Why flax for fibre could reappear in arable rotations
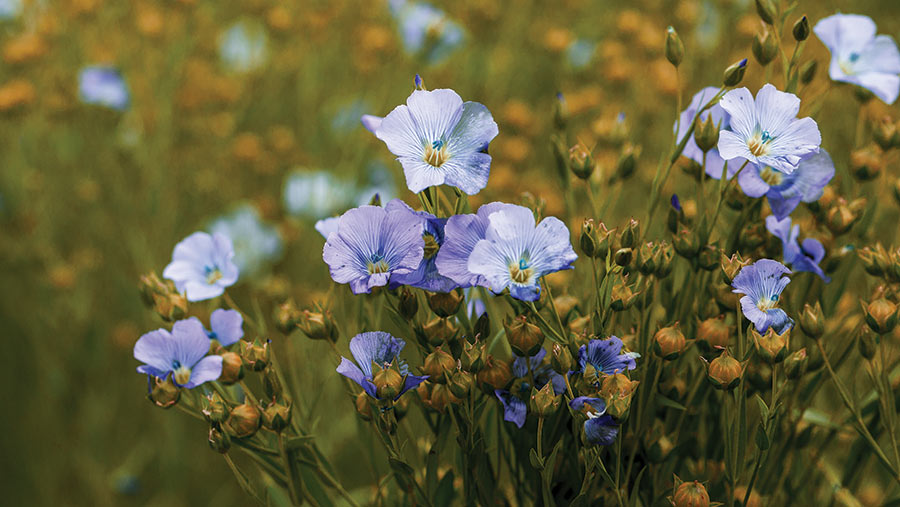
Rising demand for sustainable fibres and the ability of crops such as flax and hemp to capture carbon from the air could see their return in arable rotations, offering farmers an alternative income.
They are also attractive in being true break crops for cereals that do not need heavy chemical use.
Farmers Weekly looks at two separate projects aimed at helping to re-establish fibre crops growing in the UK.
See also: Why Yorkshire farmers are growing miscanthus and hemp
Project 1: High carbon capture cropping
Growing demand for low-carbon natural fibres in construction, defence, aerospace and automotive manufacturing could see the revival of UK fibre crop growing, with the help of a £5.9m Defra-funded project.
Fibre crops, hemp and flax is one of the four cropping options being investigated by the Centre for High Carbon Capture Cropping (see “High carbon capture cropping”).
High carbon capture cropping
The Centre for High Carbon Capture Cropping (CHCx3) is a four-year, 22-partner project, led by Niab.
Its aim is to help UK farmers and growers target net zero and build farming resilience through diversifying their arable and forage cropping.
There are four cropping options being investigated:
- Cover crops
- Annual fibre crops (industrial hemp and flax)
- Perennial food, feed, and forage cropping (including perennial cereals and herbal leys)
- Perennial biomass crops (miscanthus, willow and poplar)
Leading the crop genetic resource component of fibre crops, hemp and flax is Heather Oldfield, business development manager at Elsoms, who has spent time working in the natural fibre crop sector with the company.
Market potential
Heather believes there is huge potential for UK fibre growing and points out that Europe, which is the biggest flax grower in the world, has had its second poor harvest in a row, due to extreme weather.
In addition, the Netherlands, which is a big grower of the crop, is seeing increased pressure for land being taken from farming.
Therefore, manufacturers have increasingly been looking to the UK to potentially grow the crop.
Heather adds that there is a long history of fibre crop production, processing and manufacturing in the UK.
Another attraction is the strong prices fueled by increased demand for fibre.
“Flax returns are the highest they have ever been, due to poor harvests in Europe and increased end user demand. Long fibre is trading at £1.90/kg.
Given a typical 6t/ha retted straw yield, she says there is potential for a good return.
But for growers to benefit from this market, work is needed to develop UK expertise, and this is where the four-year project comes in.
The aim is to identify the best varieties for the UK, look at crop agronomy and also link up the various parts of the supply chain.
Variety
At the heart of the work is the on-farm trials, and last year there were four sites. Each had a 10ha trial area containing replicated blocks of six flax varieties and five hemp varieties, resulting in the project’s first harvest last summer.
Elsoms is working with researchers at the University of York, building on several years of expertise to improve crop variety traits to meet the needs of developing markets that are best suited to UK conditions.
With flax, Elsoms has a long-standing partnership with Dutch breeders Van De Bilt, and they are working together to identify those that may be suitable in the UK.
“The Netherlands is not that far from the UK and has similar conditions,” says Heather.
Processing and testing
Hemp is being processed at East Yorkshire Hemp for uses in construction materials, insulation, mattresses, textiles, woven and non-woven composites, and low-carbon alternatives to products such as plasterboard.
All varieties will be kept separate throughout the processing to ensure products can be tested, and any differences noted.
SHD Composites, who are leading the way in Natural Fibre composite research and solutions, will perform a number of tests, including strength of woven fibres and suitability for end markets.
This will enable identification of varietal traits for more specific end uses.
Agronomy and growing
Another part of the project is to develop expertise in growing the crops to enable growers to produce quality fibre.
For example, while hemp doesn’t need tramlines as no inputs are needed, it does need a fine/level seed-bed.
Heather explains that an uneven seed-bed leads to uneven establishment. Ideally, the crops all need to be the same height for high-quality, consistent fibre yield.
Flax is more delicate than hemp and also needs good seed-beds. The aim is to produce a single stem on each plant, so requires careful management, weed control, and a high seed rate to avoid tillering.
Flax doesn’t suffer much disease, but crops may need some weed control early on and farmers have to rely on Extensions of Authorisation for Minor Use, with flax being classed as linseed on the label.
However, some herbicides can affect fibre quality by checking growth. “The aim is to produce flax stems 90-120cm in length.”
Therefore, the project is looking at herbicides to determine what chemicals farmers can and can’t use to maximise fibre quality.
Harvesting and retting
This year, only one site was pulled and the rest were cut.
Heather explains that pulling is where the crop is pulled out of the ground using specialist equipment with about 5cm of the root still attached to the stem, leaving behind the fibrous roots.
Pulling results in longer fibres and the aim is to have more than 1m. Next year, we aim for all the flax trial sites to be pulled, she says.
The fibre is then turned with a special turner and baled with a special baler to retain longer fibres.
In contrast, hemp is cut with a cutter or drum mower and is turned and baled using conventional equipment.
Between cutting/pulling and baling, the fibre is retted, which takes about three to six weeks. This is the riskiest period for the crop, as it is open to the elements.
Early lessons
One lesson already learned was that any overwinter cover crop must be fully incorporated before fibre crop drilling. “Fields need to be cultivated to get the good seed-beds that the crops need.”
Another was the importance of drill timing for flax. The threat of flax beetle means the crop needs to be drilled when its cooler – ideally, end of March/early April.
However, delays in securing the Home Office licence for the hemp crop meant both crops were drilled in early May.
While flax beetle was not a problem last spring, it did mean it was getting a bit late baling the fibre, increasing the risk of the weather turning during the retting process.
“We just about got away with it this season and it has sharpened our minds for future years.”
But overall, she is really pleased with how the crops grew.
“Hemp reached 3.2m high and flax at 1.2m meant we managed to hit the European gold standard for both crops.”
Future
The project is ongoing and next year will see it expand to six sites. Another key piece of work is generating the carbon footprint data for end users, backing up the green credentials of natural fibres.
“Ultimately, our aim is to create a viable supply chain and demand so growers have the confidence to grow fibre crops.
In turn, end users will have the confidence that contracts will be fulfilled with the required quality.”
Green markets
The construction, aerospace and car manufacturing industries are all looking at their environmental credentials and have net-zero targets to meet.
One way to cut carbon is to incorporate natural fibres in their products, having a much smaller footprint than carbon fibre from oil.
Heather Oldfield points to F1 racing as an example, as teams now have to use 15% sustainable materials in making the cars.
The front wings are currently made from carbon fibre, but they shatter into very small pieces during collisions, resulting in races being halted.
If they incorporate flax fibre into the panel, they find they flex and bend more, breaking into bigger chunks.
Ford is also looking at using natural fibres in its new electric vans.
Batteries make them heavy and the manufacturer plans to use natural fibre panels to reduce weight, so that it can increase van capacity.
Project 2: Ancient craft of linen production
A group of Scottish farmers are collaborating with weavers and textile makers to revive the ancient craft of linen production in Scotland.
Flax was grown across Scotland for many centuries for textile and linen mills until cheaper, imported textiles became popular in the 1900s.
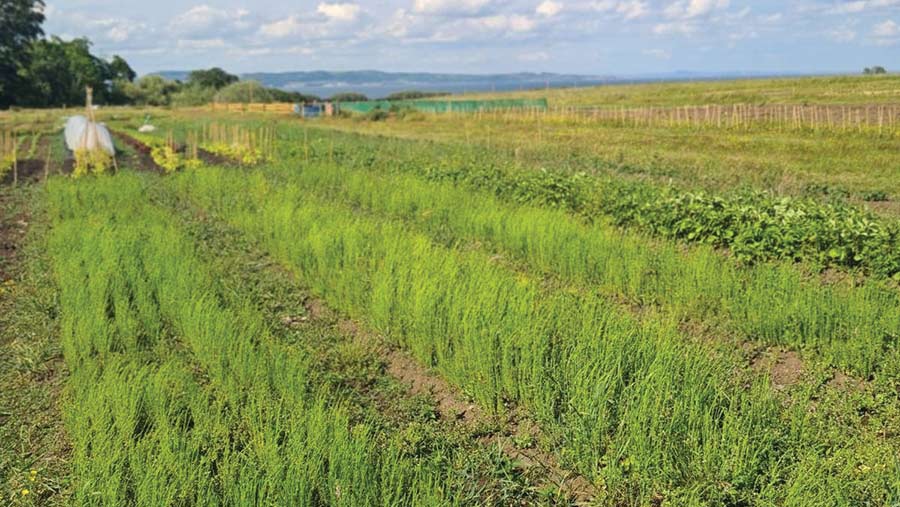
This year’s flax crop at Lauriston Farm growing 1.2m permanent beds © Innovative Farmers
Innovative Farmers is leading a field lab to find new varieties and rediscover lost knowledge on linen fibre crop production.
It hopes to demonstrate the crop as an option for nature-friendly rotations that could meet a growing demand for sustainable textiles.
More plots
Farming consultant and field lab co-ordinator Colleen McCulloch explains that this summer they had three trial farms with small plots and the aim is to double this to six sites next year.
This year, they trialled three varieties – Avian, Delta and Tango – bred in Holland, and next year she hopes to include varieties from other parts of the world with a similar climate.
While the James Hutton Institute is analysing the results, she says initial observations from the harvest are that all three varieties broadly did well.
However, one appears to have performed less well than the other two, growing consistently shorter and less dense across all three sites.
Also weed pressures had a noticeable effect on crop yield. In plots with heavy weed pressure, crop density and height were lower than weed-free plots.
She also noted that plots which previously received compost produced taller and thicker plants.
Exchange knowledge
In addition to the trials, Innovative Farmers is working with small companies and organisations to exchange knowledge and establish the supply chain to process flax into yarn.
It is also looking into larger volume markets such as sustainable insulation.
The core organisations involved in the Innovative Farmers project are the James Hutton Institute and the Edinburgh College of Art.
However, since starting, the network has grown and the organisations involved include:
- Newly established Fibreshed Scotland, a network of organisations working to bring together knowledge and expertise for textiles in Scotland
- Fantasy Fibre Mill is developing a prototype flax processing mill. The aim is to build a network of small processors in farm sheds processing home-grown flax
- Farmers who are interested in growing flax on a commercial scale
“We hope that by working together we can develop a sustainable Scottish textile industry,” she says.