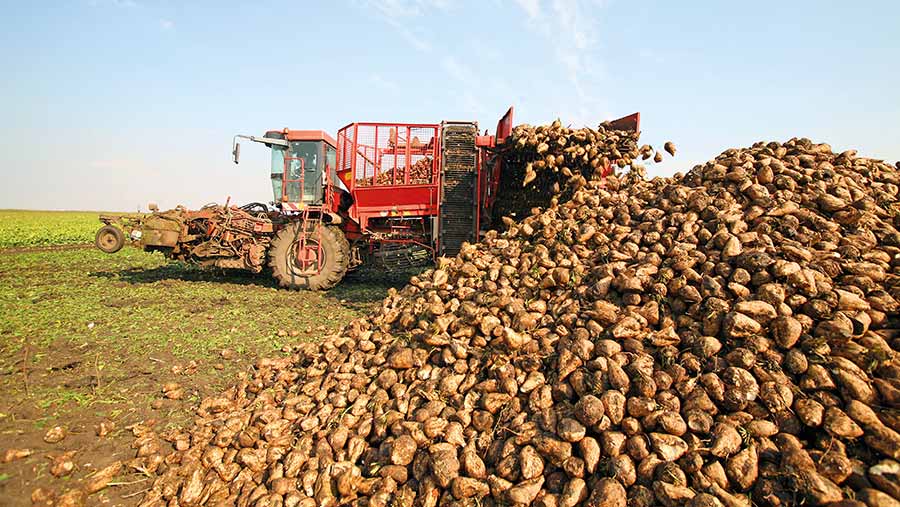
This year’s sugar beet harvest campaign is now under way, and a shortage of HGV drivers is expected to limit crop collection times, which may force some beet growers to store crops on farm.
However, with average sugar beet clamp loss rates at 0.1% of total sugar volume a day, finding the optimal storage technique is essential to minimise these losses.
Beet stored in poorly managed clamps can severely reduce crop quality, leading to financial penalties and even crop rejections.
We take a look at the latest advice on how to construct and manage sugar beet clamps to ensure growers get the best price for their crop.
See also: Why sugar beet variety choice has a role in weed control
Contractor communication
Simon Bowen, head of knowledge exchange at the British Beet Research Organisation (BBRO) advises growers to have good dialogue with their contractors so they are aware of the current haulage situation and can manage it accordingly.
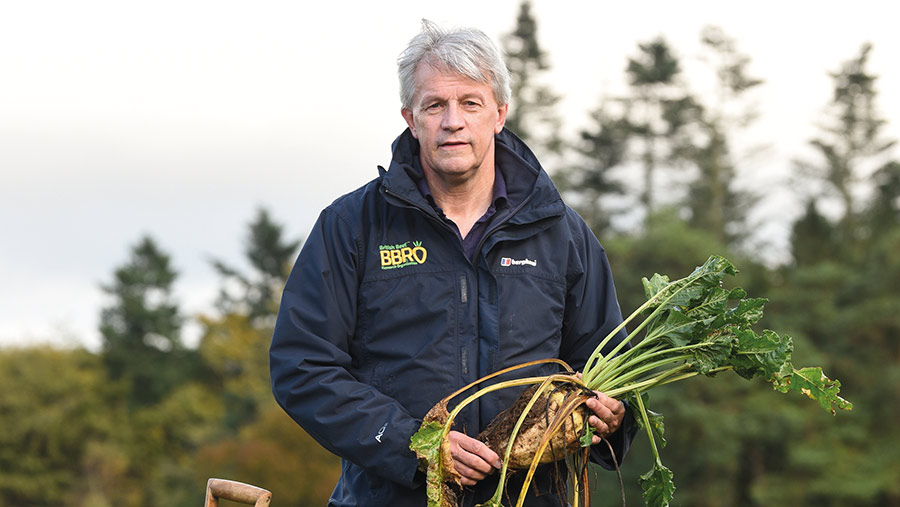
Simon Bowen © BBRO
“Go for just-in-time delivery if possible. Where storage is required, minimise the length of time crops are stored, as the longer the storage the greater the sugar loss, particularly earlier in the season when temperatures are high,” says Dr Bowen.
Ask yourself do I need to lift, or should I leave it in the ground? Once crops are harvested the clock is ticking for sugar loss.
“As long as crops are healthy, they are actively growing and contributing to yield while left in the ground. There is no point harvesting beet if they’re just going into store, which risks sugar loss,” he says.
Currently soil temperatures are still relatively warm at 12-15C, which makes sugar loss three times greater when compared to harvesting when soil temperatures are 5C.
Growers should also only aim to store crops when temperatures have decreased, usually lifted from the middle of October onwards.
If lifting in warm conditions, it’s best to harvest in the evening when temperatures are cooler because sugar beet management becomes easier as soil temperature decreases.
Growers should assess the disease risk of crops. Beet suffering from virus yellows or foliar disease need to take priority when it comes to harvest; lift them and send them to the factory sooner rather than later as these crops are not suitable for storage.
Successful storage
The rate and severity of sugar loss in stored beet depends on how the crop is harvested and handled. The gentler its treatment, the better the crop stores. Key areas of focus should be:
- Excessive dirt Some dirt can help “cushion” beet during loading, but try not to lift soil during harvest as this reduces ventilation in the clamp by limiting airflow between beet.
- Excessive green material Too much green matter can limit air flow in the clamp, which is why lifting beet with care and having good communication with the beet harvester is important.
- Damaged beet Sugar loss is three to four times higher in damaged roots. Machines should be set-up correctly to ensure crops are not handled too aggressively.
- Scalping Don’t over-top the beet by removing too much of the crown, as this can accelerate sugar loss and lead to rotting, mould development or bacterial infection.
- Disease Avoid storing contaminated beet crops as this will inevitably raise the clamp temperature, leading to greater respiration rates and increased sugar loss. Any parts of a field which are infected should be managed separately and not mixed in the main clamp.
Clamp construction
Where it is necessary to store beet on farm, Dr Bowen suggests that clamps should be built in an open area to aid ventilation and cooling.
Avoid siting clamps against the side of buildings or other areas that can restrict ventilation and select a site at least 10m away from overhead powerlines.
The site should have a firm, well-drained base that is suitable for loading and unloading, with no ruts that can trap water or loose beet, leading to hotspots and high respiration rates.
Sugar beet should not be pushed up the face of the clamp. “This will damage beet, compact the clamp and restrict air movement, allowing heat to build up and increase the rate of sugar loss,” he says.
Clamp type
The length of time beet needs to be stored dictates the type of clamp that should be constructed. Dr Bowen outlines the three main types.
1. Early season/temporary clamp
Beet lifted early in the season that requires temporary storage should not be left in the clamp for more than 10-14 days. Such clamps should be made up of individual loads so that trailers carefully tip beet in.
These short-term clamps should not exceed 2m in height, be covered or have retaining walls. They are designed to provide a large surface area to reduce sugar loss through respiration.
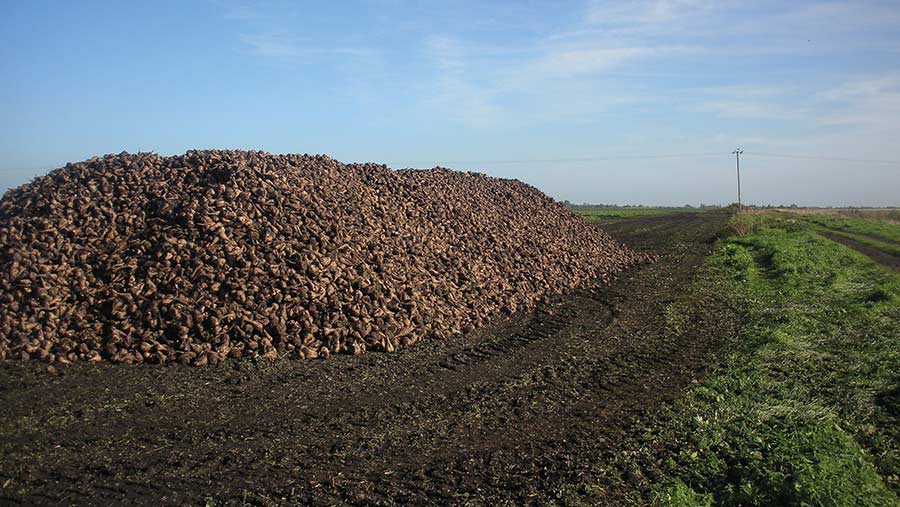
© BBRO
2. Late-season/longer term clamp
Late-season clamps are used further into the sugar beet campaign when longer storage is required.
Clamps should be no more than 2.5m high and constructed using pallets and bales. To help with ventilation, pallets should be placed on a concrete pad, and bales should be placed on pallets with the open end facing outward.
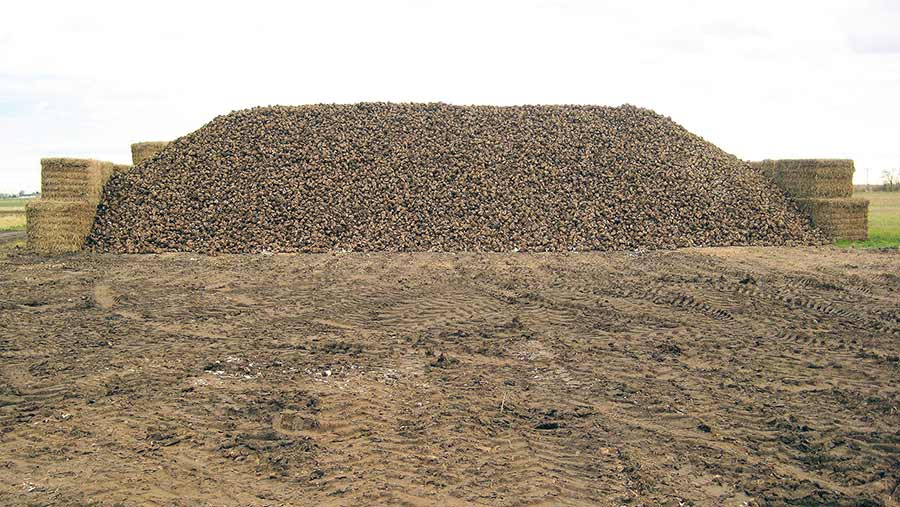
© BBRO
The beet pile should be loaded carefully with a level surface so no frost pockets develop when temperatures dip below freezing.
Hollows between trailer heaps should be filled by tipping loads into gaps with a loader, not pushing up the face.
Clamp sheets should only be used if the ground temperature is below -3C. These sheets are made from polyfelt, which allows the sugar beet to breathe.
Longer term storage isn’t frequently used in the UK.
3. A-shaped/Maus clamp
An A-shape clamp should be built where a self-propelled cleaner-loader is used. The beet must be placed on a flat, rut-free surface in an A-shape of the correct width to allow the machine to operate effectively.
Clamps can be higher than 2.5m, but height is determined by the width of the loader and angle of repose.
These clamps are normally built on the headland, ideally loaded with a harvester or chaser trailer directly, rather than a conventional tipping trailer which runs to the heap.
This will avoid creating ruts in the clamp that could fill with beet and water and create rot problems.