Storage upgrade essentials for potato growers
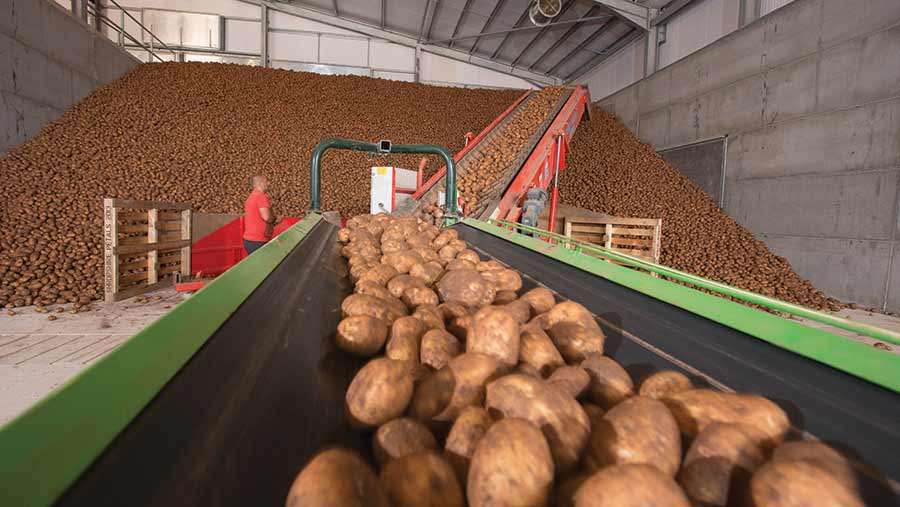
Confidence in the potato sector is low and has led to a lack of reinvestment in storage infrastructure in recent years.
But growers committed to the crop in the long term are urged to pluck up the courage and capital to improve their facilities to reduce losses, cut costs and maximise returns.
About 3.25m tonnes of potatoes go into storage each year and AHDB Potatoes estimates just 20% go in to what are considered state-of-the-art, modern stores.
Five storage essentials – old and new stores
Leakage – get an existing store assessed for leaks. Up to 50% of your costs could be caused by leakage in the worst cases, so make sure the building is sealed to ensure only internal crop issues dictate energy use.
Equipment – it is essential to have an automated control system capable of controlling fan speed and monitoring and maintaining the correct CO2 levels within the store.
Air distribution – the whole performance of a store is governed by air distribution. In a bulk store, tapered ducts and laterals that deliver air underneath the floor will help this. In a box store, consider a suction wall designed to produce positive airflow.
Be able to cope with a wet season – your ability to ensure you can load, dry, cure and pull down a crop when conditions in the field are wet could be the difference between a bad year and a very profitable one.
Size – build the store to a size you can manage and can fill and get under control in seven to 10 days. There was a trend of building larger-than- necessary stores in the 1980s. Two 1,500t stores might be better than one 3,000t store.
Adrian Cunnington, head of Sutton Bridge Crop Storage Research, says only those producers who have built the best relationships with processors and packers have invested in storage.
See also: Potatoes growers have two seasons to get stores up to scratch
He adds that this has left a long tail behind that have stores coming to the end of their working lives that are not as good as they should be.
“The industry needs to ensure there is sufficient return from storage and a continuity of supply for the future, which is in the interests of everyone.
“It is an area that doesn’t get enough emphasis and there needs to be more trust between suppliers and markets, which will provide a better basis for making long-term decisions, such as investing in an expensive store,” he adds.
Repair or replace
Whether growers should build a new store or upgrade an old one will depend on the businesses. Mr Cunnington says a good place to start is an assessment of existing facilities.
The relationship with the farm’s customer is again an important element and it can often provide technical expertise to advise growers on their storage requirements and what would be best in a given situation.
However, some growers like to “paddle their own canoe” and come to independent sources for advice, or carry out a self-assessment.
What are your costs?
Capital costs
* Building and depreciation
* Finance
Running costs
* Energy
* Building repairs
* Loading and unloading
* Overheads such as insurance
* Servicing
Crop costs
* Sprout suppressant
* Fungicide/hygiene treatments
* Weight loss (dehydration)
* Quality losses
* Opportunity cost (off the field v storage price)
Guidance for potato storage self-assessment can be found in the AHDB Store Managers Guide (PDF), which offers a step-by-step audit of how well the store is performing.
“Whether there is scope for improvement of an old store will depend on what you have there already.
“For example, where you have a solid steel structure, you may not need to dispense with it. You could perhaps just upgrade insulation, ventilation systems or install a vented floor,” explains Mr Cunnington.
Ray Andrews of Norfolk storage specialist Crop Systems – which carries out store audits, design and construction – says there are many poor-quality stores in use, but with a bit of care about half of them could be made suitable.
He says one of the critical factors is addressing airflow, with some poorly performing stores having as much as 80% of the air going through just 40% of the crop.
“That means 20% is going through the rest, so you are overblowing the majority of the crop to compensate, which increases shrinkage and compression damage.”
He gives an example of a recent Crop Systems project where new louvres – the inlet that controls air coming into the store – for £8,000 and new fans for £3,000 were installed to an old foam-insulated store.
“It now has 25% better air output, using 35% less electricity, though airflow still needs improvement. It doesn’t have to cost a fortune, it is frustrating people don’t look after their storage better,” says Mr Andrews.
Box v bulk storage
About two-thirds of processing potatoes are stored in bulk stores, with the remainder in boxes, while spuds destined for the fresh sector are almost exclusively stored in boxes.
The AHDB storage cost calculator is an online tool that allows growers to use their own fixed and variable cost data, supplemented by average costs from benchmarking data, to track the price-cost relationship month by month. It gives an indication of overall costs, when to sell the crop or how long to store it, along with dehydration and grade-out costs.
Crunch costs to increase competitiveness
The cost of potato storage is a hugely misunderstood area of potato production and is something all growers should get to grips with, according to the AHDB’s Adrian Cunnington.
Storage is the biggest single expenditure for potato producers who choose to hold on to their crops to add value to off-the-field prices at harvest.
AHDB research shows the running costs of current stores have variations of about 300% between the most efficient to the poorest, putting the bottom-of-the-table growers at a huge competitive disadvantage.
Measuring the various cost elements will allow growers to use the AHDB Potatoes storage cost calculator to enter all their data and produce a cost/t figure for their store.
“If you install an electric meter, you can start to pick up information and get a baseline to work to.
“You can then compare yourself to benchmarking data to get a handle on where you are in relation to others and see if you fit into the good, the bad or the ugly. You can then address unnecessary costs to remain viable,” explains Mr Cunnington.
If growers opt for investment in a new store, these market trends will drive the choice between box and bulk. In the current climate, processing potatoes would be better placed in a bulk store.
“Box stores are too constrained for processing as they are small, so bigger bulk stores will give you a cheaper storage cost a tonne, as new boxes aren’t cheap and there is a cost for maintenance,” explains Mr Cunnington.
In the fresh sector, enterprises tend to be smaller scale, so box stores are more suitable, but Mr Cunnington warns if growers opt for a new box store, it must have enhanced ventilation for better airflow and even distribution of CIPC (chlorpropham).
Store design
When confronted with building a new store, growers will be faced with an array of British companies – and an increasing number of European firms – all offering their own variation on the same principle design, developed over a number of years.
Mr Cunnington explains there is no perfect store, but there are many good ones. He advises potential purchasers to visit some existing stores built by suitable designers.
This is particularly the case for the automation computer systems, which can be complicated and difficult to use, so getting a handle on what they offer is crucial.
“I’m a great advocate of auto-control, as I have seen some disasters in manually controlled stores – without it you are just taking a punt,” says Mr Cunnington.
Mr Andrews agrees that auto-control is crucial and is now the most important element alongside optimum airflow to improve store performance.
This is particularly the case as stores have become bigger and large potato units may have multiple stores spread over some distance which are sometimes only checked once every two to three days.
Without a decent control system, problems may not be detected until it is too late, resulting in significant crop losses.
“A good control system may only cost 2% of a decent harvester, or less than 1% of the crop value going into the average store for more than three years,” explains Mr Andrews.
Optimise cooling
Systems can easily be fitted to old and new stores alike and optimise drying and cooling of the crop, control CO2 levels and control fan speeds – significantly reducing the risk of problems occurring and trimming energy costs.
Mr Cunnington says all available systems are capable of doing more than enough for most stores, but the limitation for many is end user education and the store managers’ ability to get the most out of them.
“You can have all the bells and whistles, but if you don’t understand how to use them, it’s a waste of time,” says Mr Cunnington.
“Some are too complex and haven’t put enough emphasis on tailoring the system to the end user, but there are a few companies now offering a more user-friendly package.”
Airflow key to compliant CIPC use
Even airflow and efficient CIPC application go hand in hand. Growers should make this is a priority before the total maximum dose of the sprout suppressant is reduced further in 2017.
Growers will only be permitted to use 36g/t and to counter the threat of residue exceedances and Ray Andrews believes it is possible to work well within the lower limit and still achieve good sprouting control.
“In one modern bulk store, keeping a crop from September to June, we have seen we can use just 22g/t of CIPC and believe we can go lower.”
That was in a modern store, but Mr Andrews says for £2,500-£3,500 in an existing 1,000t store, an inverter can be fitted to slow fans down and reduce the risk of fog accumulating in the roof space.
The issue is a little trickier in box stores, where getting an even airflow and active recirculation – which will be a CIPC label requirement by 2017 – can prove more of a challenge when running slow fan speeds. “A suction wall will do a very good job for about £6,000-£13,000 depending on existing fans and costed on a tonnage basis, it is peanuts. It will pull air back through pallet openings, so it circulates evenly, but you need to ensure it is blown the right way so it doesn’t short-circuit,” says Mr Andrews.
He adds designing and planning box layout is crucial and overloading the store should be avoided, with room to move air over the top of the boxes essential. “The potato business relies on CIPC and without it, we would be in trouble, so growers should be duty-bound to look at these issues and address the problem,” he adds.
Be CIPC Compliant is the potato industry stewardship initiative. You can find more information on the CIPC Compliant website .
Case study
Yorkshire estate invests in state-of-the-art bulk store
The logistics and extra cost of renting third-party box storage encouraged North Yorkshire-based Fridlington Farms to invest in its own 3,000t bulk store three years ago.
The 1,200ha enterprise at Sutton-on-the-Forest, eight miles north of York, grows about 243ha of potatoes, with 4,000t on contract for processing giant McCain and the rest for Walkers crisps.

Matthew Wallace
About 90% of the crop goes into storage annually, which is where the business tries to add value to its product, says arable manager Matthew Wallace.
“The contract price for green tops only just covers cost of production, so we try to make a margin by storing the crop for as long as possible,” he explains.
Before the new store was built three years ago, the farm had its own storage and supplemented that with renting space, which incurred extra cost in rent and haulage.
Mr Wallace says the potatoes weren’t storing well either, so they decided to bite the bullet and bring the whole process under their own control.
“We decided to go for bulk storage due to the initial and subsequent maintenance costs of boxes, but also because of better airflows, less weight loss and more efficient CIPC and energy use,” he adds.
Cool concrete
When deciding on a store, Mr Wallace looked at three different systems and settled on Norfolk storage specialist Crop Systems’ design after looking at two of its stores and being impressed with build quality and finishing.
The farm also opted for an all-concrete construction, which will last much longer than less expensive wooden dividing walls.
“If you are going to invest all that money, relatively it isn’t much more for concrete and you get a 50-year store. With wood, one bad season can cause problems and it may only last 20 years.
“The concrete also acts as a heat sink – once it is cool, it stays cool – so you don’t need a fridge, which keeps energy costs down,” explains Mr Wallace.
Adiabatic cooling
When loading the store, it is crucial to have the fan and cooling capacity to dry, cure and pull down the crop temperature of about 7-8C for a processing crop.
Fan capacity in Fridlington Farms’ store allows these processes to be carried out quickly to reduce dehydration and deal with wet years, maximising returns from the storage period.
This is combined with an adiabatic cooling system, which uses cold water to cool and humidify ambient air pulled into the store, before pushing it through the crop.
“Fridges are expensive to run and dry the air out, which increases weight loss when the fans are running, so adding humidity counters that.”
He adds that weight loss from a box store would be in excess of 10%, but the new store has been down to 6-7%.
“It has also reduced compression bruising, which can happen in bulk stores and make the potatoes unmarketable,” says Mr Wallace.
Minimal CIPC
A tapered plenum – the channel that runs between each bay – and laterals that distribute the air under the crop ensure an even distribution across the store, with airflow tests showing variation across the store is within 5%
This not only ensures there are no rot trouble spots, but has also allowed Mr Wallace to use less CIPC.
“We’ve reduced CIPC use to just three fog applications of 9g/t, giving a total of 27g/t, whereas in their old box stores we hit the maximum allowable limit by April,” he explains.
The even distribution achieves better sprouting control; lower rates reduce cost and residue risk and eases concerns about the imminent reduction in the maximal allowable CIPC limit to 36g/t by 2017.
Full automation
The icing on the cake in the store is the automation system, which uses an array of sensors inside and outside to monitor external air, roof and crop temperatures, store and outside humidity and CO2 levels.
It then reacts to problems itself, such as purging the store of CO2 when levels reach the set parameter, while an energy-saving mode also ensures the store only cools when it absolutely needs to.
All the parameters and data readings are displayed on a touchscreen control unit at the store entrance.
Mr Wallace adds that in a time when margins are low, you need the best store possible to maximise returns.
“In our previous third-party bulk stores we were moving the crop in December to February, but now we are able to have a contract for April to June, which is more lucrative.
“Overall, cost a tonne hasn’t gone down if you include the investment, but running costs have reduced by about £15/t compared with box storage,” adds Mr Wallace.