What Hereford Monitor Farms’ machinery cost review reveals
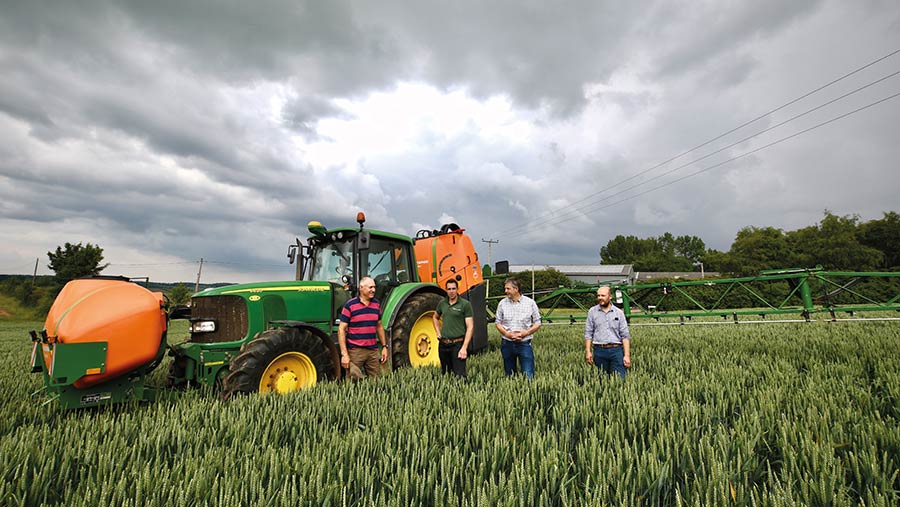
A full machinery review has identified potential savings for the four AHDB Herefordshire Monitor Farmers, which could help their businesses weather the combined effects of the rise in input costs and the decline in Basic Payment Scheme income.
Host farmers Jack Hopkins, Rob Beaumont, Adam Lewis and Martin Carr took part in a full review of their labour and machinery costs, and compared their findings at a recent Monitor Farm meeting, which revealed potential savings of nearly £60/ha for wheat.
Labour and machinery costs make up 25-60% of the total cost of production, and farmers have the ability to change this – at least to some extent.
See also: Cultivation trial shows min-till success on heavy clay soils
As poor availability of new equipment causes second-hand prices to rise, it could be time to consider changes to machinery replacement policy.
Machinery collaboration, joint ventures and keeping requirements for longer could offer possible solutions, says Harry Henderson, AHDB knowledge exchange technical manager.
“There is no right or wrong answer, but it all comes down to individual choice and attitude to risk,” he says.
Is it more cost-effective to own a well-looked-after piece of equipment and keep it for as long as practically possible? Or does it suit the business to have the latest kit every few years? Is there opportunity to collaborate and share machinery with local farmers?
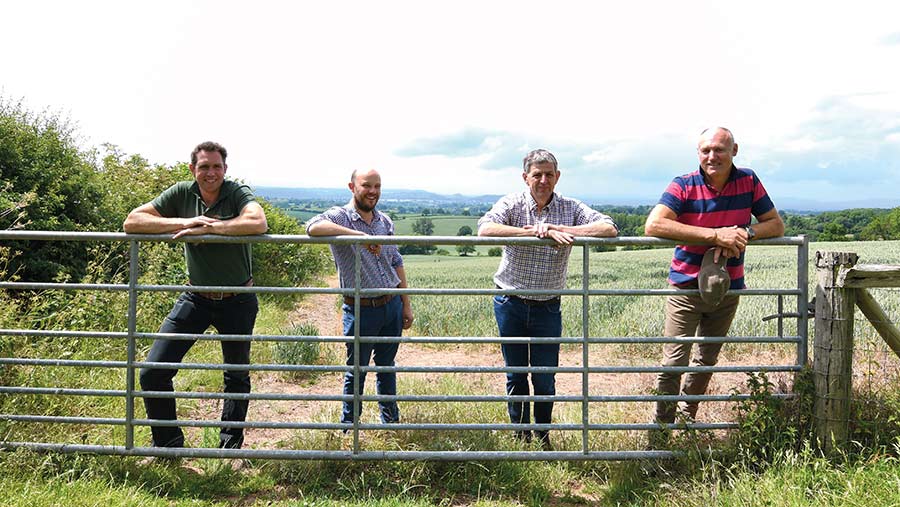
From left: Jack Hopkins, Rob Beaumont, Martin Carr and Adam Lewis © AHDB
Machinery review
The host farmers carried out machinery costings using data from harvest 2020 in a bid to identify potential areas to save money.
Average labour and machinery costs totalled £745,239 across the four farms. This was the equivalent of £1,528.38/ha, explains Rob Meadley, Brown & Co agribusiness consultant, who worked on the project.
“The overall machinery value of the farms reached a huge £2.178m,” says Mr Meadley.
This was made up of:
- £1.4m worth of machines (30 machines with engines)
- £661,000 worth of implements (88 different implements)
- £83,000 of minor items (such as front weights and farm trucks).
However, he points out this included all farm enterprises, incorporating livestock, contracting and estate maintenance, not just the combined 787ha of farmed arable area covered by the four farms.
A further £65,000 was spent on machinery repair costs, £20,000 on insurance, and 90,000 litres of fuel was consumed. A total of 9.25 full-time equivalent staff members were employed across the farms.
Optimum machinery requirement
The total machinery value of £2.178m included four combines, seven drills (including one maize drill) and four sprayers (including one self-propelled).
However, AHDB machinery calculations show a farm of that size would theoretically require just one 30ft combine, one 6m drill and one 30m sprayer.
Obviously, there are logistical constraints to consider, as the farms are spread out across the county, but the contrast in the suggested optimum compared with what the farms had was stark, highlighting opportunities to cut back on machinery expenses.
Thoughts from the four AHDB Hereford monitor farmers
Adam Lewis “There is certainly opportunity for machinery partnerships in farming going forwards, but it’s important for both parties to consider their own objectives first. You need to find commonalities with the potential partner.
“Obviously, finance is a relatively straightforward commonality to find, but this isn’t the only thing to be accounted for. It’s important to outline and agree these objectives before beginning a partnership.”
Jack Hopkins “After crunching the numbers in the machinery review, we can see there is a lot to consider and improve.
“Machinery and labour costs are something us farmers have the ability to change. When buying new machinery, farmers get hooked on the depreciation, but it’s time to turn this on its head and look at the machinery replacement charge.
“There are many benefits of working together with other farmers, such as pooling together skilled operators and specialist machinery.
“I see joint ventures as a good way for people to begin their farming journey by getting themselves on the farming ladder. It could fit well with the transition between someone at the start and someone at the end of their career. Don’t rule out collaboration and joint ventures. There is a lot of opportunities out there and grants are available.”
Martin Carr and Rob Beaumont Mr Carr and Mr Beaumont teamed up to take on a 120ha joint contract-farming agreement at Town Farm, Herefordshire, in September 2021.
Mr Beaumont will specialise in the regenerative agricultural agronomy side of the business, while Mr Carr will take on the more practical machinery side, growing wheat winter, beans, tenderstem broccoli and a spring crop of feed maize.
They plan to carry out a combine appraisal and identify potential methods to reduce machinery costs.
“It’s still early days, but so far it has worked really well. We’ve got lots to learn and we’re up for the challenge – using our two minds together will be better than one,” says Mr Carr.
Scenario set-up
Both Mr Henderson and Mr Meadley then set up a scenario-based costing review, reducing the number of farm machinery and implements across the combined 787ha area.
They included one 400hp tractor, a 250hp tractor, one high-volume self-propelled sprayer, one large-capacity combine and two forklifts. A total of 12 implements, including two 6m drills along with four minor items and a hired-in tractor for the harvest period were also added.
Staff rates were reduced from just over nine workers to two general farmworkers and one full-time farm manager.
The existing farm average labour and machinery costs fell from £745,239 to £381,606.
However, Mr Meadley notes the scenario figure is not directly comparable, as it solely used the arable unit costings, without including information from any livestock and other enterprises.
Therefore, it is most useful to compare between the two reviews on a crop-by-crop basis.
For a crop of winter wheat, the existing farm average was £499.98/ha, while the reduced machinery scenario showed a saving of £58.45/ha.
Like wheat, the majority of crops had a significant cost saving. However, this was not true for winter barley, winter beans and winter oat crops.
This is because these crops were not grown by all of the host farmers, and some were able to deliver these crops cheaper due to their current system – rather than the proposed scenario.
Costing review |
||
Crop |
Existing farm average (£/ha) |
Scenario (£/ha) |
Winter wheat |
499.98 |
441.53 |
Winter barley |
415.76 |
524.79 |
Winter OSR |
413.06 |
371.60 |
Winter beans |
319.26 |
365.71 |
Winter oats |
346.37 |
418.55 |
Spring barley |
463.33 |
359.93 |
Spring oats |
466.47 |
456.11 |
Spring beans |
342.29 |
290.57 |
Q&A with Rob Meadley, agribusiness consultant at Brown & Co
What findings can the four host farmers take away?
This costing review was undertaken in what, hopefully, was an abnormal season (September 2019 to August 2020), with cropping alterations and yield implications. However, the findings show labour and machinery costs may be high, and require further investigation.
The costing is reflective of each business in that specific year, and the mechanics behind the figures explain why something was expensive in that time. This could aid management decisions if action needs to be taken.
How can farmers benefit from carrying out their own costings review?
As farmers we have all this data, but getting management information that can be useful in aiding decisions is often challenging. This level of detail for a costing review can seem daunting, but with professional help and information brought together, it doesn’t have to be difficult.
The outcome can really help decisions in terms of bidding on land opportunities, charging contact rates, assessing the effect of system changes, and labour and machinery enterprise cost allocation to see which enterprises are costing the most and may not be contributing to profit and loss.
What should be done first to tackle machinery costs?
Undertake a realistic valuation of the machinery fleet, including everything in the nettles and workshop. Use realistic market values or, if possible, get the fleet valued (if you can persuade your friendly local machinery dealer).
Review replacement requirements. What machines could realistically be kept longer. Are there any problems – for example, a machine regularly requiring repairs.
Are you putting hours on the right machine? Can work be spread around? Does one tractor do all the work and get the bulk of hours, reducing its value or increasing service costs?
If you are looking to a system change, such as a move to regenerative agriculture, think about what equipment you actually need.
What are your thoughts on machinery shares/joint ventures?
They can be a great way to save costs within a business. But it needs to be with the right people, so the parties can effectively work together and communicate.
An agreement ideally needs to be drawn up and, hopefully, put away in a drawer and not required again. However, the agreement is there as a backstop for the resolution of any issues that may crop up, or to define the exit strategy, if required.
What size combine?
When deciding on combine size, the AHDB advises growers to plan for an average of 20 UK harvest days or 200 harvesting hours, which is adjustable to specific location conditions.
“For example, Herefordshire on average would have fewer harvesting hours, maybe 150-175, compared with the Essex coast, which could be up to 300 hours. This also depends on drying capacity.,” explains the AHDB’s Harry Henderson.
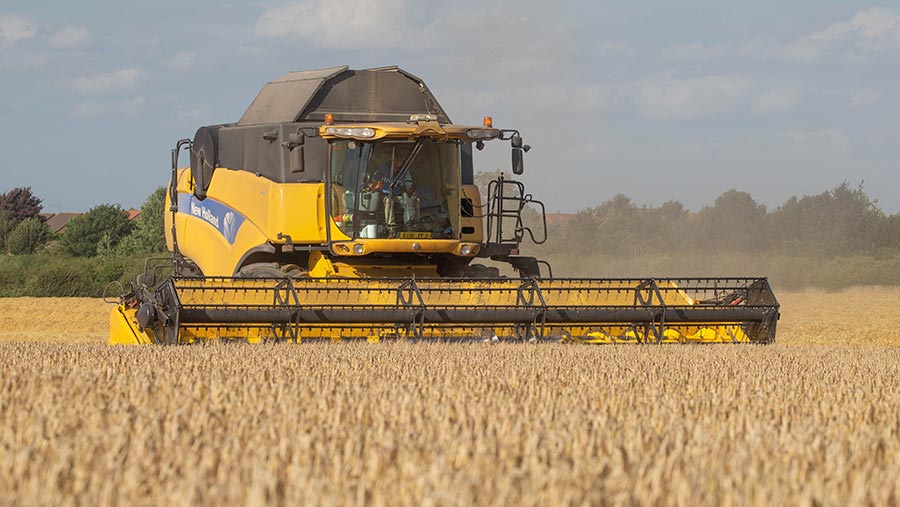
© Tim Scrivener
Assuming an average yield of 4.96t/ha across eight different crops grown on the Monitor Farms, including cereals, oilseed rape and pulses across 787ha, this totals 3,903t of grain.
With 150 harvesting hours, this requires a grain output of 26t/ha. Field efficiency for a combine is somewhere between 65-80%. Assuming 65% in Herefordshire, this would require a machine with a 40t/hour throughput.
What size sprayer?
When selecting a sprayer, operators should assume the entire farm needs covering in three days or 36 hours and opt for a speed of 12-14kph, Mr Henderson says.
“Despite modern spray advancements, this speed is still recommended, with a ‘go low, go slow’ approach.”
Travelling and filling time should then be accounted for, using a field efficiency of 60%. Remember that a bowser and water rates can make a significant difference to this time.
Calculating the required width and capacity:
- Total area (787ha) ÷ 36 hours = 22ha/hour spraying time
- (Ha/hour x 10) ÷ (kph x field efficiency) = boom width, for example: (22 x 10) ÷ (12 x 0.6) = 30.5 (30m sprayer).
This principle can also be used to calculate drill width by considering a given area and required time frame.