Suffolk grower sees big savings with lean management
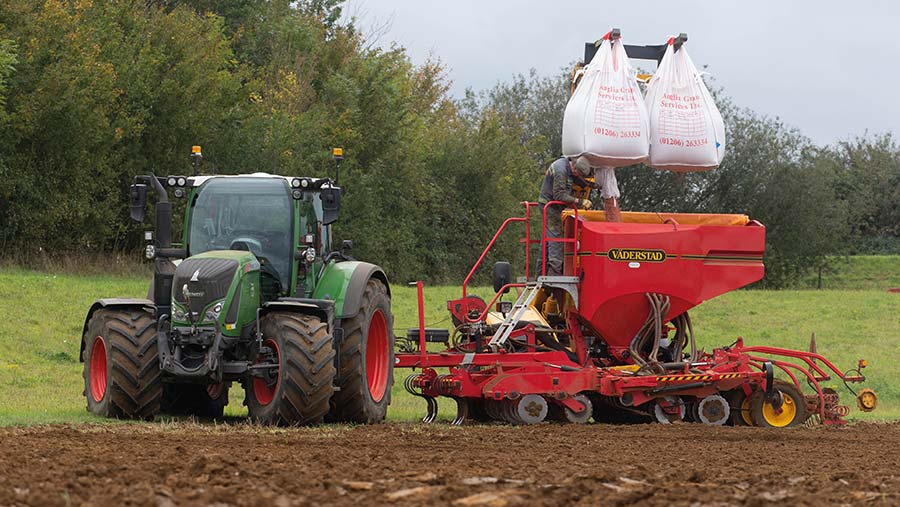
Short videos on setting up three grain drills are part of Suffolk grower Richard Ling’s move into lean management techniques in an overall approach that could benefit him £82,000 each year.
The basic instructions for preparing the drills for action are put on the farm’s WhatsApp group and save the farm staff valuable time re-acquainting themselves with the quickest and most efficient way to start drilling.
See also: Strategy pointers for selling grain in a volatile market
A lean management review of the 1,000ha arable farm revealed a whole series of small measures that, added up, would allow crops to be drilled, sprayed and nutrients applied at the right time to bring about higher yields to result in the big financial gain.
“The benefits will come from the extra yield by improving the timeliness of drilling, keeping on top of diseases and weeds and applying nutrients at the right time,” he tells Farmers Weekly.
Three drills
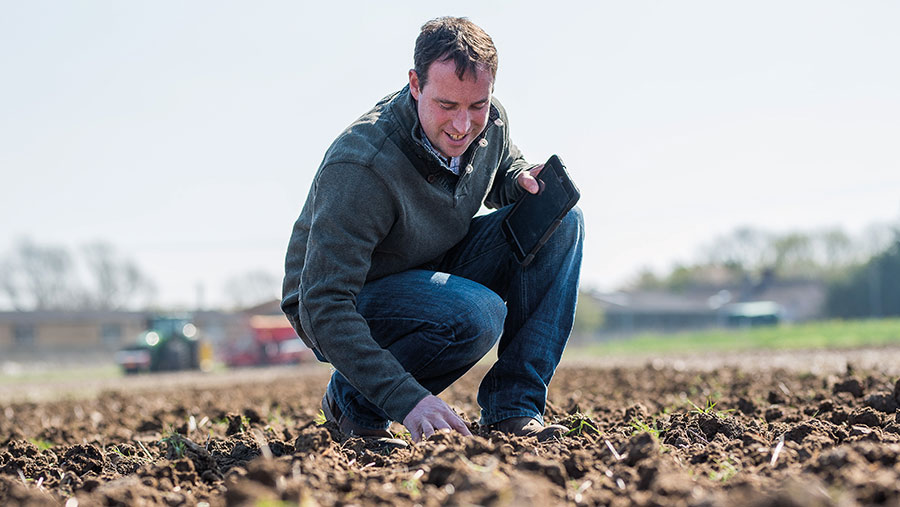
Richard Ling © AHDB
The short videos made by the farm staff remind them how to set up and calibrate the three drills quickly after the gap between spring and autumn drilling seasons.
The farm drills include a Vaderstad 6m cultivator-disc drill and two tined direct drills – a 5m mounted Dale and a Weaving.
The three drills are used to drill the farm’s winter wheat, winter and spring barley, winter beans and oilseed rape across the farm’s soils, which range from sandy clay loams to sandy loams.
Farm staff include Mr Ling and two full-time staff, with two other part-time employees.
The lean management review at Rockery Farm, just south-west of Diss, was conducted in November 2022 and examined the whole drilling process.
It highlighted that easily accessible videos would make it easier to remind staff on the most-efficient operation of the three drills.
In addition to setting up the drills, correct positioning of seed bags in store for easy access for different blocks of land, and better use of trailers to move seed to the field would lead to more timely drilling.
This could benefit the farm £42,000 in increased yield.
The more-efficient working of the drilling process by reducing the downtime to fill drills was seen as a way to cut the estimated 25% of the farm’s drilling plan not being completed on time, and so would benefit yields.
Better timeliness
A further benefit of £40,000 a year could be made by improving the timeliness of weed and pest control and the correct timing of liquid nutrition.
This includes the use of a water bowser to reduce downtime of the sprayers and placing liquid fertiliser tanks at remote units.
Mr Ling is prioritising “easy wins”, such as the videos, setting up white boards for post-it notes of jobs to be done and shadow boards for tools to save time looking for missing items.
Other longer-term aims include streamlining and standardising field shapes.
Lean management techniques to “strip out waste” were first devised in Japan in the 1950s as that nation looked to recover from the Second World War and compete on world markets.
These techniques came over to the UK in the 1980s as Japanese carmakers started building plants in England. It then spread to other manufacturers, retailers and to agriculture.
Neil Fedden, a consultant who specialists in lean management, has worked with six AHDB Monitor Farmers and has identified a total of £514,000 of benefits across the six farms, including the £82,000 for Mr Ling’s farm.
“We initially target £50,000 of benefits, so it is good to see £82,000 on Richard’s farm, and this process can be repeated each year to get even more benefits,” he says.
Neil Fedden was speaking at an AHDB Diss Monitor Farm meeting in January discussing lean management techniques on Richard Ling’s farm.