Shock treatment for weeds that resist chemical control
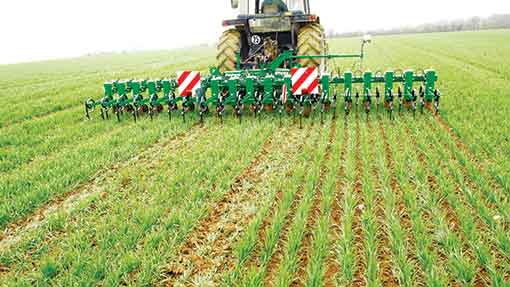
New technologies being developed for weed control such as electrocuting weeds could help growers tackle resistant weeds, cut costs and perhaps reduce the threat of pesticide legislation.
Inter-row spraying is an established technique for controlling weeds in vegetable and horticulture crops. It is now attracting more attention in broad-acre crops, especially where weed resistance to selective chemistry is threatening profits.
Non-selective herbicides are applied using a specialist sprayer fitted with shrouded nozzles to control weeds between crop rows. In vegetable crops the technique is often operated by eye. Now GPS is opening up its use in crops like oilseed rape, maize and sugar beet and could eventually be used in cereals.
Toby Whatley, UK sales manager for Micron, says the company’s Varidome range of front- or rear-mounted band sprayers are proving effective at removing persistent weeds such as blackgrass.
“With fewer active ingredients available for crop protection, these sprayers offer a highly targeted spraying solution, helping to reduce growers’ dependence on selective products. This will also help preserve selective chemistry for future use.”
At the moment the narrowest row width that can be treated is 35cm, which suits arable crops sown in wide rows. Forward speeds of 10-11kph means 60ha/day can be covered using the 9m S5 machine, currently the largest in the range. “Each machine is manufactured to individual customer requirements, to fit with existing crop establishment machinery,” he adds.
Improvements in GPS RTK accuracy could see inter-row spraying being adopted more widely, he adds. “There will be a demand to treat narrower rows in crops like cereals and to go wider with machine design.”
Paul Miller, application specialist for NIAB TAG, says experiments with oilseed rape and wheat carried out during a three-year HGCA-funded study, which finished in 2011, showed the technique had promise and could be used down to 25cm row widths without significant yield loss. “There are one or two people with big blackgrass pressure who are starting to look at this.”
However, he believes widespread uptake could be some way off, even in more suitable crops like oilseed rape. “While we still have a reasonably good selective herbicides such as carbetamide and propyzamide the commercial incentive to switch is limited.
“This is partly because there is a penalty in work rate – although getting better it remains around half that of an equivalent boom sprayer.”
RTK systems and vision guidance have helped accuracy greatly, he adds. “However, the inter-row sprayer has to be matched to the drill to ensure accurate bout matching. Although RTK claims great accuracy, errors can mount up both at drilling time and when spraying. If you are drilling 8m you need an 8m sprayer.”
Cambridgeshire grower Edd Banks, who farms at Manor Farm, Harlton, has been using a 6m Micron Varidome S3 in sugar beet for three years to improve control of resistant blackgrass in the rotation. This year he is trialling the concept on 40ha of oilseed rape.
“Our rape is drilled on 50cm rows using a trailed 12-leg subsoiler. It is less accurate then the beet drill, but we have been really pleased with results so far. We hope to do all the rape and sugar beet next year.”
All crops are drilled and sprayed using RTK Farming’s GPS RTK signal. “It is accurate and repeatable – without this the technique would not be viable on these crops,” says Mr Banks.
The Varidome S3 covers about 40ha a day, whereas his 36m boom sprayer can do four times that. However, Mr Banks calculates he has halved his agrochemical costs in sugar beet, more than compensating for the low operating speed.
As well as spraying diquat between the rows, the actual rows are simultaneously sprayed with a targeted conventional herbicide programme using a 40deg nozzle, effectively treating just 40% of the field. He hopes to do the same in OSR.
“We can be certain that blackgrass is killed completely on at least half the field, leaving much less of a problem for other chemicals to deal with.”
Mechanical weeding
Accurate straight-line drilling of sugar beet using GPS RTK has proved a boon when it comes to hoeing sugar beet crops, says Cambridgeshire grower David White, one of the founder members of RTK Farming, which provides network coverage across East Anglia.
The first pass through the crop still needs to be done by eye, he explains. “It is not possible to set the drill up absolutely centrally and keep it there when operating. During the first pass you use discs on the hoe to prevent soil burying small plants so there is no margin for error – the hoe needs to follow the drill rows exactly.”
Auto-guidance comes into its own during the second pass, when guard discs are removed. “Often rows are closing over so you don’t have a clear line to see. This is where GPS really helps,” says Mr White.
Using RTK guidance in combination with Garford’s digital camera positioning technology could help at the first timing, he adds. “The company says they have got very good results using this combination. It could come into its own for growers who are also getting into inter-row hoeing of OSR.”
Garford’s technical manager Tim Hales maintains the company’s camera-based Robocrop guidance system is accurate to 1.5cm and as such is the best option for inter-row hoeing.
The system is well established in the vegetable and horticultural sector, but interest in broad-acre crops is growing, especially in areas with problem blackgrass, he adds. “We can operate in rows as narrow as 12cm, so it is a realistic proposition for cereal growers as well as oilseed rape, sugar beet and maize.”
Accuracy has been improved thanks to a more advanced camera that records a wider spectrum of colours. Mounting a pair doubles the numbers of rows being monitored, reducing the chance of the machine skipping across a row, which can occur in high-contrast light. Feelers that sense stem bases along a crop row have also been developed for use when rows are closing over.
Speeds of 12kph with an 18m machine are feasible, says Mr Hales. “In France we have a lot of machines working in cereals and oilseed rape. I believe we are likely to see a lot more interest in the UK soon.”
Weed mapping/variable rate spraying
Map-based patch spraying of weeds is moving closer to commercial reality thanks to a Technology Strategy Board co-funded project to refine the technique, led by Agrii in association with other industry partners and Reading University.
The key focus has been blackgrass in wheat. The aim is to generate maps of the weed in fields using cameras mounted on sprayers. Using that information, growers can to apply full rates of chemical where populations are dense and lower rates where weeds are fewer or absent.
“The main attraction is the reduction in herbicide costs,” says Alistair Murdoch of Reading University. “Because the technique relies on information build up at through a season or more it can be used to tailor choice and rates of pre-emergence sprays before weeds are visible as well as on emerged blackgrass plants.”
Less chemical is used which could help preserve some of the more vulnerable actives from being revoked, and there are environmental spin-offs too, he adds.
“Lack of control could also flag up the onset of resistance, allowing growers to act earlier.”
Cameras mounted on sprayer booms capture high-resolution images based on shape, colour and light contrast to identify weeds through the season during normal field operations, Dr Murdoch explains. Their exact location is mapped using the on-board GPS.
It is likely the data will then be transferred directly to a central server to be processed and converted into field maps, which can be downloaded on to the farm computer.
“We are at the field-testing stage,” says Dr Murdoch. “Depending on the industry partners we should have a commercial system ready for launch in 2016.”
Syngenta is taking part in the same TSB project, examining ways of using mapped data through variable rate application.
“The aim is to use a standard pre-emergence application across the field and apply this at maximum rate where blackgrass problems exist and reduce rates elsewhere to maintain effective control of other target weeds,” says Syngenta application specialist Ben Magri. “We started in 2009 and the results have been positive every year.”
Increasing seed rates on areas with dense blackgrass populations can produce a small, but significant improvement in blackgrass control, he adds. On average 95% blackgrass control was achieved using a full-rate Defy/Liberator mix (5 litres and 0.6 litres/ha respectively) on blackgrass populations above 50 plants/sq m.
“Over the four years increasing the drilling rate of Gallant winter wheat from 300 to 400 seeds/sq m and spraying the same full rate Defy/Liberator mix increased control from 95% to 98%.” That additional control produced a £40/ha margin over input cost, he adds.
Most modern sprayers can be linked to GPS systems to alter rates, though it may take some work to get all the equipment talking to each other, says Mr Magri.
However, with the development and adoption of injection systems it will also be possible to switch to different products as the sprayer travels across the field, he adds.
Electrocution
A tractor-mounted “hoe” that electrocutes weeds could offer growers a new way of keeping rows between crops clean.
A prototype currently being put through its paces draws power from the tractor’s power take-off and delivers a 10,000 volt shock via electrode plates that can be positioned to suit different shapes and sizes of weeds, says Rob Diprose, a director within a consortium of companies working with the Allium and Brassica centre to develop the concept.
Like inter-row spraying, it leaves the soil undisturbed, whereas hoeing can encourage fresh flushes of weeds, he explains. “We expect first uptake in field vegetables, but it could be developed for any crop with a defined planting pattern such as sugar beet, and perhaps eventually crops like oilseed rape.”
Gaining safety accreditation is key when working with such high voltages. The company is also working on design features to increase speed. “A forward speed of 3kph is not that exciting,” says Mr Diprose. “We are looking to develop a commercial machine within two years.”
Pros and cons
Inter-row spraying
+ Good control of all weeds in row
+ No resistance problems
+ Less selective chemistry needed
+ No drift
+ Available now
– Slower operating speed
– Needs relatively wide rows
Mechanical weeding
+ Relatively quick
+ Low input costs
+ Narrow rows can be treated
+ Available now
– Relatively dry soils needed
– Can encourages new weed flushes
Weed maps
+ Information captured during normal spraying operations
+ Not real time – information can be used for pre-em applications and actives can be tailored in advance
+ Can be done now by simply drawing weeds areas onto maps
– Not yet available commercially
Variable rate spraying
+ Greater margin over input costs for herbicide used
– Needs mapped data – currently time-consuming to gather
– Equipment compatibility can be a problem
– Available now but mapping/equipment issues need solving
Weed electrocution
+ No chemicals needed
+ No crop residues or weed resistance
– Very slow
– Health and safety problems
– Still in development